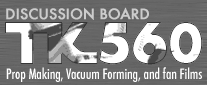 |
www.TK560.com Vacuum Forming, Movie Prop, Sci-fi and GIjOE Forum
|
|


|
View previous topic :: View next topic |
Author |
Message |
drcrash Guru

Joined: 04 Sep 2006 Posts: 705 Location: Austin, Texas
|
Posted: Thu Oct 12, 2006 12:15 pm Post subject: plumbing for 2-stage |
|
|
Ok, so I got a little 0.6 cfm vacuum pump and a little 7 gallon tank and I want to make a two-stage system.
(Those things cost me a total of about $25. The vacuum pump is inside a FoodSaver evacuator/sealer for food bags that I got for $3 at a thrift shop, and the tank is a $20 Wal-Mart 125 PSI pressure "carry tank." The plumbing will approximately double that, of course.)
So far, for testing, I've just been plugging the thing together with 1/4" I.D. braided PVC hose and plastic hose barb fittings. That seems to work great; no leaks, and the FoodSaver can suck the tank down to 20 in Hg in about 5 minutes, or 23.5 in. Hg if you give it three or four more minutes.
I'm thinking that the 0.6 cfm and 7 gallon (about 1 cu. ft.) tank should be enough for a fairly large platen, in a two-stage setup. Usually, anyway.
The usual recommendations seem to be about 23-30+ gallons for a one-stage system for a 2-foot square platen. (Unless I'm wrong and the lower figure is for a 2-stage system.)
If the vacuum cleaner sucks most of the air out to and gets the plastic to basically suck down, I should be able to get by with a fraction of that---hopefully no more than 7 gallons.
Here's my plan so far:
The main plumbing for the vacuum pump and tank is 1/2" I.D. I'm thinking I shouldn't usually need the usual 3/4" or 1" I.D. of one-stage plumbing, because the volume of air to be evacuated will be much lower---by the time the vacuum tank valve is opened, most of the air will already be gone, and rarefying the remaining air won't depend so much on pipe diameter. A quarter the cross-section of a 1" pipe should do okay, because three quarters of the air will already be gone.
I could be wrong about that, in two ways.
First, there may be some cases I care about where the shop vac fails to suck out most of the air, and the high-vac system has to do a lot of the basic sucking down. If I'm forming thick, high "hot strength" plastic, the vacuum cleaner may not do much to stretch the plastic down to the mold, beyond what I did by pulliing the frame down and stretching it over the mold.
I'm thinking that in that case, pipe diameter still won't be critical. The plastic is so thick and hard to bend that it's going to be a comparatively slow process, and the limiting factor will be inches of mercury, not CFM. I'm very unsure about that, though
The second possible problem is weirder. Maybe the main purpose of powerful pumps and/or big vacuum tanks is to compensate for leakage---especially failure to really seal around the edge of the platen.
In that case, CFM and pipe diameter may be more important than I'd otherwise think. If you have leaks that are comparable in airflow to your suckage, you're in big trouble. (For example, if air leaks in as fast as your narrow pipe can carry it out, you'll never get a good vacuum under the plastic, and the plastic may not come down much.)
So if you have significant leakage, there's a big advantage to pulling the plastic down REALLY FAST, before your vacuum leaks away. If you only suck as fast as you leak, you're hosed, but if you suck 10x faster than you leak, the leaks won't matter much. (At least, not not at first. You may not be able to hold the plastic down long enough, though, and it may spring back before it cools below its thermoforming temperature, if you run out of vacuum in your tank.)
Anyway, here's the basic scheme I'm looking at right now:
* a 1" vacuum cleaner connection & check valve, with
* a 1/2" port to the high-vac system ahead of the check valve (i.e., between the platen and the check valve,
* a 1/2" (full-port) ball valve to isolate the whole high-vac system so that I can evacuate the tank
* a tee that splits this into separate paths to the vacuum pump and the vacuum tank, and
* another 1/2" (full port) valve to isolate the vacuum tank after using it, so that the pump can continue sucking air from under the plastic without sucking the air back out of the tank
Code: |
+ - - - - - - - - - - +
| platen |
+-------+ +-------+
| |
| | +-------+ +-------+ +-------------+
| | | 1st | | 2nd | | |
| +------+ ball +---------+ ball +----+ vacuum |
| +------+ valve +---+ +---+ valve +----+ tank |
| | +-------+ | | +-------+ | |
+-+ +-+ | | | |
| check | | | | |
| valve | +-+ +--+ | |
+-+ +-+ | high | | |
| | | vac | | |
| | | pump | | |
+---+ +---+ +-+ +--+ | |
| low | | | | |
| vac | exhaust | |
| pump | +-------------+
+---+ +---+
| |
| |
exhaust
|
I should probably have a check valve just before the high vac pump, to keep the tank from sucking air backwards through the pump if the pump is off... and maybe I should have it anyway; not sure.
I'm also not sure if I should have a relief valve somewhere... or can I get by with relieving pressure through the platen? (If I get a really, really good seal between the plastic and the platen, I might not be able to get the plastic off, even with the first valve closed. I suspect I don't need to worry much about that.) |
|
Back to top |
|
 |
jegner Site Admin

Joined: 30 May 2003 Posts: 2144 Location: Texas, USA
|
Posted: Thu Oct 12, 2006 1:45 pm Post subject: |
|
|
Here is Doug Walsh's idea on a 2-stage set-up:
I was going to try that, but now that I have a Hi-vac pump, and a tank, all I need to do is the plumbing. Heck, I even have the pipe fittings, and the ball valves, just no time to work it. |
|
Back to top |
|
 |
drcrash Guru

Joined: 04 Sep 2006 Posts: 705 Location: Austin, Texas
|
Posted: Thu Oct 12, 2006 11:10 pm Post subject: check valves, cracking pressure |
|
|
What's going on in that picture? Is the rubber band a replacement for a stronger spring that's been removed, or just an addition to a valve where the flap sags open by default?
It looks to me like he's engineering a check valve with very low but nonzero "cracking pressure," i.e., one that requires a little bit of pressure to open it, but not much. That way, it will be closed by default, but even the low vacuum from a vacuum cleaner can open it.
(Cracking pressure is one of the basic specs for check valves, along with diameter and max pressure. For this application I think you'd want a cracking pressure of about 1 PSI, no more than 2.)
I think I know why Walsh is doing this---I've been thinking about the same issues---but I don't like the rubber band. Rubber bands degrade pretty quickly, and eventually break. (A light spring might be better, but I don't really like that, either---too much of a delicate balance there.) If I give away or sell my current machines, as I likely will, I don't want them mysteriously breaking on somebody who didn't build them and won't understand what's going on. (Worse, they might just get poor detail and not realize that the system was actually broken.)
Another way of getting a similar low-but-nonzero-cracking-pressure effect might be to use gravity to hold the flap shut. (Gravity is very consistent and tends to last longer than rubber bands. ) If you have a floppy, unsprung flap, you can mount the valve upside down so that it tends to sag shut instead of sagging open. Unfortunately, that requires running the pipe down from the platen past the valve and u-turning up into the valve, plus another elbow on the other end. That's big and ugly, and introduces a substantial volume of pipe on the platen side of the flap, which will have to be evacuated by the high vac system. (If you have a big pump and tank, that's probably no big deal, but for me it's an issue.)
It may be sufficient to mount the valve horizontally, with the hinge side of the flap upward. Then the flap would tend to sag very weakly closed, parallel to and next to the ring seal, but not actually pressing against it.
That would give it a cracking pressure of approximately zero, so that a small pressure difference could suck it plenty open one way, or suck it tightly shut the other way.
(Actually, depending on the weight distribution of the flap and any resiliency in its hinge, it might tend to sag somewhat open or with a little weight holding it shut. You'd have to play with the particular valve, which makes it hard to shop for online. )
I'm thinking of doing something similar with a ball check valve I have sitting here, mounting it horizontally so that the ball can move freely either way. That way, the low vac system won't have to fight against pressure from a spring or rubber band to keep the valve open, and the high vac system should still be able to suck it shut... I hope.
It's not as easy for the high vac system to suck a check valve shut as you might think. Even if your high-vac pulls 14 PSI, the pressure difference across the check valve flap may be much, much lower. If the high-vac system can't handle much flow, you may not generate enough vacuum in the table and across the flap... enough air may breeze past the flap that vacuum never builds up in the table, and the actual pressure difference across the flap is always low. This is one reason I decided to go with 1/2" plumbing from my tank to my check valve, rather than the 3/8" or 1/4" that I considered. I want to make sure I can suck enough air fast enough that the check valve slams shut. (The other reason is to cope with leakage around the edge of the platen.)
BTW, does anybody here have a working two-stage system where a check valve automatically closes off the low vac pipe? If so, what kind of valve did you use and how did you use it? |
|
Back to top |
|
 |
drcrash Guru

Joined: 04 Sep 2006 Posts: 705 Location: Austin, Texas
|
Posted: Fri Oct 13, 2006 12:17 pm Post subject: sump pump check valve |
|
|
I spent way too long at Lowe's today but that was good, because eventually I stumbled across what seems to be the kind of check valve that Doug Walsh is modifying and using in the pictures.
It's actually labeled a "sump pump check valve"; I had previously found check valves over in the pump section that were just check valves, not "sump pump check valves," and they're different. Glad I looked again.
They only seem to come in one size, 1 1/4" threaded pipe size. (Also fit 1 1/2 unthreaded, apparently.) So I assume that's the right size. (Anybody know?)
Very low cracking pressure... I tried blowing into one, and it didn't take much to open or close it, no matter what the orientation.
That makes me wonder whether it really needs the rubber band hack, and if so, why.
Maybe that's only necessary if you have a really lame vacuum pump, like a hacked bike pump used as a hand vacuum pump with no vacuum tank.
Or maybe it's because a lot of pumps suck in pulses, and you don't want the valve to sag open between pulses---you'll have to suck some air through it to shut it at every pulse.
Anybody know?
By default, I guess I'll get one of those and try right side up without the rubber band first.
Once I get that, a flange to mount it, and a hose barb to glue into it for the high-vac connection, I'll have everything I need to put together the two-stage system.
(If I mount it righteously, with a 1 1/4" galvanized floor flange it just screws into, the flange will cost more than the check valve---$7 vs $6 dollars. I'll probably do that anyway, because i like clean interfaces for experimenting, moving things around, and replacing broken rubber bands.) |
|
Back to top |
|
 |
drcrash Guru

Joined: 04 Sep 2006 Posts: 705 Location: Austin, Texas
|
Posted: Mon Oct 16, 2006 7:29 pm Post subject: |
|
|
Preliminary result from my little two-stage setup, with the sump pump check valve installed right way up and without a rubber band:
Not good. Yet.
My vacuum gauge drops almost instantly from 22 to around 9 inches of mercury when I open the valve to the vacuum tank. Then it drops pretty quickly from there and I'm out of vacuum in a very few seconds.
I think two things are going on here:
1. The check valve is closing way too slowly, and about 4 gallons of air are being sucked the wrong way through the shop vac hose before it closes and the suckage starts to do something useful like sucking plastic down. Oops. I think that's what's making the needle plummet at first.
2. I'm not getting a good seal around the edge of the plastic. My gasket and/or frames need work. I think that's why the pressure continues to drop, less rapidly but still too fast, after the initial plummetting. The sump pump valve might not be sealing well, but I don't know. If not, it might seal better if the vacuum was higher, pulling it more tightly shut, rather than being mostly lost by its not sealing at all for too long.
So far, the high vac is not making a noticeable difference in the pulls, but I think it's fixable. Sucking four gallons of air through the shop vac right off is a really bad idea when you only have a 7-gallon vacuum tank. (It'd make a lot less difference with a 30-gallon tank, but it still wouldn't be good. You'd lose about three inches of mercury immediately.)
Without a vacuum gauge, I'd have no idea what was going on. Well worth the $3.50 plus shipping to Noshok; I should have gotten one before.
For the moment, I may try the rubber band hack. It's tacky and not really permanent, but it should make the valve close a lot faster, and not waste most of my vacuum. For now, it would be fine. I'd like to try mounting the valve upside down instead, or at least horizontally, but here's not a lot of room for that plumbing under my the platen on the little rig, and it might not be enough to get the valve to close really quickly. |
|
Back to top |
|
 |
jegner Site Admin

Joined: 30 May 2003 Posts: 2144 Location: Texas, USA
|
Posted: Mon Oct 16, 2006 8:13 pm Post subject: |
|
|
Good info. Tell us more about that vac gauge.
Links? |
|
Back to top |
|
 |
drcrash Guru

Joined: 04 Sep 2006 Posts: 705 Location: Austin, Texas
|
Posted: Mon Oct 16, 2006 10:06 pm Post subject: cheap vacuum gauges |
|
|
These are the gauges Knightshade was talking about in an earlier thread titled "Vac Guage".
http://www.tk560.com/phpBB2/viewtopic.php?t=334&highlight=vacuum+gage+guage
They're from this vendor on Ebay:
http://stores.ebay.com/NOSHOK-Direct
I got one of these:
http://cgi.ebay.com/NOSHOK-2-5-Dial-1-4-NPT-30-Hg-Vacuum-Gauge-NIB_W0QQitemZ7626815598QQihZ017QQcategoryZ55825QQtcZphotoQQcmdZViewItem
And another one just like it except with the 1/4" NPT fitting on the bottom instead of the back. The link is there somewhere in the eBay store.
The shipping is about $7 dollars for one, or about $7.50 for two. I figured what the heck, what's another $4?
Now I have one on the vacuum former and another around to test things with.
They have them marked two ways. The ones I got are marked in inches of mercury and bar (atmospheres). (They also have them marked in PSI and kg/cm**2.) Unfortunately, the pictures show the wrong scales---go by the text description. The pictured gauges do show the right housing style.
They seem to work fine, and are supposed to be accurate within 2.5 percent of full scale, or about three quarters of an inch of mercury. One of mine reads a little less than a half-inch higher than the other toward the top of the scale, but I figure that anything within an inch is precise enough for my purposes. |
|
Back to top |
|
 |
drcrash Guru

Joined: 04 Sep 2006 Posts: 705 Location: Austin, Texas
|
Posted: Wed Oct 18, 2006 5:26 am Post subject: |
|
|
I did some more testing of the two-stage check valve thing, mostly not very well controlled. To reduce the variability from variation in how good an edge seal I got, I made a simulated leaky platen. (I took my board-with-a-hole in it platen, and covered the hole with a disk with a small hole in it.) That removes variability in leakage, and lets me control leakage by varying the size of the little hole.
It's pretty clear that
1. Mounting the check valve upside down doesn't help enough. It seems to help---the valve usually closes faster and is less likely not to close at all---but it's flaky and variable. How much vacuum you waste before the valve closes varies a lot. (Up to and including it not closing at all and you wasting all your vacuum.) The rubber band helps ensure that it closes, and closes more quickly. It helps more than inverting the valve and using gravity. (That would probably help more if I put a weight on the valve flap.)
2. How fast the check valve closes (with or without a rubber band to help it close) is very dependent on the amount of leakage around the edge of the platen. The worse your seal, the more vacuum you'll waste because the valve closes slowly, too. (Typically a few gallons, assuming it closes at all.) That's why I was losing 4 gallons before.
Using my current rubber band, and with no leakage, the check valve loses about 1/3 gallon before it closes. The vacuum gauge drops less than an inch of mercury when I open the valve, so I've still got about 95 percent of my seven gallons of vacuum. With a larger tank and a perfect seal, the loss would be negligible.
With leakage from a 1/8" diameter hole, it loses a couple of gallons. With more leakage than that, it loses more. With leakage from a 1/4" hole, it loses several gallons and may not close. (It's hard to tell, because it's losing vacuum so fast anyway simply due to the hole.)
That's in my current setup. Your mileage will vary if you have a narrower or wider bottlenecks between your vacuum tank and your platen to the vacuum tank; wider is better.
That makes sense. In my setup, currently, there's are 3/8" bottlenecks in the path to the vacuum tank, due to hose barbs in 1/2" I.D. tubing that have a 3/8" I.D. themselves. This limits the airflow somewhat. An equally big hole can keep up with the flow rate through the other bottlenecks, so you're losing vacuum pretty much full-speed anyway, and there's an easier route for most of that air than pulling the valve closed.
The more your platen leaks, the bigger a pipe you need from your vacuum tank, both to keep up with leaks in general and build vacuum, and to create a pressure differential that will close the check valve. Getting a good seal is a win both ways.
3. If those things are marginal---if the valve doesn't have (enough) help closing and/or you have too much leakage---the results are very variable for reasons I haven't nailed down.
I have two theories that I suspect are both more or less true about the variation. One is that it matters how fast you open the valve.
The other is that the valve hinge has become looser as I've been testing it, as the flexible rubber hinge gets broken in. It seems floppier than when I started, tending to sag further open under gravity.
Unfortunately, I'm not sure how taut my rubber band is, or how taut it should be. That may matter. If it's too loose, it won't help enough and the valve may not close as fast as it should, losing more air. If it's too tight, it may not open far enough, creating resistance in the low-vacuum path. That would reduce the pull-down speed some, and reduce the effective vacuum that the vacuum cleaner could pull---the valve would close a bit before pressure equalized on both sides of the valve, i.e., while pressure in the platen was a bit higher than pressure in the vacuum cleaner hose. (I don't know if either of those effects is significant, or how tight the rubber band would have to be for them to be significant.) |
|
Back to top |
|
 |
drcrash Guru

Joined: 04 Sep 2006 Posts: 705 Location: Austin, Texas
|
Posted: Wed Oct 18, 2006 10:19 am Post subject: big brain dump about 2-stage & check valves |
|
|
(This is a long brain dump about 2-stage system design... it's not fully baked, and I might even be all wrong... so if you're not very interested in grisly details, please skip.)
Here's my current mental model of what happens during a pull in a two-stage system with a sprung (or rubber-banded) check valve to shut off the low-vac path.
1. While the plastic is being sucked down, the vacuum at the platen is very low (i.e., the pressure is almost the same as outside the system), until the point where the the plastic significantly resists bending and stretching.
For reasonably thin and stretchy, easy-to-form plastics, this isn't until the plastic is reasonably well sucked down. Until then, there's enough flow of air and so little resistance that there can't be a big pressure difference.
2. Then the vacuum builds up as the plastic resists being pulled into tighter-radius concavities and tightly around tighter-radius convexities. As Charlie as pointed out, this typically happens very quickly---the vacuum level is nearly nothing for a while, then goes up very rapidly. Until you run out of easy parts of the plastic to pull down, there's enough flow that theres no big pressure difference.
When that does happen, the sprung check valve will almost close, because the pressure is equalizing between the platen and the low vac line, i.e., across the sprung valve. If your system has no leaks and the plastic seals perfectly around the platen, the valve will actually close when the pressure at the platen approaches the pressure in the low-vac line, and the difference is the cracking pressure of the valve. If the valve seals perfectly, it will maintain a pressure difference equal to the cracking pressure---i.e., the vacuum at the platen won't be as good as the vacuum your low vac can theoretically pull, it will be lower by the cracking pressure.
Realistically, it's unlikely to happen quite like that because of leakage at the valve seal and leakage around the edge of the platen. (It seems to me that all of the common platen designs usually leak significantly around the platen.)
What will generally happen is that air will continue to come in, and the valve will stay open just a little, seeping as much air as it takes to stabilize at a pressure (vacuum) difference equal to the cracking pressure of the valve. The cracking pressure will keep the valve shut enough that the airflow through it matches the leakage.
So if I've got this right, the cracking pressure of your valve costs you vacuum at the platen in low-vac mode. If your vacuum cleaner can pull 4 PSI and the cracking pressure is 1 PSI, you'll get 3 PSI instead of 4 because of the resistance of the valve.
If the cracking pressure isn't more than a reasonably small fraction of the low-vac's PSI, and you turn on the high vac, this probably won't matter much. The low vac won't pull the plastic down quite as well, but it will probably do okay and not leave much extra air under the platen for the high vac system to evacuate. The high-vac will do the rest, and the cracking pressure of the valve will help it close fast, and not waste too much vacuum by sucking air backwards through the low-vac line.
But if you sometimes use the system without the high vac, it may matter more. The cracking pressure of the valve directly costs you PSI that your low vac can effectively pull. When you rely on the low vac, you'll get worse performance than if you didn't have that valve in the way, resisting flow. It might keep the plastic from basically pulling down, sometimes and it the lower final vacuum may sometimetimes degrade your detail.
This is especially true (and may be a problem even if you do use the high vac) if the cracking pressure of the valve is "too high"---comparable to the PSI's that the low vac can pull.
For example, if your low vac can pull 4 PSI and the cracking pressure is 2, and you happen to need about 3 to basically pull the plastic down, you're in trouble; in effect you only have 2 PSI to pull the plastic down with. If you're not using the high vac, the plastic just won't pull down well. If you are using the high vac, the high-vac will have to do that basic pulling down that the low vac didn't manage. This will cost you vacuum to suck all that air out, and reduce your final vacuum level by polluting your vacuum tank with that air, and may cost you some fine detail.
From this analysis, it seems to me that the cracking pressure of the valve may matter significantly---you want it to be a modest fraction of the PSI the low vac can pull, but not too big a fraction. And even if it's adjusted optimally, there's a basic tradeoff; you're always going to lose a bit of low-vac performance by using a check valve to shut it off, and a bit of high vac performance by having the valve take time to shut, and waste some vacuum. (And if you're not watching a vacuum gauge closely, you will not know what's going on.)
That makes me wonder some things:
1. How well does the check valve scheme work, even if you have the right valve, with the right cracking pressure? The ideal valve would instantly open the high-vac and close off the low-vac line at just the right moment.
The check valve may be an 80 percent solution, giving you most of the pull-down performance of your low vac and most of the final vacuum of your high-vac, but I don't know that for sure. I'm guessing it usually works pretty well, if only because Doug Walsh seems to be a smart and careful designer.
2. How hard is it to adjust the tension on the rubber band (or the compression of a spring) and get it close enough to right?
A system using a weight seems like it would be better---easier to adjust to give the PSI you want by putting the right amount of weight on the flapper, given the area of the valve hole. You could easily compute the weight necessary to give you the desired cracking pressure, and you'd know it wouldn't change due to rubber bands or springs weakening.
Unfortunately, I don't think there's actually any one "right" cracking pressure. The "right" cracking pressure depends on your system---how much low vac suction you can afford to lose, and how much high vac volume you can afford to lose.
Worse, I think it may depend on how much leakage you're getting around the platen on a particular pull, and how that's affected by changes in pressure. Unfortunately, there are some subtle issues there that I haven't figured out.
I'm not sure of the implications of most of this, but I think there are three plausible conclusions:
(1) It may be a bad idea to try to build a two-stage system without a vacuum gauge to see what it's really doing, and maybe tune it a little; a cheap Noshok gauge will do fine for that.
(2) If you use the check valve trick, but sometimes use the system with only the low vac, you may want to be able to remove, disable or bypass the check valve. Otherwise it will degrade performance in low-vac-only mode somewhat. (You likely want to be able to detach the check valve anyway, to check on the rubber band or whatever, and adjust or replace it, so being able to removing it is the simplest and cheapest thing. It may not be the most convenient thing, because it needs a large connection and you have to make sure it seals well enough for high vacuum on the platen side, every time. It may be worth adding a big bypass valve, but big valves cost real money. Bleah.)
(3) It's worth thinking about other ways to do the switch. If you're opening the high-vac valve manually anyway, you might use a big Y valve, or gang two valves together so that one handle opens one valve and closes the other. That's conceptually simple, but there may be some subtleties to it.
For example, if both valves are partly for too long, the high vac will suck air through the low vac, which is what we're trying to avoid. If they're both closed for too long, that might cause a momentary loss of vacuum, which could and affect the platen-to-plastic seal. Bleah.
(Lately I've been thinking that the platen seal is like a great big check valve. The higher the vacuum, the better it seals... usually, I guess. If you lose vacuum for even a moment, that might be trouble, especially in high-vac mode. The high vacuum system can't cope with leaks very well, and relatively small leaks can cause a big loss of vacuum---which may lead to poorer sealing, worse leakage, and a bigger loss of vacuum. I'm really unsure about that, though.) |
|
Back to top |
|
 |
drcrash Guru

Joined: 04 Sep 2006 Posts: 705 Location: Austin, Texas
|
Posted: Wed Oct 18, 2006 12:00 pm Post subject: success, I think |
|
|
One rough real-world data point...
I did a test pull of actual plastic (acrylic), with the rubber band installed in the (upright) check valve, and (I think) somewhat improved platen sealing.
It seems to work better now. I was too busy fumbling with the valve to see the gauge as I opened the valve, so I don't know how just how far the pressure initially plummeted, but it was around 12 and dropping fairly fast due to platen gasket leakage when I looked up from the valve. (But not dropping as fast as in previous real pulls.)
I'd pumped the tank down to 23 inches, so apparently I managed to use at least half my vacuum (because the check valve worked better), and for somewhat longer (because it leaked away around the platen somewhat less quickly after the check valve shut).
It seems to make a clear difference, although it's possible I didn't control other variables as well as I think. I got visibly better detail than I've gotten with this acrylic before, down to about half the previous radius. (And some thinning and webbing where previously it didn't pull down to the mold in an undercut... but that's more evidence that the 2 stage is actually working, and I can fix it by angling the buck a little.)
It could be a lot better, of course, if I wasn't wasting almost half my vacuum right off and leaking the rest away too fast, but I'm getting more than 2x the force on the plastic than I'd gotten before, for a few seconds, and just those few seconds apparently make a nice difference.
(This is on the little 12" x 18" Sunbeam over-and-under, where the drag from the check valve doesn't matter much---there's just not all that much air for the low vac to suck out, on such a small platen---I don't know if it will work on the bigger platen, with the same plumbing, but I'm hoping it will work at least as well if I do a better job with the platen and maybe some cracking presure tuning.)
Paul |
|
Back to top |
|
 |
drcrash Guru

Joined: 04 Sep 2006 Posts: 705 Location: Austin, Texas
|
Posted: Tue Oct 24, 2006 3:59 am Post subject: valves |
|
|
I was just poking around on build-stuff.com, and looking at this page about the Hobby-Vac
http://build-stuff.com/1001plans_hobby_vac.htm
if you scroll down to the "what's in the plans?" section and look at the little pictures, it appears that Hobby-Vac uses a regular white PVC plumbing check valve, <i>not</i> a sump pump check valve.
A regular white PVC check valve is a spring-loaded piston check valve, not an unsprung swing check valve like a (cheaper) sump pump check valve. (A swing check valve has a flapper on a hinge.)
This makes me think that maybe Walsh chose the sump pump swing check valve for his book because he was aiming really low. It's the cheapest big valve you can buy. A regular spring-loaded PVC check valve has a higher cracking pressure and does not require the ugly rubber band hack.
I'd looked at white PVC check valves, and played with them, and was afraid that maybe the cracking pressure was too high, and it would restrict the flow in low vac mode too much. (Or maybe not open at all.)
I was likely wrong about that.
If I had it to do over again, I'd go with my original instincts and try a white PVC check valve first.
I've come up with what I think is a better plumbing scheme for 2-stage, which doesn't rely on a check valve at all for basic switching between high and low vac, so there isn't a problem with a check valve closing too slowly. You just turn a handle that closes off the low vac line and opens the high vac line. It does require a big "two way" valve, which closes off one part before opening another, and I haven't found a large, cheap two-way valve.
"Three way" (mixing) valves are more common and therefore cheaper. They open one port while closing the other, so that the middle position is a mix. What you want for this application is to close off the low vac line before opening the high vac line at all, to avoid having the high-vac line suck air through the low vac line. The cost of those less common valves is likely why Walsh uses a check valve scheme---it's not really the right valve, but it's dirt cheap. |
|
Back to top |
|
 |
plasticfan Novice
Joined: 10 Aug 2006 Posts: 43
|
Posted: Wed Oct 25, 2006 2:13 am Post subject: |
|
|
forgive my naivty.. what is the point of a two stage? I mean, what exactly are the two stages? Am I missing the obvious?  |
|
Back to top |
|
 |
drcrash Guru

Joined: 04 Sep 2006 Posts: 705 Location: Austin, Texas
|
Posted: Wed Oct 25, 2006 5:11 am Post subject: |
|
|
A "two-stage" system uses two vacuum sources to suck the plastic down.
Typically, that's something like a shop vac and something like a vacuum pump plus a "surge" tank.
There's a torque-like issue here.
A shop vac can pull a lot of air out from under the plastic, but it can't pull the plastic down hard. It's like a lever with a lot of throw and not much torque---it can move a lot (of air) if there's not much resistance. As soon as there's much resistance, it stops. (Tops out at 4 to 6 inches of mercury, or 2 or 3 PSI, but can move maybe 100 cubic feet per minute if there's very little resistance.)
A typical not-terribly-expensive vacuum pump can't pull a lot of air in a hurry, but the air it does pull, it can pull hard. (It tops out at something like 24 or 28 inches of mercury, or 12 to 14 PSI, but can pull less than a cubic foot per minute at those pressures.) It's like a lever with very little throw but lots of torque.
When you first start pulling the plastic down, there's typically not much resistance. A shop vac can usually get most of the air out just fine. But once it's done all of the easy stretching and bending of the plastic, it stops.
That's when you want to open the valve to a vacuum tank that you've emptied with a vacuum pump. There's not much air left, but it's hard to pull out. The harder vacuum can pull bend the plastic down into small concavities or tightly around small convexities. There's not much leverage across those small things, so you need a lot of PSIs to bend the plastic. (Especially if it's thick plastic.)
If you don't pull most of the air out with a high volume / low vacuum pump like a shop vac, you waste vacuum. All that air that a shop vac could have pulled out gets into your vacuum tank and weakens the vacuum. That means that when it comes time to form the plastic around fine detail, you don't get as much force on the plastic.
In principle, you should be able to use a much smaller vacuum tank with a two-stage system than with a one-stage high vacuum system, and a much smaller vacuum pump to evacuate it in a reasonable amount of time between pulls.
In practice, your tank needs to be large enough to deal with leakage around the platen edge seal. That's usually where most of your vacuum goes; air keeps leaking in and being sucked into your tank, and your vacuum weakens. It needs to hold a pretty strong vacuum for a few seconds, and preferably 20 seconds or so.
This is much less of a problem with a shop vac, because it just keeps pumping and can keep up with a moderate amount of leakage.
Another kind of two stage system is one with two high vacuum tanks. Rather than having one big tank, you can have two smaller ones. The first one sucks the plastic down, sucking most of the air into it and losing a lot of vacuum force. Then you close off that tank and open the fresh one, which can pull the remaining air much harder. |
|
Back to top |
|
 |
jegner Site Admin

Joined: 30 May 2003 Posts: 2144 Location: Texas, USA
|
Posted: Wed Oct 25, 2006 6:24 am Post subject: |
|
|
Good info, Dr. Crash!
If you are not happy with the results with a shop vac alone, and you want to get a boots, say from a small tank or a slow vac pump, you can rig a check valve, pull 80% with your shop vac, and then at the last minute, boot the vacuum with a second vacuum source. Hence, 2-stage. |
|
Back to top |
|
 |
plasticfan Novice
Joined: 10 Aug 2006 Posts: 43
|
Posted: Wed Oct 25, 2006 11:13 am Post subject: |
|
|
interesting thanks.
So why not just use a super powerful pump in the first place? And, doesnt heat of the plastic affect, to a large extent, the ease of which its pulled into detailed areas? I understand the torque analogy, thought it would seem more like one pump is merely exhausted and another need take over hence---do you need a second tank on account of a second pump? In other words is the need for a second stage due to the lack of a larger tank? ...along the lines that a second pump is needed since tank one is kaput. |
|
Back to top |
|
 |
|
|
You cannot post new topics in this forum You cannot reply to topics in this forum You cannot edit your posts in this forum You cannot delete your posts in this forum You cannot vote in polls in this forum
|
Powered by phpBB © 2001, 2005 phpBB Group
|