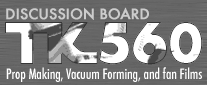 |
www.TK560.com Vacuum Forming, Movie Prop, Sci-fi and GIjOE Forum
|
|


|
View previous topic :: View next topic |
Author |
Message |
drcrash Guru

Joined: 04 Sep 2006 Posts: 705 Location: Austin, Texas
|
|
Back to top |
|
 |
drcrash Guru

Joined: 04 Sep 2006 Posts: 705 Location: Austin, Texas
|
Posted: Sat May 05, 2007 8:47 am Post subject: |
|
|
Since the hobbymolding site has been overwhelmed with porn spam and I'm afraid it may go away entirely, I thought I'd just repost the whole thing here:
PLATEN DESIGN AND CONSTRUCTION
There are two basic issues in platen design. One is how to how to seal the edge of the sheet of plastic to the platen, so that sucking the air out from around the buck doesn't just pull in air from the outside.
The other is how to distribute the vacuum, i.e., provide paths from around the buck to the pump and/or tank.
EDGE SEALING
There are two common systems for sealing the edge of the plastic to the platen. One is to use a gasket around the perimeter of the platen. (Or just around some smaller area when using smaller sheets.) The bottom of the plastic-holding frame is lowered onto this gasket to make a seal. Less obviously, there is also a seal between the plastic itself and the top of the frame---the frame is sandwiched between the plastic and the gasket, so it should be continuous and smooth on both the top and bottom.
Directly Sealing the Plastic to the Platen Edge
Another system, which is generally considered to work better, is to seal the plastic directly to the edge of a raised platen. The platen is sized to fit inside the plastic-holding frame, with a quarter or half inch to spare all around. The hot plastic is lowered over the buck and platen, with the frame going around the platen, so that the edge of the plastic is a quarter or half inch lower than than the edge of the platen. This stretches the plastic over the edge of the platen. Since it is hot and rubbery, it immediately conforms to the shape of the platen edge and makes a seal. (It also cools immediately, but has taken on the right shape and vacuum generally keeps it fairly tightly sealed.)
The edge of the raised platen is smooth and slightly rounded (with a radius of about an eighth of an inch or so.) This makes it easier for the plastic to conform to the shape and make a seal.
For this system to work well, the plastic must be hot and rubbery all the way to the corners of the platen. It will not work as well if the plastic is not evenly heated.
With either kind of sealing system, a bad seal at the edge may not be obvious, and the system may work passably well anyway. Near the edge, the plastic may simply suck down flat to the platen and more or less seal, so that the former still "works."
In some cases the results will be fine, especially with small plastic and no high vacuum system, because a vacuum cleaner can pump enough air to keep up with a moderate amount of leakage. Other times, especially with a high-vacuum system, the results may just be poorer without the user noticing that there's a bad seal, or knowing that fixing it would give better results.
(An inexpensive vacuum gauge is very handy for determining whether the system is really sealing well.)
I'll come back to the subject of edge-sealing after discussing basic platen designs.
(If you're not sure whether you want an edge-sealing platen, but want one with a bunch of holes, you can make the platen "too big" and use a gasket at first. Then if you decide you want to convert it, you can cut away a bit more than an inch around the edge, so that your platen will fit inside the frame, rather than under it. Just be sure you don't have any internal cavities or holes within a half-inch of what you may cut away later.)
WHY AND HOW TO MAKE A LOW-VOLUME PLATEN
When using a high vacuum system, the internal volume of your platen matters. Whatever air is inside the platen itself has to be evacuated to get a good level of vacuum under the plastic. If you use a tank, that air will go into your tank and reduce the vacuum level there, weakening the pull. If you don't, and rely on brute force vacuum pumping, it will take substantially longer to pull the air out from under the plastic.
This doesn't generally matter much if you're just using a vacuum cleaner, because vacuum cleaners suck a lot of air in a hurry and then just top out. (They don't spend a lot of time rarefying the remaining air.) Even if your platen is a fairly big box with a cubic foot of air in it, that likely won't matter.
But if you might ever use a high vacuum system of any sort, the volume is likely to matter---especially if you go cheap and use a hand pump or a thrift-store food sealer you snag for a few bucks, or an inexpensive commercial "vacuum pump" you score cheap on eBay. Making a low-volume platen can be easy, so you should consider it, and read on.
When making a platen, you want to minimize the airspace inside the box, while still allowing air to flow freely from the hole(s) on top to your vacuum system.
One Big Hole May Be Perfect
One way to avoid having a lot of useles air inside your platen is to make your platen solid---just a board with a hole in the center to suck air through. This will not "distribute the vacuum" by itself, but for many people's purposes, it's just fine and works as well as anything could. If you are only making one object at a time, with one buck sitting over the center of the board, it works great.
You just need to put the mold up on spacers (coins or something) so that
air can go under the buck and get to the hole. You should probably do that anyway, so having more than one hole in your board may not be any better at all.
If sometimes you need to make multiple small objects with one pull, using several bucks arrayed across the platen, there are other ways to distribute
the vacuum across the board. You just have to make sure that the plastic doesn't pull down flat between the bucks, or across the hole; you can do that by putting thin objects in the way, under and between the bucks and across the big hole.
So unless you understand these things and know that you have a real need for a fancier platen with lots of holes, don't make one. If you go with a platen-edge sealing system, your time and effort may be better spent making several simple one-hole platens of different sizes.
Having said that, I'll tell you how to make a many-holed platen if you decide you want one.
Don't Make a Big Box
First I'll tell you how NOT to make a platen if you may want to use a high vacuum system.
A lot of people make platens that are boxes several inches tall, sealed on the top and sides, with a board with many holes across the top. The vacuum cleaner just connects to a hole or short pipe through one side of the box.
The box itself serves as a "plenum" (flow-distributing chamber) to distribute the vacuum to the holes. Sucking air out of the box sucks air in through the holes.
Code: |
+----- --- --- --- --- --- --- --- --- --- --- --- -----+
| |
| | vacuum
| Plenum ------ cleaner
| ______ connects
| | here
+-------------------------------------------------------+
DON'T DO THIS
|
A similar but better way is to put the bottom of the box near the top, making a gap of about a half inch, and connect the vacuum to a hole in that raised "bottom."
Code: |
+----- --- --- --- --- --- --- --- --- --- --- --- -----+
|--------------------------+ +--------------------------|
| vacuum | | |
| connects | +-----------------------------
| here \_______________________________
| |
+-------------------------------------------------------+
THIS IS BETTER
|
Now the "plenum" contains much less excess air, and still works fine. The box is mostly a supporting frame for the two boards on top, and. You don't really need the box, if you put a spacer strip between the upper and lower boards, around the perimeter, and support the platen in some other way. (That' what I like to do---I have several platens, and I don't want each one to have its own bulky box.)
Code: |
+----- --- --- --- --- --- --- --- --- --- --- --- -----+
+--------------------------+ +--------------------------+
vacuum | |
connects | +-----------------------------
here \_______________________________
|
Here's a close-up of an edge this "sandwich" construction:
Code: |
+---------+ +--------+ +--------+ +--------+ +------
| | | | | | | | |
+---------+ +--------+ +--------+ +--------+ +--------
| spacer | plenum
+---------+-------------------------------------------------
|
+-------------------------------------------------------------
|
Now you can see that we still have a "plenum," it's just much shallower and holds a lot less useless air.
(To keep the upper board and the lower board from being pulled together by the vacuum, we need to have some more spacers spaced out across the board, every few inches. Those can be small and should be positioned so that they don't interfere with the airflow toward the big hole; that's not hard.)
A half inch gap is still a lot, though. For a 2-foot-square platen, it comes out to a sixth of cubic foot, or about a gallon of useless air inside the platen. If you're relying on a vacuum pump with no tank, and your pump can pump a few cubic feet a minute, it will take several crucial seconds to pump that air out. If you're using a tank, but it's not very big, it will pollute your tank significantly and reduce the available vacuum.
Over most of the board, the gap in the sandwich doesn't have to be very big at all---an eighth of an inch is fine, and allows plenty of airflow from the individual holes in the top toward the big hole in the bottom, where the air is being sucked out.
1/8" is not enough near the big hole, though. That's where all the air converges as it's sucked out. If your hole is one inch in diameter, for example, it means that all the air has to squeeze through a 1/8" tall space around the perimeter of 1" hole. That perimeter is about three inches around, so the total "cross sectional area" that the air is being sucked through is only about three eighths of a square inch. That's about the same size as a half-inch pipe, just stretched out skinny and wrapped around in a circle.
We can use a 1/8" gap without this restrictive "bottleneck" if we provide some air channels outward from the big hole toward the edge of the board.
We can just cut some grooves in the top of the bottom board and/or the bottom of the top board, radiating outward from the big hole, like this:
Code: |
+---------------------------------------------+
| |
| |
| |
| \ / |
| \ | / |
| \ | / |
| \ -+- / |
| -------------+ +--------- |
| / +-+ \ |
| / | | \ |
| / | | \ |
| / | | \ |
| / | | \ |
| / | | \ |
| / | | \ |
| / | | \ |
| / | | \ |
| / | | \ |
| / | |
| / | |
| | |
| |
+---------------------------------------------+
|
For example, we can cut eight radiating grooves about 1/4 deep and 1/4 wide, and that will increase our cross-sectional area around the hole by a half of a square inch. (1/4 x 1/4 gives a 1/16 square inch cross section, so eight of them is 1/16 x 8 = 1/2 square inch.)
If we do this on both the top of the bottom board and the bottom of the top board, we can make our platen "breathe" even better. For example, we might cut the channels outward a third of the way to the edges on one surface, and two thirds of the way on the other.
You probably noticed that the big hole is off-center in the picture above. Many people think that the hole should be right in the middle, but it doesn't matter---as long as the airflow toward the big hole is not restricted, the pressure will equalize all over the board.
I like having the holes in my platens off-center by a few inches; that usually makes it easier to arrange stuff (pumps, tanks, plumbing) under the platen. (Having the connection pipes/hoses stick down in the very middle is awkward, because you can't put anything right under the platen that isn't less than half the width of the platen.) You can put the hole near an edge, or in a corner if you want. Just make sure that there's enough cross-sectional area of channels across the middle toward the far side of the board.
The sizes and numbers of radiating channels given above should be plenty for platens up to about 2 x 2 feet, if you put grooves in both the top and the bottom boards. Just doing one or (top or bottom) be plenty for smaller boards up to about 16 x 20. You can use twice as many grooves half as big if you want, but it doesn't really matter---whatever is easy for you to cut.
If you don't have a router, an easier way to get the same effect is to add a layer to the sandwich, using a piece of thin plywood or MDF, and cut the radiating channels out of it with a portable saw.
If You Want to Make a VERY Low-volume Platen...
To make a VERY low-volume platen, you can eliminate the airspace between the top and bottom layers of the sandwich entirely, and just make grooves that all the little airholes in the top can feed into.
One way to do that is to route parallel grooves about 1/8" x 1/8" into the top board, lengthwise along the long axis (if there is one), like this:
Code: |
+----------------------------------------------+
| |
| |
| | | | | | | | | |
| | | | | | | | | |
| | | | | | | | | |
| | | | | | | | | |
| | | | | | | | | |
| | | | | | | | | |
| | | | | | | | | |
| | | | | | | | | |
| | | | | | | | | |
| | | | | | | | | |
| | | | | | | | | |
| | | | | | | | | |
| | | | | | | | | |
| | | | | | | | | |
| | | | | | | | | |
| | | | | | | | | |
| | | | | | | | | |
| | | | | | | | | |
| | | | | | | | | |
| | | | | | | | | |
| | | | | | | | | |
| | | | | | | | | |
| | | | | | | | | |
| |
| |
+----------------------------------------------+
|
Then you can drill holes down into those lengthwise channels to make a grid of holes. That allows air from any hole to travel lengthwise along the board until it hits one of the larger radial grooves, and head straight for the big hole.
(If you do this, at least some of the radial grooves should extend all the way to the outer lengthwise groove, not stop short of that. Or you could rout a few crosswise grooves, too.)
If you don't have a router, you can do this with a layer of thin slats, maybe made out of paint stirrers or "craft paddles." (I have some craft paddles from Wal-Mart; they're like paint stirrers but smaller. If you want 1" spaced holes, they're conveniently 7/8" wide, so spacing them an inch apart leaves 1/8" channels in between.)
With the lengthwise grooves and the radial grooves, all you have to do is glue or caulk the two boards together, with the grooved sides facing.
A Note on Gluing/Caulking:
When you put together a sandwich-construction platen, realize that the only place you need to seal the layers together is around the perimeter. Glue elsewhere is just there to hold the thing together, and you don't need a lot, because there are no major forces on the pieces, except the compressive force of the vacuum, which just squeezes it together.
You may want to use silicone caulk around the, rather than "glue". It's really not a very good glue, but it's a fine sealant and for this you don't need really strong glue.
When applying glue to an internal spacer or slat, just use a bead of wood glue (or silicone caulk) down the center. Smearing a lot of glue all over it won't make it any better, and may create a void, with air sealed in.
Clamp the sandwich together while the glue sets. The easiest way to do that is to put in on a very flat, very strong surface, and put something flat across the top of it, and weight it down.
If your sandwich construction leaks, that's easy to fix. A smear of epoxy around the outside should do it. (Vacuum tends to suck sealants into holes, rather than blowing them off.)
Before gluing the whole sandwich together, be sure you know how you're going to connect your vacuum. It may be easiest to drill the holes for that first. Be sure they won't create leaks; you may want to reorient them to avoid the air channels inside the board, etc.
A Note on Materials:
A good material for platens is MDF (Medium Density Fiberboard). It's flatter and smoother than most wood, reasonably strong, durable, and easy to work. And it's cheap. For large platens I'd recommend 2 layers of 3/4" MDF; for small ones 1/2" is fine.
MAKING AN EDGE FOR EDGE-SEALING
For a system without a gasket, where the plastic seals directly to the edge of the platen, the top edge should be rounded about 1/8".
The corners should probably be rounded in the horizontal plane, as well, by a bit more than that, maybe an inch. There are two reasons for this. One is that when forming very thin plastics, the plastic may rip at the corner and you'll lose vacuum.
The other is that even with a good oven, the plastic is often not as hot at the edges, and especially at the very corners. One reason is that the frames may shadow some of the infrared radiated by heating elements, so that most of the plastic is being heated from all around, but at the edges it's mostly being heated from one side. This problem is worse in the corners, because there are three quadrants from which the plastic may not be receiving direct IR, and only one where it is.
(There's some subtlety here, and the problem isn't as bad as it seems. Metal frames actually reflect most of the infrared that hits them, so they reflect some IR that would otherwise miss the plastic back onto the plastic at the edges. Light-colored wood does the same thing to some degree.)
Another reason that edges and corners are often less hot is that the clamping frames conduct away heat, especially if they're metal. (Preheating metal frames is a good idea if this is a problem.) Very near the edges, the plastic may lose significant heat to the frames. At the corners, the plastic is losing heat in two directions.
Because of these things, it's probably good for the platen "corners" to be rounded by a half-inch or so in the horizontal plane. (Not in a vertical plane; if the upper edge going around the platen is too rounded, the plastic may fail to "grip" and form to it---it may just slide or pop up.)
The usual material for the surface of the platen is thin aluminum, glued and smoothed over the top of the top board, and with the edges beaten down to conform to the rounded edge with a rubber mallet. (Do that slowly and carefully, especially in the corners.)
Naturally, if you're going to do this, you should do it before drilling the platen holes, or you'll have to drill them again. (And you should be sure you have good alignment marks, if you're making a very low volume platen that has no air gap---when you drill your holes, they must hit the small grooves in the upper board.) _________________ Paul (a.k.a. Dr. Crash)
Tired of buying cheap plastic crap? Now you can make your own! www.VacuumFormerPlans.com
Last edited by drcrash on Sat May 05, 2007 3:39 pm; edited 1 time in total |
|
Back to top |
|
 |
faithblinded Newbie
Joined: 28 Apr 2007 Posts: 14 Location: Cleveland, Ohio
|
Posted: Sat May 05, 2007 2:01 pm Post subject: |
|
|
Great write up Paul!
Definitely seems like a lost cause posting things there. Someone needs to archive the good info that is still there, so when that forum dies, it can be put up here. |
|
Back to top |
|
 |
drcrash Guru

Joined: 04 Sep 2006 Posts: 705 Location: Austin, Texas
|
Posted: Sun May 13, 2007 2:59 pm Post subject: edge-sealing platen edges |
|
|
By the way, another option for making an edge-sealing (no gasket) platen is to just round the edge of the platen a little and seal it with resin, making sure it's really smooth. You don't really need to cover it with aluminum; as long as the edge is smooth and rounded, the rubbery plastic will seal to it.
I suggested this to a guy over on rcgroups.com and he tried it, and it seems to work like a charm. (He's producing ABS airplane bodies especially for aerial photography setups.)
I just noticed that Walsh mentions this in his book, too, but none of the pictures show it. He suggests using polyester resin, which he thinks is more heat tolerant than epoxy. I'm not sure that's right. Professional vacuum formers use epoxy molds all the time. (Some epoxies are more heat tolerant than others, though.)
Could somebody with experience with aluminum platen skins elaborate on the technique for getting it bent down around the corners without wrinkling too much? (I'd be inclined to cut darts into it, and smooth over the seams with JB weld. I'm lazy.)
Is there any reason I couldn't just epoxy coat an MDF platen, and go back and layer aluminum on it later if it started to wear out? (I'm thinking it probably would do anything I want it to without the aluminum skin, but I might have to do some maintenance on the edges occasionally, sanding and recoating them to make them smooth again.) _________________ Paul (a.k.a. Dr. Crash)
Tired of buying cheap plastic crap? Now you can make your own! www.VacuumFormerPlans.com |
|
Back to top |
|
 |
|
|
You cannot post new topics in this forum You cannot reply to topics in this forum You cannot edit your posts in this forum You cannot delete your posts in this forum You cannot vote in polls in this forum
|
Powered by phpBB © 2001, 2005 phpBB Group
|