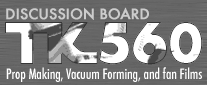 |
www.TK560.com Vacuum Forming, Movie Prop, Sci-fi and GIjOE Forum
|
|


|
View previous topic :: View next topic |
Author |
Message |
drcrash Guru

Joined: 04 Sep 2006 Posts: 705 Location: Austin, Texas
|
Posted: Sat Sep 22, 2007 10:10 am Post subject: |
|
|
jegner wrote: | A well made fiberflass mold will be strong enough for even a 29.9 in/hg vac forming needs. You of course needs to make the molds 'husky' like they way boats and car body panels are made but thats about 4-6 layers of FG and resin. Nice thing, FG molds are light weight and easy to repair!
|
The downside of a thick shell hollow mold is that it holds a bunch of air that you have to pull out. For a high-vacuum setup, that means you need a bigger tank.
I think 2 or 3 layers of FG ought to be fine if you fill it with something cheap---almost anything---to take up the volume and reduce the vacuum requirements. (Modeling clay would do it, and be easy, but even really cheap modeling clay costs $1 a pound, and vent holes might close up.)
Even light foams like pink or blue insulation foam have a compressive strength of an atmosphere or so, and should do it. Very light foams may eventually come apart under vacuum, though.
Here's another interesting moldmaking video from Freeman:
http://youtube.com/watch?v=-2Ml49s5Fx8
The mold they're making is kinda complicated because it's a multi-piece mold, but the basic idea is simple---lay up a very few layers of fiberglass, then a thick layer of cheap but modestly strong filler stuff, then a little more fiberglass. Essentially you're making foam-core fiberglass.
The middle stuff, which doesn't have to be nearly as strong, is something like tiny styrofoam beads mixed with resin. That's strong enough to stabilize the inner and outer fiberglass layers so that you get an I-beam effect.
(It's neat how they make a relatively uniform sheet of that stuff, by just rolling it with a rolling pin up on a couple of sticks. Then they cut it into pieces and fit it to the inside surface of the outer FG.)
I'm trying to think of some easy similar techniques that'd be especially appropriate for making vacuum forming bucks.
One thing we've done recently for some medium-sized Ultracal molds (more faces) is to cast in a blob of modeling clay in the middle.
The modeling clay serves two purposes. One is to hold greased skewers for casting in some vent holes. You stick the skewers through the clay blob where you need them, and pack the clay to hold them while you pour the plaster. (You need to hold the clay down, or it will float up in the plaster.) You slide the skewers out once the plaster is basically set, but before it's really hard.
After it's set, you can scrape the clay out. That leaves a hollow in the middle of the mold, and if you need more vent holes, you can just drill them into that hollow, rather than having to drill all the way through the buck.
That has a couple of advantages. One is that you generally don't have to drill as far. Another is that you don't have to drill very accurately.
I've tried drilling biggish holes from the back, and then drilling little holes from the front that meet those big holes. Without a good jig to align the drill paths accurately, so that they actually connect, it's hard to get them to meet, and I end up enlarging the little hole when I try a new angle to get the holes to meet. Ooops.
With the blob-of-clay trick, you have a bigger target, and you can concentrate on not enlarging the little hole from the front, rather than getting it to hit the relatively small channel you drilled from the back.
(BTW, if anybody tries this with resin, watch out for inhibition. Regular cheap modeling clay inhibits some resins---not just silicones, but also at least some urethanes.) _________________ Paul (a.k.a. Dr. Crash)
Tired of buying cheap plastic crap? Now you can make your own! www.VacuumFormerPlans.com |
|
Back to top |
|
 |
jegner Site Admin

Joined: 30 May 2003 Posts: 2144 Location: Texas, USA
|
Posted: Sat Sep 22, 2007 10:40 am Post subject: |
|
|
My thought on a FG forming buck is to make it a shell. If the air inside the mold is an issue, a filler like plaster or cement might do the trick.
There is a positive side of the hollow mold. Venting holes. A solid mold might become an issue, but a shell mold would allow a lot better draw through venting holes.
Jim |
|
Back to top |
|
 |
drcrash Guru

Joined: 04 Sep 2006 Posts: 705 Location: Austin, Texas
|
Posted: Sun Sep 23, 2007 9:44 am Post subject: vent holes, casting a space-filling plug with a venting gap |
|
|
jegner wrote: | My thought on a FG forming buck is to make it a shell. If the air inside the mold is an issue, a filler like plaster or cement might do the trick.
There is a positive side of the hollow mold. Venting holes. A solid mold might become an issue, but a shell mold would allow a lot better draw through venting holes.
|
One version of this, if you have a sturdy enough shell to support itself under vacuum, is to cast a space-filling plug 1/8" smaller than the inside of the shell, and have a 1/16" gap between them. 1/16" is plenty---you don't need a big space inside the mold for the vent holes to work well.
You could do that by taking the fiberglass mold, lining it with something about 1/16" thick (or maybe 1/8", just for slack), and filling it with cheap laster and maybe some kind of even cheaper rubble. Then insert the plug into the mold, maybe attaching it with some spacers to keep them together properly.
That would provide a 1/16" or so slot around the perimeter of the bottom for air to get out... way more than enough to service any number of vent holes.
That's pretty much the same trick as the "surface casting" technique in the Freeman video, only you don't actually cast anything in the gap---just leave the gap as an air space.
BTW, if you're fiberglassing anyway, it's pretty easy to put in strengthening ribs to hold the overall shape, so that it doesn't have to be very thick to be plenty strong. (They could get in the way of casting a space-filling plug, but there's probably some clever solution to that problem that's not difficult.) _________________ Paul (a.k.a. Dr. Crash)
Tired of buying cheap plastic crap? Now you can make your own! www.VacuumFormerPlans.com |
|
Back to top |
|
 |
knightshade Expert
Joined: 19 Jun 2005 Posts: 123 Location: Rochester NY
|
Posted: Sun Sep 23, 2007 7:52 pm Post subject: |
|
|
High level, I start with a mold, and I make a pull using styrene.
In many cases my original molds are styrofoam coated in wood glue.
they make one good pull, but get damaged in the demolding process.
Once I have the styrene negative, I use fiberglass resin and matting on the interior. I make it quite thick, in the 1/2 inch to 3/4 inch range - which leaves me with a hollow mold.
(Huge molds like chests, and stuff might need to be thicker - or have supports... I haven't gotten that far yet...)
Your right - it is highly exothermic. Once it is "set", I strip off the styrene.
Frequently it comes off in pieces.
I then let it sit a day or so to fully cure, and then sand down the surfaces
with a fairly course paper.
If I have any surface defects that I see in the pull,
I can mix some resin and do patch work and then sand it down again.
As the molds are hollow, I also drill a number of pilot holes to help direct air flow.
It does take me a while to get the molds to the stage that I want them,
but once there - they've worked great. I've even had a mold dropped onto the floor with no damage.
Quote: |
The downside of a thick shell hollow mold is that it holds a bunch of air that you have to pull out. For a high-vacuum setup, that means you need a bigger tank.
|
Maybe that is part of why I needed to upgrade to 70gallons to hold my vacuum  |
|
Back to top |
|
 |
TeeCee Newbie
Joined: 15 Jun 2007 Posts: 10
|
Posted: Mon Sep 24, 2007 3:20 am Post subject: |
|
|
I use fibreglass moulds for my forming. Rather than just use resin, though, I mix polyester resin and silica together and then rotocast that into the mould first to create an outer skin. Once it's dried, I follow it with a 2 coat lay-up of 450GSM fibreglass. I've never had to add support to any of my moulds (and some of my moulds are huge) - they've always managed to handle 29".
I keep my moulds hollow so they're lighweight and it also allows me to fix some handles on the inside making it a lot easier to pull from the plastic.
To get past the free air in the moulds, I have a 2 stage set-up. I use a shop vac to pull down the plastic over the mould and evacuate the air from the mould, then once it has pulled the general shape, I shut off the valve to the shop vac and open the valve to the tanks to 'tighten up' and pull the detail.
The amount it requires from the tanks is minimal so I can usually evacuate a 30 Gal tank once and then use it for around 4 or 5 pulls before I need to switch the pump on again to get it back to 28 or 29". |
|
Back to top |
|
 |
drcrash Guru

Joined: 04 Sep 2006 Posts: 705 Location: Austin, Texas
|
Posted: Mon Sep 24, 2007 6:28 am Post subject: |
|
|
TeeCee wrote: |
I keep my moulds hollow so they're lighweight and it also allows me to fix some handles on the inside making it a lot easier to pull from the plastic.
To get past the free air in the moulds, I have a 2 stage set-up. I use a shop vac to pull down the plastic over the mould and evacuate the air from the mould, then once it has pulled the general shape, I shut off the valve to the shop vac and open the valve to the tanks to 'tighten up' and pull the detail.
|
Actually, a shop vac won't pull most of the air out of the molds. Even if you're getting 6 in Hg., that's only about 1/5 of an atmosphere, so the molds hold 4/5 of an atmosphere of air when you turn on the high vacuum. That air will mostly go into your tank.
Quote: |
The amount it requires from the tanks is minimal so I can usually evacuate a 30 Gal tank once and then use it for around 4 or 5 pulls before I need to switch the pump on again to get it back to 28 or 29". |
It sounds like you're getting a much better seal around the edge of the platen than some people here, or you wouldn't be able to get several pulls from a 30-gallon tank.
Interesting. Any pictures of your platen? _________________ Paul (a.k.a. Dr. Crash)
Tired of buying cheap plastic crap? Now you can make your own! www.VacuumFormerPlans.com |
|
Back to top |
|
 |
drcrash Guru

Joined: 04 Sep 2006 Posts: 705 Location: Austin, Texas
|
Posted: Mon Sep 24, 2007 8:31 am Post subject: |
|
|
TeeCee wrote: | I use fibreglass moulds for my forming. Rather than just use resin, though, I mix polyester resin and silica together and then rotocast that into the mould first to create an outer skin. |
I'm guessing that by "silica" you mean Cab-O-Sil type fumed silica thixotropic filler (not fine sand as a structural filler...) ?
How do you do the rotational casting? I've been looking for good, simple plans for a rotational casting thing, but haven't found any. (I keep finding the same picture of a wooden one with huge gears that was done as a gear-cutting demo... not worth the trouble.)
Quote: |
Once it's dried, I follow it with a 2 coat lay-up of 450GSM fibreglass. I've never had to add support to any of my moulds (and some of my moulds are huge) - they've always managed to handle 29".
|
How thick is the first layer, and how thick does it end up being? How big are your molds? (Without internal bracing, the thickness needs to be proportional to the spans, for a given shape.) _________________ Paul (a.k.a. Dr. Crash)
Tired of buying cheap plastic crap? Now you can make your own! www.VacuumFormerPlans.com |
|
Back to top |
|
 |
drcrash Guru

Joined: 04 Sep 2006 Posts: 705 Location: Austin, Texas
|
Posted: Mon Sep 24, 2007 8:42 am Post subject: fiberglassing videos |
|
|
There are some pretty decent fiberglassing how-to videos on YouTube.
Some of them are from GasserGlass; here's their channel:
http://youtube.com/user/GasserGlass
My channel's "subscriptions" page has links to a few channels with molding and casting videos, including some lifecasting and SFX stuff (BITY) as well as general moldmaking (Freeman), fiberglassing (GasserGlass), etc.:
http://youtube.com/profile_subscriptions?user=vacuumformer
Auto body fiberglassers often use fiberglass to make their molds, as well as to make stuff in the molds. That's pretty cheap and works pretty well for auto body panel shapes, because they typically have draft and are very smooth, with no fine detail to make demolding hard. You have to be very good about mold sealing and releasing, though. (Lots of waxing, plus PVA) _________________ Paul (a.k.a. Dr. Crash)
Tired of buying cheap plastic crap? Now you can make your own! www.VacuumFormerPlans.com |
|
Back to top |
|
 |
drcrash Guru

Joined: 04 Sep 2006 Posts: 705 Location: Austin, Texas
|
Posted: Mon Sep 24, 2007 9:34 pm Post subject: |
|
|
knightshade wrote: | High level, I start with a mold, and I make a pull using styrene.
In many cases my original molds are styrofoam coated in wood glue.
they make one good pull, but get damaged in the demolding process.
|
Wood glue is mostly PVA (polyvinyl acetate) plastic (not to be confused with the PVA that's polyvinyl alcohol mold release for fiberglassing). It has a low melting point, which may be most of your problem.
A lot of RC modelers sculpt in foam and coat it with maybe 3 coats of epoxy finishing resin, and pull a few pulls of thin plastic over that. If they want it more durable, they may use a layer or two of extremely light fiberglass cloth. (There are some very light fiberglass cloths that don't distort the shape much, so there's less sanding to do.)
You might try using epoxy rather than wood glue. You can put epoxy straight on foam, unlike polyester resin. Polyester resin will eat right through XPS or EPS foams like Styrofoam (TM).
Some RC guys sculpt the basic shape pretty close with foam, then coat the foam with epoxy (with or without a little glass) then put a thin layer of bondo over that and sand it to the final shape.
Quote: |
Once I have the styrene negative, I use fiberglass resin and matting on the interior. I make it quite thick, in the 1/2 inch to 3/4 inch range - which leaves me with a hollow mold.
(Huge molds like chests, and stuff might need to be thicker - or have supports... I haven't gotten that far yet...)
Your right - it is highly exothermic. Once it is "set", I strip off the styrene.
Frequently it comes off in pieces.
|
I'm wondering if the styrene coming apart is due to the heat, or due to the solvents in the polyester resin, or both. A coating of epoxy might make the styrene more durable when you put polyester in it.
Do you see any warpage when you do this? Are you supporting the styrene when you use it as a mold for the FG?
Quote: |
It does take me a while to get the molds to the stage that I want them,
but once there - they've worked great. I've even had a mold dropped onto the floor with no damage.
|
I'm wondering if a gel coat of half bondo and half plain resin might be the way to go... more durable than just bondo, and easier to sand than straight resin. _________________ Paul (a.k.a. Dr. Crash)
Tired of buying cheap plastic crap? Now you can make your own! www.VacuumFormerPlans.com |
|
Back to top |
|
 |
TeeCee Newbie
Joined: 15 Jun 2007 Posts: 10
|
Posted: Tue Sep 25, 2007 2:46 am Post subject: |
|
|
drcrash wrote: |
I'm guessing that by "silica" you mean Cab-O-Sil type fumed silica thixotropic filler (not fine sand as a structural filler...) ?
|
Yes, I use it since it stops exceptional heat when the polyester starts to go off, it creates a smooth outer surface and it's easy to sand. I prefer it to gelcoats since the heat seems to make gelcoat bubble away from the fibreglass after a few pulls.
drcrash wrote: |
How do you do the rotational casting? I've been looking for good, simple plans for a rotational casting thing, but haven't found any. (I keep finding the same picture of a wooden one with huge gears that was done as a gear-cutting demo... not worth the trouble.)
|
Nothing as fancy as a rotocaster I'm afraid, I just pour the mix into my initial plastic pull and then roll it around by hand until it starts to go off (takes about 10 minutes).
drcrash wrote: |
How thick is the first layer, and how thick does it end up being? How big are your molds? (Without internal bracing, the thickness needs to be proportional to the spans, for a given shape.) |
The first silica layer is only a mil or so thick in most places, but I do get get it thicker in other places, especially if I think they'll need sanding later. That's followed by 2 lay-ups. I've never measured the thickness but I always try to make the edges a bit thicker since these seem to suffer the most. Total thickness is probably about 3mm. My largest mould stands about 15" or so high by 19" wide x 20" length.
drcrash wrote: |
It sounds like you're getting a much better seal around the edge of the platen than some people here, or you wouldn't be able to get several pulls from a 30-gallon tank.
Interesting. Any pictures of your platen?
|
The seal on my platen is pretty much airtight. I can place a flat piece of plastic on it and there won't be any loss from the tanks after the initial pull down (there would probably be loss over an hour or so but from short periods there doesn't seem to be any loss of vacuum from the tanks). Combined with the shop vac, I can pull ABS over a mould using the vac and then it takes around 1" HG from the tanks to tighten up to the details. As soon as I hit around 25" I switch the pump on again.
My platen is nothing special - I copied Jim's platen but placed a strip of rubber window sealant around the very edge of it. I thought the heat of the plastic may affect the rubber but it doesn't seem to, the only thing that does is my dragging the freshly pulled plastic off - I really should lift it off rather than drag it. I'll find my camera and take a pic of it. |
|
Back to top |
|
 |
knightshade Expert
Joined: 19 Jun 2005 Posts: 123 Location: Rochester NY
|
Posted: Tue Sep 25, 2007 4:34 am Post subject: |
|
|
[quote="drcrash"] knightshade wrote: |
Any recommendations on an epoxy to try?
|
Not really, but I might have more experience soon.
Quote: |
Up until now, I had been attempting to "keep it simple" by using things that I could obtain locally - but it is becoming clear that this may not be the optimal approach
|
I've been putting Enviro-Tex Light brand Pour-On (TM) finish stuff on some platen edges, experimentally, but that may be a bad idea. It's a thin, slow-setting finishing epoxy you can get at Hobby Lobby craft stores and some hardware stores.
One thing to be aware of (thanks to Doug W. for pointing this out) is that epoxies generally soften up around 200 degrees F, even "high temperature" epoxies---even if the epoxy is rated for 400 degrees and that temperature won't damage it, it will get soft and may get mechanically damaged while it's soft. That may not matter much for thin easy plastic, which doesn't keep the epoxy very hot for very long, but might matter more for thick plastics that are especially hot or don't cool down quickly.
I will not be surprised if I end up having to re-do my platen edges.
That also makes me re-think what I said about an outer coat of epoxy for your FG bucks cast in vacuum-formed styrene pulls.
I'm wondering if just waxing and PVA'ing the styrene mold would protect it from the polyester resin solvents... have you been waxing and PVA'ing?
(I've also heard that heavy duty hair spray can be a reasonable substitute for PVA, at least for casting epoxy. It's a water-soluble plastic, too, and easy to spray on. I don't know if it works for polyester.)
The usual thing when casting fiberglass in a hard mold is to seal it with several coats of mold release wax, or fairly pure carnauba car wax. (Not liquid squirt-on car wax; that won't work. It has to be carnauba.) If you're doing thick casting, carnauba may not work, because the heat from the exothermic reaction may liquefy it too much. (I'm not sure about that, but I think some waxes sold specifically for mold sealing are a bit more heat resistant.)
Quote: |
Quote: |
I'm wondering if a gel coat of half bondo and half plain resin might be the way to go... more durable than just bondo, and easier to sand than straight resin. |
Interesting - I've never thought to literally mix the materials.
I did have one mold that I made some extensive modifications to after the fact using bondo - and it seems to hold up well. My success with that had me considering modifying my approach to create the outer shell with a few layers of fiberglass, and then an inner coating of bondo (1/2 inch or so) to give a supporting layer. The fact that bondo is more of a paste would make it much quicker to thicken the sides of the mold. |
I was thinking of bondo + plain resin for a gel coat, to adjust the surface durability/sandability tradeoff. (If your mold is perfect, go for straight resin; otherwise make it sandable.) To thicken the gel coat without making it weaker but more sandable, you're better off using a thixotropic additive. Cabosil "thickens" the goo really well without compromising strength much; a little goes a long way.
(Another reason to use an impression coat is that you can sand the gel coat, not the glass layup, if you don't have to sand too much off. Sanding the actual glass is nasty.)
But I guess when you're talking about thickening the sides of the mold, you're talking about rapidly building up a thick layup by just smearing on a paste, rather than laying up more glass...?
If you want maximum strength, you might consider using Bondo-Glass. It's resin plus short glass fibers, and it's way stronger than Bondo body filler (which is resin plus microballoons). It's not as strong as laid-up cloth or mat, but it's pretty strong.
A layer of regular Bondo filler in between makes sense, I guess, to keep it reasonably light while getting the thickness you need for an I-beam effect. I'm not sure about the cost-effectiveness, though. Bondo filler isn't exactly expensive, per unit volume, but I'm thinking you're mostly paying resin prices for mostly air.
One thing I've considered is a gel coat of some sort (maybe resin + bondo + cabosil), then just smearing on a layer of Bondo-Glass, then smearing on a thick layer of something light (regular bondo?) then just smearing on another layer of Bondo-glass. Or for more a bit more strength, gel coat , a layer or two of cloth or mat, a layer of bondo-glass, a thick layer of cheap filler, another layer of bondo glass, and a final layer or two of cloth or mat.
For the inner thick layer, which is mostly just a spacer between the outer strong thin layers, it'd be good to find something really cheap, stretching the resin as far as possible. With epoxy, it's common to use styrofoam beads and ground foam to make a very thick paste that doesn't waste much resin. Unfortunately, polyester eats styrofoam.
If you're not worried much about weight, all kinds of things can be used as cheap filler for the thick spacer layer---sawdust, sand, gravel, etc. (I think Doug told me he'd used Rice Krispies in a pinch. I'm not sure what resins you can use Rice Krispies with, though.) You want to make an aggregate with particles of various sizes, so that the smaller ones mostly fill in the spaces between the larger ones, rather than wasting resin filling in those gaps. |
|
Back to top |
|
 |
|
|
You cannot post new topics in this forum You cannot reply to topics in this forum You cannot edit your posts in this forum You cannot delete your posts in this forum You cannot vote in polls in this forum
|
Powered by phpBB © 2001, 2005 phpBB Group
|