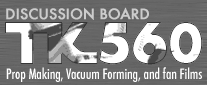 |
www.TK560.com Vacuum Forming, Movie Prop, Sci-fi and GIjOE Forum
|
|


|
View previous topic :: View next topic |
Author |
Message |
Kookas Newbie
Joined: 21 Apr 2006 Posts: 22 Location: Australia
|
Posted: Tue May 02, 2006 1:11 am Post subject: |
|
|
Hi Charlie,
yep you are right, trying it will be the best test. I didn't realise Polycarb had such a low working temp though. Thats good.
I race nitro onroad cars. I used to have an old Hornet off road electric but it was too slow Nice truck though.
I noticed in your picture your clamp. it looks like how I want to do mine. could you possible post a close up of it? how many clamps are on your frame? can I get away with just one clamp or would I need one on each side?
On another note. I had Dad look over the oven last night. I need some heat proof wire and I will probably use roof insulation to better insulate it. I have some heat proof wire in an old oven I dismantled. The interesting part though is that I will probably wire up the thermostat from the oven complete with thermometer so I can control the heat! I was surprised that all I needed was the dial and the thermometer rod. Too simple... More pictures soon!
regards
David K |
|
Back to top |
|
 |
crashmann Guru

Joined: 27 Sep 2005 Posts: 501
|
Posted: Tue May 02, 2006 11:13 pm Post subject: |
|
|
Ahh, my over-engineered clamps
One piece of angle stock 1 1/2" by 3" long
Cut a groove in the middle 1" deep for the 1/4" by 2 1/2" eyebolt
Cut a slot to allow room for the lower clamp
Attach it to the upper frame with 3 screws and 6 nuts
A smaller piece of angle stock 1" x 1" x 1"
Drill two holes, one to attach it to the frame, the other for the eye bolt screw
Attach it to the lower frame with a single screw and two nuts
Mount the eyebolt holder screw with a nut
Add small washers that will fit inside the eyebolt
Mount the eyebolt, followed by a fender washer and a nut
Use a very large fender washer and a wingnut at the top of the eyebolt
Originally, I only had the two clamps at the top of the frame (with the hinges at the bottom). I had a couple of blowouts where the plastic slid out from the sides, so I added one extra clamp to each side. Nothing is more disheartening than seeing the plastic coming down, then losing seal. Super poopy!!!
When mounting the plastic, use an adjustable wrench to tighten down the wingnuts half a turn more than finger tight. Make it too tight, and you strip out the eyebolt (which I have replaced many times!) or you stretch out the loop on the eyebolt (which is evident in the pictures) - That's what happens if you invite your friends over to melt plastic
Fortunately, since adding these clamps, I have not lost another piece of plastic from it slipping out of the frame. I'd like to use some type of quick release / cam clamps, but since the frame is only 1" square tubing, I haven't found any that would fit.
Interesting comment on the thermostat. I guess it just gets wired inline with the hot lead. Then it controls whether or not the circuit is active based on the temperature probe. Nice!
Charlie
TI-386 |
|
Back to top |
|
 |
Kookas Newbie
Joined: 21 Apr 2006 Posts: 22 Location: Australia
|
Posted: Wed May 03, 2006 7:30 am Post subject: |
|
|
Thanks heaps for the photos! they are just what I was looking for. You can never over engineer enough! I put two clamps on the end but will probably do as you did and have side ones as well.
As for the thermostat, it is just wired in instead of the switch. When it is turned right down it is off. I will photograph the dial, print it out and stick it behind the dial so I can see what temp it will be at.
Tonight I took my oven apart and sandwiched the roof insulation between two cement boards. I am hoping this will help keep the heat in and away from the wiring (there I go, over engineering again!)
Last two steps now are to wire the oven up to the mains (planned for Friday) Then source a decent vacuum cleaner. I going to do what Jim suggested and use an ordinary vacuum cleaner for testing. Since my plastic shouldn't be more than 2mm at the most I expect it should be ok. I might post the note from Jim next as I found it quite helpful. Thanks Jim!
So I could be pulling plastic as soon as this weekend! (Getting VERY excited now! )
David K |
|
Back to top |
|
 |
Kookas Newbie
Joined: 21 Apr 2006 Posts: 22 Location: Australia
|
Posted: Wed May 03, 2006 7:34 am Post subject: message from Jim about the vacuum cleaner |
|
|
I thought I would add this in for the benefit of others wondering the same thing about the vacuum source.
Quote: | Kookas wrote:
Hi Jim,
I am thinking now about my vacuum source. I would like to use a shop vac like yours but I am not sure about how successful it will be. Your video seems like it is good enough. What factors are affected by having a shop vac rather than a vacuum pump and tank? From Crashmans video it seems to relate to the size of the moulds.
Also what wattage is your 3hp shop vac? It doesn't look like the wattage relates to the suction power.
Another idea which was mentioned to me was to use a fridge compressor as the vacuum pump. If you can find an old fridge it is basically free! But as I said, I would rather not have to do all the tank and plumbing work.
thanks
David K
|
Quote: | Hello!
Ah, the vacuum. Yes, that is a source of confusion, and it was for me when I started too. I took some advice from Phil [Blaxmyth from New Zealand] and from Paul [ANHTrooper from England] and Stacey [TKBIG from the US] , and the consensus was to test the machine using a shop vac and if satisfied with the results, then stay with it. If not, then upgrade to a high-vac rig.
The shop vacs, and any vacuum cleaner for that matter all pull about the same in/HG. about 4. Does not matter of the HP, AMP, etc. But I do get good results with a 3.5 -6.5 HP vac. Adding more than one in tandem does not increase the performance.
If I were you, I would hook a decent shop vac or vacuum cleaner up, heat some plastic and see what happens. When I started, I was only going to use the shop vac as a test, but so far I have been happy with the results. About the only thing I have to do is add risers, as the bottom of the molds, where they touch the forming platen have a soft edge.
If you are not happy with the results, your vacuum form machine just got much more expensive and complex. You will need a vacuum pump rated at 8+ CFM, a 30 gallon tank, valves and gauges.
Jim |
I'll add this too, I have a really nice Robinsair vacuum pump, but I'm still searching for the 30 gallon tank. If I ever want to try and pull thick ABS I'll need this as the vacuum source, as thick ABS cools much more slowly than HIPS. Something the shop vacs seem to have trouble with.
Last edited by Kookas on Wed May 03, 2006 7:40 am; edited 1 time in total |
|
Back to top |
|
 |
jegner Site Admin

Joined: 30 May 2003 Posts: 2144 Location: Texas, USA
|
Posted: Wed May 03, 2006 7:37 am Post subject: |
|
|
As for the holding grit that lines the insides of the holding frames, I tried the M3 non skid tape. It worked ok for a while the heat cause the adhesive to release. I too that out, and bought a couple of tubes of JB Weld. Mixed it all up, and spread it one all the surfaces that once had the 3M tape. Once it was layered on, I then sprinkled sifted playsand. I let the JB Weld dry over night. Now I have some great grip, and the only time I need to use the side clamps on my rig are when I pull thin material like .060 or smaller.
Jim |
|
Back to top |
|
 |
Kookas Newbie
Joined: 21 Apr 2006 Posts: 22 Location: Australia
|
Posted: Fri May 05, 2006 1:18 am Post subject: Success! |
|
|
Success! well sort of. I just pulled my first sheet of plastic! I used 1mm thick HIPS and pulled it over the mould I showed earlier.
problems: I don't think I got the plastic hot enough (not enough sag) and the vacuum was only an average household vacuum cleaner which didn't produce enough vacuum.
I hooked up the fuse and the thermostat switch from the old oven and it all worked really well, turning off when it reached 200DegF at just the right point.
here are some photos:
the finished product:
the control box:
the first pull:
 |
|
Back to top |
|
 |
Kookas Newbie
Joined: 21 Apr 2006 Posts: 22 Location: Australia
|
Posted: Fri May 05, 2006 5:41 am Post subject: |
|
|
Ok I did another pull. It did come out better because I left it heating for longer (about 18 minutes). But I think I know why its not as good as I want. I now understand what you mean when you say "you need risers" what you mean is that you need risers...
So I'll make some wood blocks to put the mould on and then it should make a perfect top to bottom cast. Also I guess I can't complain after two pulls!
Cheers!
David K |
|
Back to top |
|
 |
crashmann Guru

Joined: 27 Sep 2005 Posts: 501
|
Posted: Fri May 05, 2006 6:50 am Post subject: |
|
|
Congratulations David!
Whoo-hoo, another success story!
Looking at your first pull, I immediately thought you need to add risers, and I'm glad you see that as well. I just put the mold on a piece of 3/4" MDF, trace out the shape with a marker, then cut it a little wider with a jigsaw. If you're skilled enough, set the jigsaw for a 15 degree angle so you taper the sides as you're cutting.
If you just use some scrap wood, and leave too much gap at the bottom of the mold, then you run the risk of the plastic curving in underneath. Then extraction will be accompanied by lots of four letter words Also, you might get a hole if the plastic stretches too thin.
When heating styrene, try setting the oven for 350 degrees. 18 minutes is a long time for the plastic to heat up 1mm or .040 gauge plastic. My oven (without a thermostat and after warming up for 20 minutes) will have the sheet ready to form in about 2 to 3 minutes.
Do you have a shop vac? I've used a 6.5HP shop vac for my table and it has worked great! I picked it up for $100 (US) and have a filter set aside that is ONLY used for vacforming on the table (use a separate filter for vacuuming up gritty bits).
Again, congratulations on your first pulls!
Charlie
TI-386 |
|
Back to top |
|
 |
jegner Site Admin

Joined: 30 May 2003 Posts: 2144 Location: Texas, USA
|
Posted: Fri May 05, 2006 7:49 am Post subject: |
|
|
Yea! You did it!
Learning the craft will come with practice. Let your oven pre-heat for 10 minutes. Then load a sheet of plastic. If you made a lid for the oven, keep that on while the plastic heats. I just set my lid on top after the plastic is in the frames laying on the oven. Set a timer for 1 minute. Check plastic. Reset timer for 1 minute. check plastic, and repeat until the plastic's corners are very soft, and the center has begun to droop down a couple of inches.
Risers are a must if you want detail on the bottom of the molds. If the plastic is hot enough, you can get good platen surface detail, and tight corners, but risers make life easier.
Good job, keep us posted!
Jim |
|
Back to top |
|
 |
ANH trooper Master
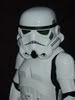
Joined: 20 Oct 2005 Posts: 305 Location: UK
|
Posted: Fri May 05, 2006 1:45 pm Post subject: |
|
|
Congrats on your first pulls mate!
If I can just chirp in here and say that I don't use any kind of risers at all and get good sharp pulls right down to the platen every time.I just have one hole in the middle of the platen and the plastic sucks over the mould and then tries to get 'under' it.I have small slots at the bottom of my moulds that let the air through which I suppose ae kind of risers but are only like 2mm or so.
This method is good for single moulds only really,but you can get creative and make moulds line up like I have to form a few at a time and don't get any webbing issues.If you plan on just making these car bodies I would suggest you try just having your vacuum hose flush with your platen surface,you will be amazed at the great detail you will achieve.
I only use an industrial vacuum cleaner which is very similar to the US 'shop vacs'.I tried using a platen with the perforations like yours and had the same problems.It's like the suction is spread out and weakened over the large area.With one large hole the power is there and when you form it is done instantly with a 'shlop' and voila!
Just my experience,but worth a try if it is not too much hassle to adapt your platen  |
|
Back to top |
|
 |
Kookas Newbie
Joined: 21 Apr 2006 Posts: 22 Location: Australia
|
Posted: Sat May 06, 2006 8:18 am Post subject: |
|
|
I did another 5 pulls and they all came out better than the last. I added a couple of risers by cutting out the shape of the mould from chipboard and using it as a platform. I was then able to cut the body with a nice straight edge.
Its interesting you say that I should go with one hole in the centre ANH Trooper. I was thinking this myself since I'll mainly be doing car bodies, if I could get more central suction I think I would indeed get better results. Fortunately I haven't actually fixed my platen down at all, so it is definitely interchangeable with a central hole version as well. I'll definitely try it.
Well I took my first body out today on the race track. It was actually noticably better than my bought ones! the front of the car had an extra large air dam created by "not enough suction" Unfortunately the HIPS cracked too easily (didn't matter as I had a couple of bodies) so I'll get some polycarbonate (Lexcan) next week and make some out of that. Anyway I now have 4 bodies sitting outside ready for more racing tomorrow. As soon as one breaks, I'll be able to pull out a brand newey. Ordinarily a new body would have cost at least $36-$80 but each body has cost me $4 for materials plus a bit of electricity.
After Charlie mentioned that it should only take a couple of minutes to get the plastic ready, I decided to do a batch. It took 20 minutes for the oven to heat up but subsequent pulls only took 4 minutes from loading to pulling. probably 3 minutes heat time. The thermostat is working really well. I have it at about 350DegF and its clicking on and off at just the right time.
So all in all I proclaim this project a huge success. If I have anything more I'll be sure to post it here. All the best Guys and thanks again for your help. You are champs!!!!
David K
 |
|
Back to top |
|
 |
propsculptor Newbie
Joined: 24 Mar 2006 Posts: 22 Location: Southern California
|
Posted: Sat May 06, 2006 8:03 pm Post subject: |
|
|
Nice job!!
I like the way you did what you called "over-engineered clamps", I think the way you did it looks great, and since it works who cares if it's "over-engineered"! _________________
 |
|
Back to top |
|
 |
Kookas Newbie
Joined: 21 Apr 2006 Posts: 22 Location: Australia
|
Posted: Mon May 15, 2006 3:21 am Post subject: Update |
|
|
Hi,
I have just finished making another 2 bodies. This week I had been trying to pull polycarbonate (lexcan). It broke my mould. It is soo tuff that I couldn't even bring the frame down to create a seal for the vacuum to work. I had 1mm then tried 0.7mm sheets with no luck. The other problem is the temperature. PC needs to be about 300DegC to form and even then you have a small window of about 10DegC to work with. The annoying part was that as soon as I took the lid off the oven, it would cool too much to form This stuff is really frustrating.
Today I finally sourced some PETG plastic @ 1mm (like coke bottle plastic) and it worked unbeleivably well. It has a fairly low forming temperature of about 90DegC. It got to that temperature in a little over a minute. I had to actually do the pull a lot earlier than I thought I would because it nearly sank onto my coils.
The first body I did without risers came out really well. The second body I did with a riser and was even better. It is so easy to work with I probably should have started with it rather than HIPS. (HIPS being cheaper by $10 I am still glad I started with it though)
Another change I have made to my table is I now use a garden blower/vac as the vacuum source. It is about 2000W and pulls a lot more vacuum than my household vac did (who would have thought a household vacuum wasn't up to the task )
I'll post some pics soon. Right now I am painting my car body.
Cheers
David K |
|
Back to top |
|
 |
crashmann Guru

Joined: 27 Sep 2005 Posts: 501
|
Posted: Tue May 16, 2006 6:53 am Post subject: |
|
|
Hmm, that's disappointing news about the polycarbonate. It's a good thing I only bought 6 pieces of the stuff.
I had been digging around the Internet looking at industrial style vacuum forming equipment, and I found a site with videos of their stuff in action. They showed a machine creating 20 oz. bottles for soda or water, and the plastic they were using was called PETG. I was thinking of trying that plastic, so thank you for pioneering the test!
Will the polycarbonate paint stick to the PETG? (You're painting it on the inside, right?)
I might have to rig up the leaf vacuum to see how much it pulls. That's a great alternative to the shop vac!
Charlie
TI-386 |
|
Back to top |
|
 |
Kookas Newbie
Joined: 21 Apr 2006 Posts: 22 Location: Australia
|
Posted: Tue May 16, 2006 9:03 am Post subject: |
|
|
Hi Charlie,
Yep I am painting on the inside. I have only used acrylic paint (hmm maybe it was enamel, though I don't think that would stick) The acrylic is the wrong stuff but the hobby shop wasn't open last night at 10:30 when I was wanting to paint the body . But you still need to use Polycarbonate paint. It is the only one which can bend and stretch with the plastic. The acrylic will chip and peel off.
PETG is definitely what you want. It is pretty tough too. Not as tough as polycarbonate but considering how easy it is to work with definintely worth using.
I remember being told that soda bottles start off as tubes and are pressurised from the inside to form the bottle. If you hold a hair blower near it and slowly melt the plastic, it will actaully return to the tube shape. I tried that once and it seemed to start working...then I got impatient and it burned
Anyway I just finished a second mould and will try it out tomorrow night.
Cheers
David K |
|
Back to top |
|
 |
|
|
You cannot post new topics in this forum You cannot reply to topics in this forum You cannot edit your posts in this forum You cannot delete your posts in this forum You cannot vote in polls in this forum
|
Powered by phpBB © 2001, 2005 phpBB Group
|