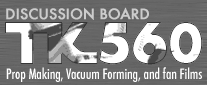 |
www.TK560.com Vacuum Forming, Movie Prop, Sci-fi and GIjOE Forum
|
|


|
View previous topic :: View next topic |
Author |
Message |
Slots_4_Ever
Joined: 13 Dec 2008 Posts: 3 Location: Cleveland,Ohio
|
Posted: Sun Dec 14, 2008 2:10 pm Post subject: Hello from Slots_4_Ever |
|
|
Hello Everyone,
Sure wished that I would have known of this website, way back when I was building my machine.
First of all I must apologize for some of the crappy pictures; bad camera day!
This is my version of the Protoform Vacuum Machine. Blueprint plans provided by Doug Walsh.
While we are not going to see a slot car being vacuum formed today, but a 1/10th scale radio control car body. I'll try to make this interesting and hopes of showing you any one can do it.
Back in the day, year 1999, when everyone thought the world was gonna come to end, computers were gonna crash and burn. My spare time was gathering parts for this contraption. All my friends kept saying "You're building what?" My answer was always a vacuum machine that will heat plastic, suspended in a frame that can be lowered over the mold ,which sits on the platen, connected to this tank, which will have the air sucked out of it, that when you trip this valve, the air is trying to rush back into the tank, through all the little 1/16 inch holes drilled in a 1" grid, covering a useable platen space of 21"x33"! So instead of the plastic being sucked down from underneath, it's actually the outside atmosphere in which we live in pushing the plastic down over the mold. But then, because the plastic is soft and warm, it seals around the edges of the platen and around the mold, resulting in its new hardened shape.
The first of many pictures. Sorry dial-up connections, but stick with me, it's worth it!
This starts off showing the front view of machine. The moveable clamp frame slides up and down in a track of tubes in the center.The handle is just a little over six feet in height, with the roller casters fastened to the bottom for mobility.
The platen close-up showing front panel controls for oven and pump, the lights are to notify me of being on or off.
The tank is a forty gallon electric water heater, stripped down and painted, all the heater elements were removed and drains were either used or capped off. Coleman supplies the air evacuation of tank.
You must use a line capable of withstanding the vacuum or it will collapse.
Dual connection to feed the large platen; notice the 110 volt box for Coleman power.
Power panel box with separate breakers. The box on the left houses the contactors to turn on the heaters, once the other two limits are met.
The 3000w commercial broiler heater elements. The stainless wire mesh was placed beneath the heaters to help try to deflect some of the direct heat onto the plastic as it was being warmed.
The vacuum gauge at full amount, ready to go
The glowing warmth of the heaters, this small amount of time is used in warming up the clamp frame, platen area, and mold.
Which one was it anyway?
Oh, yeah, this one:
The GE .030 Lexan being warmed up
The formed plastic over the hydra-stone mold.
Hot off the mold!
Notice the thick webbing between the two tail sections? This is intended, as the stretching of the plastic over the molds has nowhere to go except stick to itself. This is very thick section of the plastic formed together.
Disclaimer: By no means the modifications that have been done to this machine should be taken lightly.There are 220 volts of power, and open heaters that can burn. Do Not Touch them at any time after they have been on!
So after a lot of work, reading, studying, planning, building, this is a lot of fun! It takes less then a second, blink of an eye, for the plastic to be drawn over the mold. I can only imagine how quick it would be on a smaller scale mold with thinner plastic. While I have never tried to clamp anything thinner than .030 it's flimsy enough trying to hold a 2 foot x 3 foot piece of that!
I have made another table top design that has a flip handle. It's not going so well as of yet. Going back to the drawing board on that!
Here is a picture of the finished trimmed and painted sprint car body pieces.
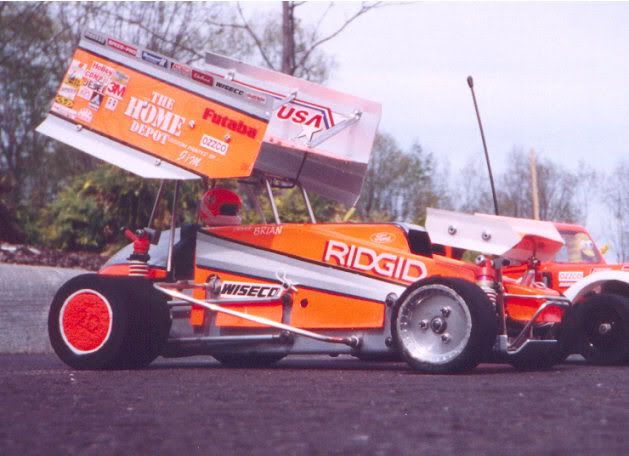 _________________ Brian McPherson |
|
Back to top |
|
 |
jegner Site Admin

Joined: 30 May 2003 Posts: 2144 Location: Texas, USA
|
Posted: Mon Dec 15, 2008 9:06 pm Post subject: |
|
|
Good looking machine! Thanks for the review.
Jim |
|
Back to top |
|
 |
ahillworks Master

Joined: 18 Nov 2007 Posts: 308 Location: Orlando FL
|
Posted: Thu Dec 18, 2008 8:09 pm Post subject: |
|
|
Nice looking setup and like the post. Nice work. |
|
Back to top |
|
 |
Slots_4_Ever
Joined: 13 Dec 2008 Posts: 3 Location: Cleveland,Ohio
|
Posted: Sat Dec 20, 2008 6:17 am Post subject: Smaller machine |
|
|
What do you think?
I'm back at it again building another vacuum machine, this one is a wee bit smaller,
I will use the 5hp shop vac instead of air compressor and tank.
Heat is supplied from the black & decker toaster-oven partially taken apart and re-fabbed special for this project.
Plastic size is 9" X 11" in clamp frame and 6"X 8" useable platen area.
Have yet got to try it out for I'm in short order for plastic, I'm itching to see if this will work or not?
The flip top machine was canceled as I really never liked the design compared to the overhead heating style. This style uses the same lift mechanical clamp frame as my previous larger machine. _________________ Brian McPherson |
|
Back to top |
|
 |
jegner Site Admin

Joined: 30 May 2003 Posts: 2144 Location: Texas, USA
|
Posted: Sat Dec 20, 2008 9:06 am Post subject: |
|
|
Cool!
How thick a sheet of plastic do you plan to use?
Jim |
|
Back to top |
|
 |
Slots_4_Ever
Joined: 13 Dec 2008 Posts: 3 Location: Cleveland,Ohio
|
Posted: Sun Dec 21, 2008 5:23 am Post subject: |
|
|
Hi Jim,
Hoping to do any plastic within .015 and .030 in thickness. I've got a message out to a friend that I believes has some .030 We'll have to wait and see how that goes...busy time of the year. _________________ Brian McPherson |
|
Back to top |
|
 |
ahillworks Master

Joined: 18 Nov 2007 Posts: 308 Location: Orlando FL
|
Posted: Tue Dec 23, 2008 8:04 pm Post subject: |
|
|
.30 should work as long as the sheet is not to big. I had my former using elements from a toaster oven and would have work great had it been smaller. |
|
Back to top |
|
 |
|
|
You cannot post new topics in this forum You cannot reply to topics in this forum You cannot edit your posts in this forum You cannot delete your posts in this forum You cannot vote in polls in this forum
|
Powered by phpBB © 2001, 2005 phpBB Group
|