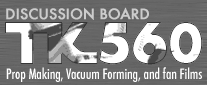 |
www.TK560.com Vacuum Forming, Movie Prop, Sci-fi and GIjOE Forum
|
|


|
View previous topic :: View next topic |
Author |
Message |
coffeehedake Novice

Joined: 10 Feb 2010 Posts: 66 Location: Burlington, CT
|
Posted: Wed Feb 10, 2010 6:32 pm Post subject: Greetings, and *salute* |
|
|
Hello all, stumbled into these forums after reading so many guides online, and buying a slew of books on vacuum-forming, mold-making, etc, that were recommended here on the TK560 boards, and elsewhere.
I'm fairly new to costuming, vacuum-forming, and the like, but after reading through the forums, I am very optimistic.
I'm 26, on the East Coast, currently working as a Certified Apple Technician / Network Admin for my local school district.
Went to school years ago for Game Art & Design, which brings me to my current project:
Right now I'm gathering materials and parts for my first homebuilt CNC Router / Mill, which I plan to donate to the school I work for after I get it up and running. I bring a lot of 3D Studio MAX experience to the table, but I'm not exactly handy with a jigsaw.
I'd like to machine bucks for vacuum-forming with the machine, and I'm really excited to see that others here have had success with the process. I'm also working on a self-contained (not the kitchen oven, at the fiance's request) vacuum-former for building a TK armor set.
I hope I can lend a hand to those who already have CNC machines up and running, but may not have a solid grasp on the 3D modeling aspect. (I can definitely work with you on that) Perhaps we can assist each other to get the best results possible.
If anyone is in the CT or New England area, and would like to combine efforts, I'd be glad to help out in real-life as well as here on the forums.
Glad to be here, and I really hope to contribute as much as I can. Thanks everyone! _________________
 |
|
Back to top |
|
 |
jdougn Guru
Joined: 18 Mar 2009 Posts: 714 Location: Louisville KY area
|
Posted: Thu Feb 11, 2010 8:11 am Post subject: |
|
|
Hey, glad you're here. Sounds like you've got a great start with this hobby by reading up and doing the research!
CNC is the next step for me in the process of mold making and trimming vac formed parts. Any recommendations on open source / cheap design software for a CNC newbie?
DougN _________________ DougN - Just in case you're wondering, I got my "rating" legitimately... by posting aimless drivel, useless advice, and pointless questions. |
|
Back to top |
|
 |
coffeehedake Novice

Joined: 10 Feb 2010 Posts: 66 Location: Burlington, CT
|
Posted: Thu Feb 11, 2010 9:55 am Post subject: Recommendations |
|
|
jdougn wrote: | Any recommendations on open source / cheap design software for a CNC newbie? |
I'm right there in the same boat with ya. Though so far, I've found other's recommendations here (i.e. Culvan and Danipe70) to be extremely useful.
I use 3D Studio MAX all the time, and thusly a lot of my research has been based around that. Useful for 3DSMAX is the CNCtoolkit which is open-source. The software also works with gMax, which is the lite version of Studio MAX designed with game modders in mind. (gMax doesn't have a file export function that I know of)
Basically the CNCtoolkit attempts to take 3D data and generate G-Code for your CNC software. From what I understand you still need something to control your machine. As Culvan says in his thread, you can use Mach3 to take the G-Code and push it out to your machine as instruction. Culvan also mentions EMC2 which I am very interested in. I'm familiar with Linux, and an open-source solution to control my machine would be fantastic. However, it would appear that there is a lot of configuring to be done, before getting your machine going. I'm going to play with both options and see what works best for me. I don't mind paying the $175 for the license of Mach3, if it means I can get things running faster, and have some support, but I'd prefer to use Linux.
Something interesting: There also seems to be a growing community of Google Sketchup users outputting to CNC Mills. Apparently there is a way to export Sketchup shapes to CamBam which is free and can generate the G-Code. However, I'm not entirely sure that CamBam will write 3D G-Code, it appears to want to cut in 2 Dimensions (X, Y). I'll post more as I discover it, currently enlisting the assistance of 2 tech ed teachers in the construction of the CNC Router chassis. _________________
 |
|
Back to top |
|
 |
Culvan Novice
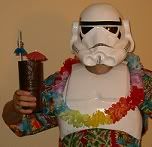
Joined: 20 May 2008 Posts: 85 Location: Kansas City, MO
|
Posted: Thu Feb 11, 2010 10:35 am Post subject: Re: Recommendations |
|
|
coffeehedake wrote: | I don't mind paying the $175 for the license of Mach3, if it means I can get things running faster, and have some support, but I'd prefer to use Linux.
|
I've got absolutely nothing against linux, but I wanted to keep all the software on the same operating system. I didn't want to have to setup a second computer or dual boot into a different OS for CAD/CAM and machine control. I'll point out that if you intend to donate this to a school then you can request the education discount. It'll probably knock $50 off the price of MACH3.
My problem with the CNC-toolkit is that it is not milling software. It won't correct for the actual location of the cutting surface compared to the model. It's described in the toolkit handbook. I've been playing around with deskproto a little bit. They offer a 30 day trial of 3 different software packages. If you had a computer lab to work with you could probably rotate it through different computers for quite a while.
http://www.deskproto.com/
My big weakness is that I'm not very good with CAD programs. I was trying to make K9's head (from Doctor Who) and I couldn't make a decent looking model. I'd really like to make a clone trooper helmet, but my attempts have all failed so far.
Andy |
|
Back to top |
|
 |
coffeehedake Novice

Joined: 10 Feb 2010 Posts: 66 Location: Burlington, CT
|
Posted: Thu Feb 11, 2010 11:16 am Post subject: |
|
|
Culvan wrote: | My big weakness is that I'm not very good with CAD programs. I was trying to make K9's head (from Doctor Who) and I couldn't make a decent looking model. I'd really like to make a clone trooper helmet, but my attempts have all failed so far. |
I'd love to help if I can. I can mesh out a 3D Model for you, all I will need is some decent photos for a source, and measurements, if available. I can probably churn out an ok model in a couple of days (I'll have to reinstall Max, I just upgraded to Win7 x64).
What format works best for you for the model? _________________
 |
|
Back to top |
|
 |
stormtrooperguy Expert

Joined: 24 Sep 2009 Posts: 126
|
Posted: Thu Feb 11, 2010 3:37 pm Post subject: Re: Greetings, and *salute* |
|
|
coffeehedake wrote: |
If anyone is in the CT or New England area, and would like to combine efforts, I'd be glad to help out in real-life as well as here on the forums.
|
Hello there! I'm in Waltham MA, about 15 minutes off of rt 95. I'm getting REALLY close to finished with my vac former. I've been wanting to make some contacts with CNC capabilities to work on prototyping parts that way.
I don't do stormtrooper myself (don't let the name fool you!), but have made a full set of clone trooper armor. |
|
Back to top |
|
 |
coffeehedake Novice

Joined: 10 Feb 2010 Posts: 66 Location: Burlington, CT
|
Posted: Thu Feb 11, 2010 5:26 pm Post subject: |
|
|
Hey Stormtrooperguy!
I'm buying the MDF tomorrow from Home Depot to get building started on this rig. Once it's up and running you're welcome to use it, though I'll have to check how we'll get you in, as it will be living in a middle school. (Should be okay after hours)
We've got a Vac Former in the high school already, and I'll be building one in the basement as well. You'll have a workshop-away-from-home! Haha!
SoOooo... look what came in the mail today:
Yippee! Only 3 more books in the mail... they should all arrive tomorrow. Amazon is awesome.
Also, I was marveling at your clone armor, earlier. That is phenomenal!
Eventually, I'm hoping to build a full set of Dark Trooper armor. As one of The Dented Helmet forum members has started. I'm starting with the TK armor as it's more documented, and I'd like to get some experience under my belt before I experiment too much.
Yeah, you're welcome to use the machine, or just hang out and shoot the breeze, talk some SW, etc.
I travel to West Springfield now and again to visit friends, not too far. _________________
 |
|
Back to top |
|
 |
Culvan Novice
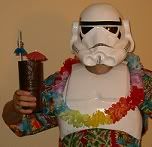
Joined: 20 May 2008 Posts: 85 Location: Kansas City, MO
|
Posted: Fri Feb 12, 2010 1:11 pm Post subject: |
|
|
coffeehedake wrote: | Eventually, I'm hoping to build a full set of Dark Trooper armor. As one of The Dented Helmet forum members has started. I'm starting with the TK armor as it's more documented, and I'd like to get some experience under my belt before I experiment too much.
|
That guy gets around.
Thanks for the modeling offer. I'll gather my clone helmet reference photos and send them to you. The K9 head seems like it should be extremely simple to make. I'd really like help doing it myself so I can get the basics down. I've got a diagram with views from all 6 sides. Perhaps I'll start a thread here about basic modeling techniques and see if I can get some help along the way.
Here's what K9 looks like.
Andy |
|
Back to top |
|
 |
coffeehedake Novice

Joined: 10 Feb 2010 Posts: 66 Location: Burlington, CT
|
Posted: Fri Feb 12, 2010 3:36 pm Post subject: K9 |
|
|
Culvan wrote: | That guy gets around. |
He certainly does.
Culvan wrote: | The K9 head seems like it should be extremely simple to make. I'd really like help doing it myself so I can get the basics down. I've got a diagram with views from all 6 sides. |
Yep, looks like a slightly squished box that tapers toward the back.
A good way to get started in modeling, besides GMAX, is a nice program I've used for years (and paid the $20 reg fee for, totally worth it for game modding) is MilkShape3D.
For a project like this, it's a perfect example to start learning 'box modeling'. This is one of the first things you learn in Studio MAX class, and it's the easiest to grasp. I can do a quick write up, but there's a TON of tutorials out there for box modeling a head, human figure, etc.
If you've got the diagram view I can start whipping up a quick model, and screenshot my progress for you, so you can see my method, if you like. You can attack something like this from a lot of different angles:
Box modeling (like I mentioned)
Polygon / Mesh Modeling
Spline modeling (similar to CAD, but adds a surface modifier)
NURBS (Non-Uniform Rational B-Splines) which is similar to the above method, but a little more organic.
I'd probably go with one of the first three. The learning curve for box and polygonal modeling is not steep, Spline and NURBS can get pretty confusing for a first-time modeler.
If you've ever seen people using Pepakura to unfold 3D objects into paper prototypes, you've seen polygonal modeling. Basically you're building a shape out of a bunch of quads (boxes, 4 sided, comprised of two triangles) and triangles. It's like putting together a big puzzle. Pepakura actually does the reverse, where it tears down a 3D model into quads and triangles that a human could fold from paper, and figures out the best way to do that.
I can help either way you prefer, or both, up to you.  _________________
 |
|
Back to top |
|
 |
coffeehedake Novice

Joined: 10 Feb 2010 Posts: 66 Location: Burlington, CT
|
Posted: Fri Feb 12, 2010 4:46 pm Post subject: K-9 |
|
|
Found some plans. Click here if the link is wonky.
Also found this guy's blog, as he's building one too.
I'm downloading the CAD drawings, as StudioMAX loves CAD files, it eats them for breakfast. Should be able to use the CAD lines as a perfect guide. _________________
 |
|
Back to top |
|
 |
coffeehedake Novice

Joined: 10 Feb 2010 Posts: 66 Location: Burlington, CT
|
Posted: Fri Feb 12, 2010 5:32 pm Post subject: K-9 |
|
|
Let me know when you have that thread started.
Got the CAD file cleaned up, and imported into Studio MAX. Makes a great template, but I had to delete all of the grid lines the guy made when creating the file. (No biggee)
In case anyone's interested, heres an OOOOOOoold render of a custom vibro-axe I modeled for fun:
 _________________
 |
|
Back to top |
|
 |
jegner Site Admin

Joined: 30 May 2003 Posts: 2144 Location: Texas, USA
|
Posted: Tue Feb 16, 2010 11:01 am Post subject: |
|
|
Welcome to the board! Neat stuff, I hope you can share some of your knowledge with the group. |
|
Back to top |
|
 |
coffeehedake Novice

Joined: 10 Feb 2010 Posts: 66 Location: Burlington, CT
|
Posted: Tue Feb 16, 2010 11:23 am Post subject: |
|
|
Thanks Jegner, I hope so too! _________________
 |
|
Back to top |
|
 |
coffeehedake Novice

Joined: 10 Feb 2010 Posts: 66 Location: Burlington, CT
|
Posted: Tue Feb 16, 2010 5:16 pm Post subject: The Book Collection |
|
|
The rest of my library (for now) has finally arrived! Including Jegner's book. Totally worth the purchase; I'd recommend it, and Thurston James' book as well.
The last book by Vincent Gingery is pretty good, though focuses on building a 110V former. (I'm reading them all now, and am half-way through James' book) I've read Jegner's, and the CNC Machine book already. _________________
 |
|
Back to top |
|
 |
coffeehedake Novice

Joined: 10 Feb 2010 Posts: 66 Location: Burlington, CT
|
Posted: Fri Feb 19, 2010 4:01 pm Post subject: Instant Message |
|
|
Just thought I'd throw this out there... anyone looking to shoot the breeze, feel free to IM me, just check my profile for my handle. _________________
 |
|
Back to top |
|
 |
|
|
You cannot post new topics in this forum You cannot reply to topics in this forum You cannot edit your posts in this forum You cannot delete your posts in this forum You cannot vote in polls in this forum
|
Powered by phpBB © 2001, 2005 phpBB Group
|