View previous topic :: View next topic |
Author |
Message |
IMMark Expert
Joined: 18 Nov 2010 Posts: 189 Location: Columbus, Ohio
|
Posted: Mon Oct 24, 2011 3:59 pm Post subject: |
|
|
Nice job.
Thanks for posting the pictures and good stuff in the write up!
Mark |
|
Back to top |
|
 |
RFC Newbie
Joined: 22 Aug 2011 Posts: 19 Location: Western PA
|
Posted: Mon Oct 24, 2011 4:10 pm Post subject: |
|
|
Excellent job on your reporting. Photos help with understanding the process. If you don't mind my asking, what did you have to pay for the used hot water tank and did you sandblast the outside or is that some kind of paint in the last picture?
You are doing great. Keep up the good work. Bob _________________ Cheers, Bob |
|
Back to top |
|
 |
PARATECH1 Expert

Joined: 19 Mar 2008 Posts: 112 Location: ALABAMA
|
Posted: Mon Oct 24, 2011 4:45 pm Post subject: |
|
|
IMMark wrote: | Nice job.
Thanks for posting the pictures and good stuff in the write up!
Mark |
Thanks. I appreciate it. |
|
Back to top |
|
 |
PARATECH1 Expert

Joined: 19 Mar 2008 Posts: 112 Location: ALABAMA
|
Posted: Mon Oct 24, 2011 4:54 pm Post subject: |
|
|
RFC wrote: | Excellent job on your reporting. Photos help with understanding the process. If you don't mind my asking, what did you have to pay for the used hot water tank and did you sandblast the outside or is that some kind of paint in the last picture?
You are doing great. Keep up the good work. Bob |
I finally found an old used tank for $30.00. I had called electric companies, gas companies, plumbers, and salvage yards all over the dang place but could never get them to give or sell me one. I finally was riding by somewhere and saw one in a dudes yard leaning against his shed. I asked him about it. He was wanting to sell it. I haggled and bought it. The gas and electric places said that they could not sell old tanks anymore even though they were just going to throw them away. The salvage places would say that they would save you some but never would. The plumbers were the same. I was coming close to buying a new tank and just shelling it out.
As for the outside of the tank - It was just shelled out, sanded, primed and painted. |
|
Back to top |
|
 |
PARATECH1 Expert

Joined: 19 Mar 2008 Posts: 112 Location: ALABAMA
|
Posted: Mon Oct 24, 2011 7:49 pm Post subject: |
|
|
Looking at and building the carrier frame for this type of machine can look pretty intimidating at first. The big thing is to break it down in simple steps. You will weld various parts together to become one piece. You will then weld several pieces together to become another piece. Once these pieces are made you will then weld them together to form one big awesome looking piece.
If you don't know how to weld, no worries. I didn't either prior to starting this machine. The books and videos I found sorta sucked and didn't really help. I started with a Mig welder because all of the info I could find said that this would be the easiest. I ended up buying two seperate Harbor Freight welders, a Lincoln 140 and a Lincoln 180. I had no one to show me how to properly use one to get the settings right. Needless to say, it freakin sucked. I contacted the manufacturers with the type metal I was using and asked for the proper settings (even though the settings are on the welders themselves) and the welders still sputtered and sucked.
- Tip - When you practice, make sure you practice on the same type of metal you will be using for your vacuumformer. Get used to whatever type of welding you eventually will use. You can easily and very quickly melt a big giant sloppy hole into the metal you are welding on. Make sure you practice on both the angle iron and square tubing.
In the end I got an arc welder. With arc welding I was welding right off the bat. For the guage material you will use on this machine you will only need thin welding rods. The thicker ones burned and melted the metal you will be using super fast. Again I am sure I was not doing it right because I was a beginner. I am actually still a beginner. I just know a little more now than when I first started. I can make decent clean welds with a cheapo machine.
In a later post I will go into detail of using a decent ($100.00) welder, the exact welding rods to get along with the exact settings for that welder.
Before I eventually learned how to use the cheaper welders properly I ended up getting big time frustrated and went overboard. I wanted a big welder that also had at least a 60 amp electrical output. I needed the output to power the vacuumer since my shop was not wired yet. I ended up getting a really good deal on a used Miller Big Blue 502D.
I thought at first it might be total overkill but I have used the heck out of both the welding functions and the generator functions.
When you begin to weld you will definately want at least 4 "90" degree welding magnet holders. They come in big time handy. Here is a link for what you can look for:
http://www.harborfreight.com/4-3-4-quarter-inch-multipurpose-magnet-holder-1938.html
These hold all your frames and uprights together and straight while you are welding. They simply work great. Again, use the 20% off coupon. Join Harbor Freights e-mail / mailing list for all sorts of other discounts.
Again I will later post a lot more on how to weld your parts using a cheap but good welder. |
|
Back to top |
|
 |
PARATECH1 Expert

Joined: 19 Mar 2008 Posts: 112 Location: ALABAMA
|
Posted: Mon Oct 24, 2011 8:43 pm Post subject: |
|
|
Trying to decide what color to paint the frame.
 |
|
Back to top |
|
 |
PARATECH1 Expert

Joined: 19 Mar 2008 Posts: 112 Location: ALABAMA
|
Posted: Mon Oct 24, 2011 8:55 pm Post subject: |
|
|
I deferred from the instructions and used these type of furniture sliders inbetween my frame uprights. They fit and work great after you grind off some of the rear stubs.
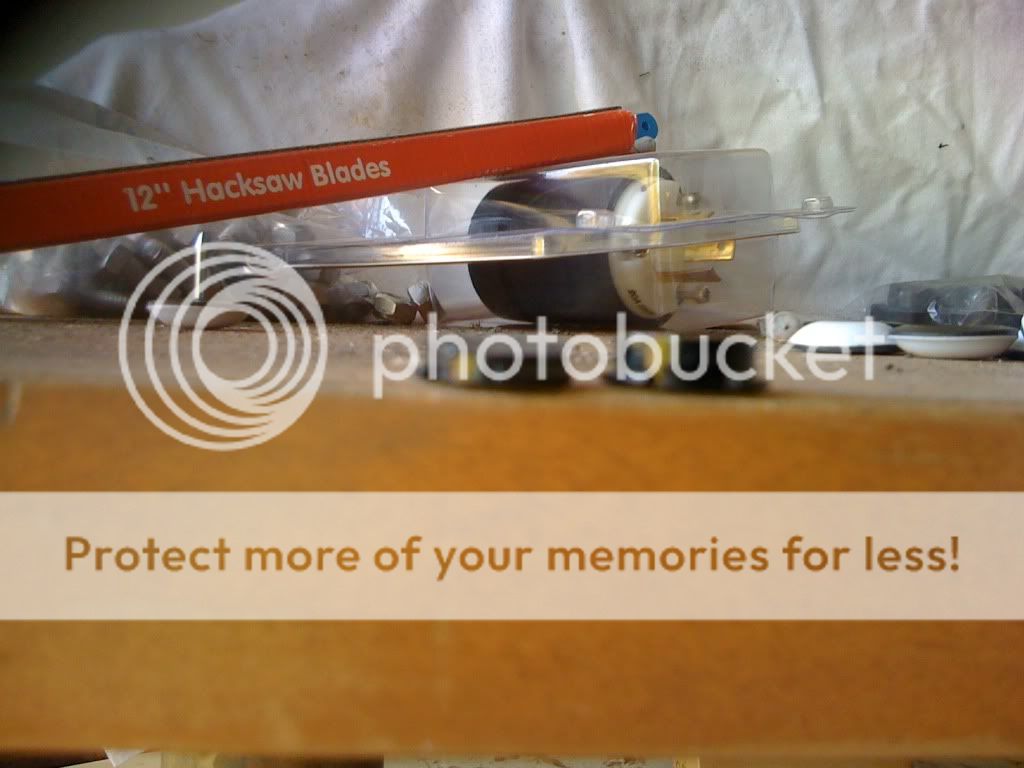 |
|
Back to top |
|
 |
PARATECH1 Expert

Joined: 19 Mar 2008 Posts: 112 Location: ALABAMA
|
Posted: Tue Oct 25, 2011 6:01 am Post subject: |
|
|
I apoligize for some of the blurriness of some of the above photos. Sometimes when you are in the middle of doing somethine and stop in the middle of it to take a photo I wasn't at times concentrating on the photo or looking back to see if it was good.
If you start building your protoform machine and need more info or a photo of a particular area I will totally try to help. A lot of times one good photo will help more than pages of text. |
|
Back to top |
|
 |
PARATECH1 Expert

Joined: 19 Mar 2008 Posts: 112 Location: ALABAMA
|
Posted: Tue Oct 25, 2011 6:27 pm Post subject: |
|
|
Make sure when you weld everything together you have it all totally lined up where it it supposed to go. Especially the two bars outside the carrier frame square. These really need to be parallel to each other from opposite sides. Also make sure they are totally straight up and down. The two bars have to be able to eventually slide inbetween you two sets of uprights on the chassis. I had to redo mine a time or two to get them just right. |
|
Back to top |
|
 |
PARATECH1 Expert

Joined: 19 Mar 2008 Posts: 112 Location: ALABAMA
|
Posted: Tue Oct 25, 2011 7:19 pm Post subject: |
|
|
After you get the main portion of your carrier frame done you can start welding on your clamp tabs ( If you are using them ).
I ended up using these clamps from Harbor Freight:
http://www.harborfreight.com/200-lb-horizontal-toggle-clamp-96237.html
They look like they are going to work really well. They are usually $5.00 each (When not on sale ). Sometimes you can find them on sale for around $3.00 each. And this $3.00 is prior to your 20% off coupon. If you subscribe to their mailing list they will sometimes send you a 20% off coupon off of your order total. This beats having to buy each item seperately to get your discount ( I'm cheap - So what! ), When they send you this coupon go ahead and make you several copies of it also so you will have them just in case you need something else before they expire.
I cut all of my tabs out of 2" angle iron using a chop saw.
Again, if you are buliding this machine yourself I highly recommend getting a chop saw. You will use the heck out of it.
Line up your clamp on top of your tab and mark it. Then using a drill press drill your holes. Make sure your tab holes line up with your clamp holes.
After you get all your tabs cut and holes drilled you need to decide where you are going to place them on your frame. The number of tabs or clamps will vary on the size of your machine. I have seen a number of posts where people have constant escaping air and can't get a good seal. On some of the machines a few more ( and stronger) clamps may have helped to prevent this. I may have got a few more than I needed but I wanted to be sure.
Use a C-clamp to hold the tab in place and weld it in place. Once this one is done go to the next one.
- Tip - When choosing your tab placement make sure you take into sideration the right and left side post on the outside of the frame. Also don't make the mistake I did of placing one underneath where your electrical box will be. It will hit it when you raise your frame. I later had to cut one off and move it elsewhere. You also have to repaint the area you just welded and the area where you cut a tab off. It can sometimes be a pain to get your tabbed and clamped carrier frame out of the chassis.
"The next step is attaching your clamps". |
|
Back to top |
|
 |
PARATECH1 Expert

Joined: 19 Mar 2008 Posts: 112 Location: ALABAMA
|
Posted: Thu Oct 27, 2011 1:47 pm Post subject: |
|
|
When it comes to attaching your clamps to your tabs you can simply use small bolts / nuts or you can do it in a more professional manner. This would involve the use of a rivet gun. If you have never used one before they are totally easy to use. You can usuaslly find a rivet gun and a box of rivets for around $10.00 at Harbor Freight, auto shops (especially in the big bin of various tools for $5.00 - $10.00 each). Most other hardware stores will also have them.
Think of a rivet as a little sword with four parts.
1. - Pommel (The ball or bottom of the sword handle)
2. - Grip (The handle of the sword)
3. - Cross Guard (The big piece between the handle and the blade)
4. - Shaft (The blade)
You start by drilling a hole through the pieces you are wanting to join together. The clamps should already have holes in them. For this project you can use 1/8" rivets.
The 1/8' comes from the width of what would be the grip of a sword. The four holes in each clamp should line up with the holes you are drilling in your tabs.
Once this is done place your rivets ( pommel / ball side facing downward)through the holes.
-Tip - Go ahead and stick all four rivets in the four drilled holes through the clamp followed by the tab. With all four in at the same time it helps to prevent any movement and helps to make sure all four rivets will fit properly.
The head of your rivet gun will have a hole in it. The shaft (blade) portion of the rivet will go all the way in here.
You need to make sure the shaft is all the way in the hole of the rivet gun. Ou will push in to make sure the cross guard section of the rivet is against the base of your clamp. You will pull the handles of your rivet gun together a few times. You need to make sure between each pull that the shaft is still all the way in your gun. After a few pulls a portion of the shaft will pop off. You are done with that one - simple as that.
Once you have used a rivet gun for even a few minutes you will be glad you didn't use small nuts and bolts. |
|
Back to top |
|
 |
PARATECH1 Expert

Joined: 19 Mar 2008 Posts: 112 Location: ALABAMA
|
Posted: Thu Oct 27, 2011 1:51 pm Post subject: |
|
|
Here are a few photos of attaching your clamps to your tabs.
 |
|
Back to top |
|
 |
PARATECH1 Expert

Joined: 19 Mar 2008 Posts: 112 Location: ALABAMA
|
Posted: Thu Oct 27, 2011 4:18 pm Post subject: |
|
|
I have taken several of the above photos down to later place back in a different section on the lift arm portion of the protoform machine. They were prematurely put up by accident. |
|
Back to top |
|
 |
jdougn Guru
Joined: 18 Mar 2009 Posts: 714 Location: Louisville KY area
|
Posted: Sat Oct 29, 2011 1:05 pm Post subject: |
|
|
Looks like you're going great work! I enjoy seeing a well thought out machine go together. Waiting to see your first pull!!
dn _________________ DougN - Just in case you're wondering, I got my "rating" legitimately... by posting aimless drivel, useless advice, and pointless questions. |
|
Back to top |
|
 |
PARATECH1 Expert

Joined: 19 Mar 2008 Posts: 112 Location: ALABAMA
|
Posted: Sat Oct 29, 2011 7:20 pm Post subject: |
|
|
jdougn wrote: | Looks like you're going great work! I enjoy seeing a well thought out machine go together. Waiting to see your first pull!!
dn |
Thanks, I really do appreciate the good comments. I have been on these boards for awhile and have read each and every single post. I am only able to build this machine from learning from each individual who has commented on these boards.
When at the beginning of this post in thanking the moderators, I wasn't just blowing smoke. I highly thank each one of them for even making these forums possible. |
|
Back to top |
|
 |
|