View previous topic :: View next topic |
Author |
Message |
Kookas Newbie
Joined: 21 Apr 2006 Posts: 22 Location: Australia
|
Posted: Sun Apr 23, 2006 2:25 am Post subject: Another Aussie Build |
|
|
Hi,
I have been building a vacu-form table over the last week, based on this web site design. So far I have made the platen and flip flop frame. I have made it large enough so that I can make radio controlled model car bodies (62cm x 51cm).
So far I have found everything I need fairly easily. The NiChrome wire was the easiest because it came in 600W lengths (From Flagstaff Electrical in Adelaide ~$7 each). That made the maths easy, I just need to stretch it until the resistance is right. Here in Australia we have 240V power. If I get the resistance down to 5Ohms per segment (I think thats what you said!?) It should only require 10A of power. This would be easy to manage with our current supply. It just so happens that I am having the house re-wired in a couple of weeks so I'll be making a circuit expecially for this!
Dad is an electrical engineer and has looked over all the wiring. I was surprised that it is all ok. I notice a lot of you guys using chicken sticks thats pretty funny (but I totally understand).
I have not yet started the oven side yet, I'll start that this week. I have found the hardi-flex fibre cement at the local hardware warehouse (~$16 sheet). The rest I had lying around.
I was planning to post a picture but my website is playing up at the moment, I'll get it posted soon.
Thanks again for all this fantastic information.
David Koukourou |
|
Back to top |
|
 |
ANH trooper Master
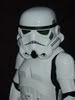
Joined: 20 Oct 2005 Posts: 305 Location: UK
|
Posted: Sun Apr 23, 2006 4:57 am Post subject: |
|
|
Welcome David!
I'm looking forward to seeing your vacuum former mate.
-Paul. |
|
Back to top |
|
 |
Kookas Newbie
Joined: 21 Apr 2006 Posts: 22 Location: Australia
|
Posted: Sun Apr 23, 2006 5:04 am Post subject: |
|
|
here is the picture I promised, I'll send more as I progress:
 |
|
Back to top |
|
 |
jegner Site Admin

Joined: 30 May 2003 Posts: 2144 Location: Texas, USA
|
Posted: Sun Apr 23, 2006 10:42 am Post subject: |
|
|
She is a beauty! Keep us posted. I'm glad this site helped you make a vac-table.
Jim |
|
Back to top |
|
 |
crashmann Guru

Joined: 27 Sep 2005 Posts: 501
|
Posted: Sun Apr 23, 2006 9:07 pm Post subject: |
|
|
RC Car bodies, that's fantastic! That's another one of my projects for down the road It sure is cheaper to pull your own than pay the hobby shop after your car has met the curb!
Are you going to be using Lexan? I ordered a few sheets, but I haven't tried it yet.
Make sure you are shooting for 94 ohms of resistance per segment, then a total resistance of 23 ohms when it's all connected together.
Those electrical engineers are pretty smart folks (I work with a few of them). But it must be sad knowing there is no more magic in the world
Charlie
TI-386 |
|
Back to top |
|
 |
Kookas Newbie
Joined: 21 Apr 2006 Posts: 22 Location: Australia
|
Posted: Mon Apr 24, 2006 3:37 am Post subject: |
|
|
I was looking for a particular model car body and they didn't have it. Thats when I figured it would be easier to make one myself! I would like to use polycarbonate (Not sure if thats the same as Lexcan, I think it might be).
Actually while I am thinking, I noticed that the only application I seem to find people using this for is for Stormtrooper Armour. I actually first started thinking of this stuff about a year ago when I was making Samurai Armour. I made it out of PVC pipe and had to use a heat gun. The gun was frustrating because it only heated a small area at a time. A friend who was making it with me has gone on to make a table and a full suit of Armour out of Polycarbonate. It is so strong, I can't shoot my 50 pound compound bow through it! he uses 6mm and 8mm polycarbonate and gets a really good result. I want to try PVC though as it would be much cheaper.
here are some photos:
 |
|
Back to top |
|
 |
Kookas Newbie
Joined: 21 Apr 2006 Posts: 22 Location: Australia
|
Posted: Mon Apr 24, 2006 6:50 am Post subject: |
|
|
I just measured the resistance in the coils I bought. They are between 91 and 96 Ohms. Stretching doesn't seem to do much but I haven't stretched them completely yet. I was going to ask, do you stretch the coils then draw the spirals or the other way around. Now I geuss it doesn't matter so much.
I have drawn the spiral and will stretch the coils to suit. I am thinking all of your resistance measuring is more to do with the fact that you have the NiChrome wire in 1 long length rather than 4 600W lengths as I have.
regards
David K
(Now, if I could only find the ceramics!! ) |
|
Back to top |
|
 |
crashmann Guru

Joined: 27 Sep 2005 Posts: 501
|
Posted: Mon Apr 24, 2006 8:30 am Post subject: |
|
|
Whoa, that's some nice samurai armor!
You are correct, Lexan is just GE's brand name for polycarbonate.
If the resistance for the whole coil is around 94 ohms, and you've got four of them, then you're all set! Stretching the wire isn't going to change the resistance (unless it is tightly coiled, and they are touching). I drew the pattern one the oven base first, then measured the total length needed to cover spirals. next, I stretched the coils just a little shorter than the length of the spirals and worked my way around the base.
Good luck, and keep us updated with your progress
Charlie
TI-386 |
|
Back to top |
|
 |
Kookas Newbie
Joined: 21 Apr 2006 Posts: 22 Location: Australia
|
Posted: Sun Apr 30, 2006 2:16 am Post subject: |
|
|
Hi,
Today I have been working on the oven. I found some ceramic insulators from a farm supplies shop for 66c each. I used 50. They are a little larger than I wanted but they are the best I could find for now. The heater coil was pretty easy to stretch out and mount. I am now waiting for Dad to come over and hook it up to 240V (he's the electrical engineer!).
I have also biuld the oven box. I used a raised box under the oven floor to insure insulation from the posts and to provide the correct height.
I have the oven as a separate unit from the table itself so that I can store it on the vacuum platen when I am not using it.
I hope to be melting plastic next weekend!
here is a picture of what I have done so far:
 |
|
Back to top |
|
 |
jegner Site Admin

Joined: 30 May 2003 Posts: 2144 Location: Texas, USA
|
Posted: Sun Apr 30, 2006 8:26 am Post subject: |
|
|
Most impressive! |
|
Back to top |
|
 |
crashmann Guru

Joined: 27 Sep 2005 Posts: 501
|
Posted: Sun Apr 30, 2006 2:44 pm Post subject: |
|
|
That looks fantastic!
It took me a very long time to build what you've accomplished in just a few weeks. As Darth Vader said... "Impressive. Most impressive!"
Charlie
TI-386 |
|
Back to top |
|
 |
Kookas Newbie
Joined: 21 Apr 2006 Posts: 22 Location: Australia
|
Posted: Sun Apr 30, 2006 7:16 pm Post subject: |
|
|
Thanks guys for the encouragement. I also gyprocked the ceiling last weekend. I also can't beleive how much I have done. It probably helps that my workshop is also where my tv is now and so I spend a fair bit of time in there (we just had new carpet laid in the lounge room so I am too paranoid to go in there lest my wife will kill me )
I have just returned from a moulding and casting shop over the road from my work.http://amcsupplies.com.au I have some poly urethane resin which I'll make a mould out of tonight. it should come out nice and hard. If it is not strong enough, I'll fill it with plaster. The guy told me that poly urethane will not leave a powder residue on the plastic after vacu-forming. It will also bring out the detail really well. I'll post a picture when I've done it.
regards
David K |
|
Back to top |
|
 |
Kookas Newbie
Joined: 21 Apr 2006 Posts: 22 Location: Australia
|
Posted: Mon May 01, 2006 8:46 am Post subject: |
|
|
Hi,
I just finished my first mould. It came out so well I thought I would show it off. I heard of someone making a Darth Vader suit out of the same material, I was amazed at the quality and strength of the plastic. Also the detail came out really well.
The only thing I am not sure of is how hot the plastic will heat the mould. This resin is only able to get to about 70 Degrees C. I am pretty sure the vacuum would cool it down pretty fast, do you think?
cheers
David K
 |
|
Back to top |
|
 |
jegner Site Admin

Joined: 30 May 2003 Posts: 2144 Location: Texas, USA
|
Posted: Mon May 01, 2006 9:54 am Post subject: |
|
|
Most casting resins heat up to 165 Degrees F. [73 degrees C] and HIPS has a forming temp of 335-350 Degrees F. [168-176 degrees C]
I use bondo, a plastic based patching resin for car parts, and it seems to withstand the heat just fine. Best to test the materials before running the risk of damage to the mold. Mix a batch up, and make some test pulls. If the pulls hold up fine, then you can try a pull with your car body master.
Note, the thinner the material you use, the more detail. Those lines on the doors, will be subtle on the pull unless you are pulling .040 [1.016mm] or thinner stuff.
Jim |
|
Back to top |
|
 |
crashmann Guru

Joined: 27 Sep 2005 Posts: 501
|
Posted: Mon May 01, 2006 8:45 pm Post subject: |
|
|
Wow, great looking mold! Although the plastic is very hot when it first comes down, it does cool off quickly with some of the heat going into the mold, and the rest transferring to the air. With thinner plastic, it should cool off very quickly. Also, I recall the plastic sales guy said polycarbonate is thermoformed at a MUCH lower temperature than styrene (around 200 degrees F or 93 degrees C). But there's only one way to find out if the resin can survive a transient jump in temperature - pull some plastic over it!
So, do you run onroad gas or electric RC cars? I ran the heck out of my HPI Nitro RS4's (way back in the day...) I used a micrometer to check the thickness of some car bodies, and they read .020 on the sides, so Jim may be right on recommending .040 or .030 polycarbonate. I can't wait to see your body (boy, that just doesn't sound right )
Here's a couple of shots of the old venerable Clod Buster (with a few mods )
Charlie
TI-386 |
|
Back to top |
|
 |
|