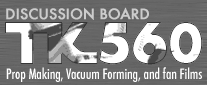 |
www.TK560.com Vacuum Forming, Movie Prop, Sci-fi and GIjOE Forum
|
|


|
View previous topic :: View next topic |
Author |
Message |
drcrash Guru

Joined: 04 Sep 2006 Posts: 705 Location: Austin, Texas
|
Posted: Tue Sep 05, 2006 8:19 am Post subject: Convection Oven Ideas [SPLIT FROM ANOTHER THREAD] |
|
|
I forgot to mention the plastic sagging away from the coils in an over-and-under design; that seems like a big plus to me, both in terms of even heating and reducing the chance of a meltdown.
On the other hand, I'm considering building a simple forced air, convection-type oven, where that may matter much less.
(Anybody else here tried that? My impression is that a convection oven could be about as simple as anything else, and more flexible if you separate the air-heating unit from the oven/plenum part. I might even be able to make an expandable and collapsible oven, which would be very convenient for my purposes; I have no dedicated shop space at all.) |
|
Back to top |
|
 |
crashmann Guru

Joined: 27 Sep 2005 Posts: 501
|
Posted: Tue Sep 05, 2006 8:45 am Post subject: |
|
|
Hi Dr. Crash!
(nice name by the way )
One of the advantages with the nichrome wire is that the plastic is heated by two sources - The wire heats up the air surrounding it, and this hot air rises to warm the plastic - And Infra-red heat radiating from the coils striking the plastic. So I'm not sure if swirling the air around would make that much of a difference for ensuring even heating of the plastic sheet.
The only experience with a forced air oven is when I worked at Pizza Movers. It was a gas fired oven with blowers that forced the air throughout the heating chamber as the pizza rolled through on a conveyor belt.
How would you propose moving the air around in your oven?
Charlie
TI-386 |
|
Back to top |
|
 |
drcrash Guru

Joined: 04 Sep 2006 Posts: 705 Location: Austin, Texas
|
Posted: Tue Sep 05, 2006 1:02 pm Post subject: convection ovens, vacuum forming craft foam, etc. |
|
|
Hi Charlie,
As I understand it, serious convection ovens heat things about as evenly as anything can. A lot of plastics and printed circuit board processing systems use them.
(For example, some processing of PCB's relies on heating the board to just the right temperature all over, to affect certain components in the right way, but NOT heat it much higher anywhere because that would degrade other components.)
Home convection ovens for food are not a lot like the serious industrial ones; they're basically just regular ovens with a fan to move the air around and reduce hotspots *somewhat*. The industrial convection (or "impingement") ovens do a much better job by moving the air quickly and systematically, to almost entirely eliminate hotspots.)
The basic idea is that if you can't guarantee that the radiant heat is very evenly distributed, don't use it---just blow uniformly hot air fairly evenly across the whole thing that you want to heat.
The trick to making this heat very evenly is that you have to blow the air fast enough that it *doesn't* lose a big fraction of its heat as it moves across the object one time; if it did, it would be substantially warmer going over the near side of the object, and cooler when it gets to the far side.
(For thin flat stuff like plastic sheets, another way to reduce that effect is to have a U-shaped airflow around the object, blowing the hot air across the top of the sheet and sucking it back across the bottom. On the input/output edge, it'll be a bit hotter on the top and cooler on the bottom, and on the other side it'll be medium hot on both the top and the bottom. On average, it'll be about the same edge to edge if you disregard the top/bottom difference.)
Industrial plastic heaters that work this way can heat up pretty thick plastics in about 30 seconds, without overcooking any part of them.
What I'm thinking of doing is isolating the air-heating component from the oven; it would just be a box that heats air, which is blown into the oven. (Actually, into a "plenum" chamber with a bunch of holes leading into the oven, to spread the airflow out.)
I think this air heating box can be very simple and efficient. You just put any kind of radiant heating element in it---whatever you can find from things at a thrift store---surrounded by several layers of metal screen. The screens will absorb the radiant heat and thermalize it, and you can blow the air through all the hot screens to heat the air. Simple metal screens near the elements will act both as transducers and heat sinks.
If the box is insulated, there is no place for much of the heat to go *except* into the air you're blowing through it, so it has to be pretty efficient. It will eventually stabilize at some temperature where it dumps it heats the air as much as the heating elements are heating it. The only worry is that if the box is too small or the airflow is too low, it could get very, very hot and melt something. (Like the screens or the connectors on the heating elements.)
As for how to actually move the air, I'm thinking that pretty much any appropriate size/speed fan will do; to keep from baking the motor, you put the fan inside a duct and the motor outside, with a long-enough shaft through a little hole in the duct. (You might need a trick or two to keep the shaft from getting hot enough to overheat the motor bearings, like using an insulating and/or heat-sinking segment of some kind.) The right kind of blower & shaft arrangement is probably available off-the-shelf if you know what machine and part number to ask for, but I don't know that...
A quick and dirty version of this wouldn't recycle the hot air. You'd just pump hot air from a heat gun or two into a plenum chamber with holes leading into the input side of the oven chamber. So the whole thing could be two insulated metal boxes with some holes in the right places, and a $10 heat gun or two.
Some of this stuff has been discussed on rcgroups.com in a couple of threads about thermoforming sheet foam plastics like Depron. (IIRC, that's some kind of dense styrene foam.) Somebody who sounded like he knew what he was talking about said that with a good plenum/oven design, a single 1500-watt heat gun should be sufficient to heat a 2 x 3 ft sheet of plastic. I don't know if that's true, but if not I'd guess 2 would do it.
BTW, those model plane guys (and some German folks they talk about) have been doing some very cool stuff thermoforming sheet foams in negative molds. The Depron foam apparently makes its own skin when you vacuum form it, so you end up with something resembling foam core board---thin solid plastic on both sides, which can capture great detail, and foam in the middle. That might be great for some costume applications as well. Unfortunately, Depron foam is hard to get in hobbyist quantities in the U.S.
Apparently you can thermoform the foam core of foamcore board, if you soak it and scrape the paper cladding off. It's some kind of polystyrene foam, too.
Some people also vacuum form craft foam, a.k.a. "Foamies" (brand), which is EVA foam. (One guy on rcgroups uses it to mold helicopter bodies.) I've tried it, and it's very cool. (It's also easy to get in small sizes for experiments, at the craft store or even the dollar store... 12 sheets for a dollar is liberating.)
I've been forming this stuff over life casts...
If I use the 2 mm stuff and bake it at 350 for about a minute and a half or two, it cooks down to something less than a millimeter thick that's more leathery than foamy, and fits like a glove. If I use the 3 mm stuff it doesn't cook down so much, and stays more like craft foam, but also fits like a glove. The 6 mm stuff is very cool, if you want a lot of loss of detail, which sometimes I do, locally smoothing out a shape with a dense rubbery foam, and still fitting like a glove. (Rubber fetishists should love it . )
I'd really like to use that for making thick, smoothed leather-like breastplates / art bras, but so far I've only found the 6 mm stuff in 9 x 12 sheets. (At some craft stores. Almost all craft stores sell the 2 mm stuff, in 9" x 12" and 12" x 18", and many sell 3mm in the 12 x 18 size. But watch out for the metric-sized off-brand 12 x 18s that may not fit your frames... I think whatever Wal-Mart sells as 12 x 18's are a little bigger one way and a little smaller the other.)
I need to hunt up an industrial supplier who will sell me larger sheets and other thicknesses; that should be possible, because various thicknesses of EVA foam are used for a lot of things. (E.g., camping and yoga mats, traction flooring, athletic shoe parts, padding for martial arts, flip-flop sandals.)
One reason I'd like to have a pretty good oven is that I want to experiment with novel materials, like foams and laminations of foams with other plastics.
Speaking of which, does anybody have much experience reinforcing thin plastics with epoxy or something...? If I don't actually come up with a good oven for big stuff and thick plastics, I may resort to making thin castings with a shoddier oven, and reinforcing them on the back side. That's a pain in the ass, but I don't expect to make more than a few of any particularly large thing, so it may be worth it.
One RC model guy I talked to laminates very thin fiberglass cloth to his styrofoam wings by just spraying them with some kind of adhesive, laying the cloth on, and spraying it again with more adhesive. (I wish I could remember what kind of adhesive he used; it wasn't an epoxy.) Very thin fiberglass cloth is available at model shops for surprisingly reasonable prices. (A few bucks for a 3 x 3 foot piece.) That trick might come in handy for reinforcing armor. |
|
Back to top |
|
 |
jegner Site Admin

Joined: 30 May 2003 Posts: 2144 Location: Texas, USA
|
Posted: Tue Sep 05, 2006 2:21 pm Post subject: |
|
|
Sounds like you have an interesting concept. Me, I choose the path of least resistance, and did the NiChrome wires a la Thurston James. Cost was not that much, and was easy and effective. I have considered adding a fan, but I get enough convection with the tapered walls that my plastic heats pretty evenly.
Your idea sounds good, but is more complex, IMHO.
And the notion that a heat gun can heat a 2x3 foot sheet of plastic to forming temp, I would be very surprized. The surface is so large, that even in a well insulated pizza oven, a heat gun would take a very long time to get the air AND plastic hot enough, and would be uneven at best. Some sort of closed space, and enought time, a heat gun might get the air hot enough, but as soon as the hot box was opened, the hot air would escape, and you would have to do the whole thing over again.
The heat guns would not last long under constant use. But these are great for spot heating.
Jim
Last edited by jegner on Tue Sep 05, 2006 2:25 pm; edited 1 time in total |
|
Back to top |
|
 |
drcrash Guru

Joined: 04 Sep 2006 Posts: 705 Location: Austin, Texas
|
Posted: Wed Sep 06, 2006 1:54 am Post subject: convection ovens and heat guns |
|
|
Jim,
I agree that a single heat gun would be lame, especially for a "production" machine, and if used a bunch would wear out the heat gun. For a production system, I'd want to recirculate. Using heat guns would let me prototype the design, though---the air paths would be exactly the same except for the return tube to the heater. (And it would work fine, though wastefully, for the occasional pull of a large piece.) If it doesn't work with the heat guns, it's not going to work with a recirculator either, and I shouldn't bother making the air heater chamber or doing the fan-shaft-through-duct-wall hack.
If my calculations are correct, a 1500 watt heat gun does put out enough heat to heat a 2 x 3 sheet of 2 mm polystyrene from 70 to 250 F in a minute and a half or so. Of course, in an open system, most of the heat is going to blow right out the output tube, not heat the plastic, so it would take several times longer... but I'm thinking two heat guns should do it in reasonable time by my occasional-big-piece standards.
(Once the oven is hot, the fact that most of the heat goes to waste doesn't mean it will heat the plastic more slowly than a closed system; that only depends on the temperature and volume of the airflow over the plastic, not whether it's freshly-heated or recycled. The closed system may save electricity, but not plastic-heating time.)
If the thermal mass of the oven interior is low, comparable to that of the plastic sheet to be heated, it should only take a few minutes to preheat it. A properly designed pure convection oven should be able to heat itself quickly and evenly, as well as doing that to the plastic. I'm thinking of aluminum flashing over fiberglass insulation, so that you basically only have to heat a thin layer of aluminum, and you're ready to go.
How long this would take would mostly be determined by the CFM of the heat gun and the cubic feet of the oven. A 10 CFM heat gun could more or less cycle the air in a 5 cubic foot oven twice in one minute. I'd think another minute or two should warm the system up pretty good.
The trick is keeping the thermal mass really low---the opposite of using Hardibacker board, etc.---and insulating it well. For this kind of system, most of the absorbing and reradiating of IR should happen in the air heater, not the oven.
(Actually the interior of the oven will quickly heat up to the hot air temperature, and will reradiate IR correspondingly. But if it heats evenly, it should reradiate evenly too, and glow evenly in the IR, which is fine.)
The tricky bit is whether the volume of heated air would be high enough with two heat guns.
My impression is that the seriously fast industrial machines pump the air through the oven really fast. A pair of heat guns probably doesn't blow nearly that hard, so the convection would be correspondingly slower. (A heat gun also blows too hot, but you could address both problems somewhat by using a hairdryer or something to blow some less-hot air in there, getting a lower temperature and higher flow, too. Come to think of it, my heat gun and my hair dryer put out about the same amount of heat, but the hair dryer blows a whole lot more air... maybe one heat gun and one hair dryer would be about right.)
If I had a good design in hand---which I don't claim to---I think this would be about as easy to build as anything---basically a couple of insulated thin-metal boxes with some holes between them. The tricky part is in tuning the design, but once that's right it should be scalable and work for large, small, or telescoping boxes.
Making the boxes collapsible would be more complicated, but straightforward, and since I don't have shop space, that really appeals to me.
Paul |
|
Back to top |
|
 |
harley guy Novice
Joined: 25 Nov 2005 Posts: 71
|
Posted: Wed Sep 06, 2006 2:55 pm Post subject: Re: convection ovens and heat guns |
|
|
drcrash wrote: | Jim,
I agree that a single heat gun would be lame, especially for a "production" machine, and if used a bunch would wear out the heat gun. For a production system, I'd want to recirculate. Using heat guns would let me prototype the design, though---the air paths would be exactly the same except for the return tube to the heater. (And it would work fine, though wastefully, for the occasional pull of a large piece.) If it doesn't work with the heat guns, it's not going to work with a recirculator either, and I shouldn't bother making the air heater chamber or doing the fan-shaft-through-duct-wall hack.
If my calculations are correct, a 1500 watt heat gun does put out enough heat to heat a 2 x 3 sheet of 2 mm polystyrene from 70 to 250 F in a minute and a half or so. Of course, in an open system, most of the heat is going to blow right out the output tube, not heat the plastic, so it would take several times longer... but I'm thinking two heat guns should do it in reasonable time by my occasional-big-piece standards.
(Once the oven is hot, the fact that most of the heat goes to waste doesn't mean it will heat the plastic more slowly than a closed system; that only depends on the temperature and volume of the airflow over the plastic, not whether it's freshly-heated or recycled. The closed system may save electricity, but not plastic-heating time.)
If the thermal mass of the oven interior is low, comparable to that of the plastic sheet to be heated, it should only take a few minutes to preheat it. A properly designed pure convection oven should be able to heat itself quickly and evenly, as well as doing that to the plastic. I'm thinking of aluminum flashing over fiberglass insulation, so that you basically only have to heat a thin layer of aluminum, and you're ready to go.
How long this would take would mostly be determined by the CFM of the heat gun and the cubic feet of the oven. A 10 CFM heat gun could more or less cycle the air in a 5 cubic foot oven twice in one minute. I'd think another minute or two should warm the system up pretty good.
The trick is keeping the thermal mass really low---the opposite of using Hardibacker board, etc.---and insulating it well. For this kind of system, most of the absorbing and reradiating of IR should happen in the air heater, not the oven.
(Actually the interior of the oven will quickly heat up to the hot air temperature, and will reradiate IR correspondingly. But if it heats evenly, it should reradiate evenly too, and glow evenly in the IR, which is fine.)
The tricky bit is whether the volume of heated air would be high enough with two heat guns.
My impression is that the seriously fast industrial machines pump the air through the oven really fast. A pair of heat guns probably doesn't blow nearly that hard, so the convection would be correspondingly slower. (A heat gun also blows too hot, but you could address both problems somewhat by using a hairdryer or something to blow some less-hot air in there, getting a lower temperature and higher flow, too. Come to think of it, my heat gun and my hair dryer put out about the same amount of heat, but the hair dryer blows a whole lot more air... maybe one heat gun and one hair dryer would be about right.)
If I had a good design in hand---which I don't claim to---I think this would be about as easy to build as anything---basically a couple of insulated thin-metal boxes with some holes between them. The tricky part is in tuning the design, but once that's right it should be scalable and work for large, small, or telescoping boxes.
Making the boxes collapsible would be more complicated, but straightforward, and since I don't have shop space, that really appeals to me.
Paul |
dr crash.why you trying to re-invent the wheel?the nicro-wire is easy to use.why get all complex with a oven? |
|
Back to top |
|
 |
drcrash Guru

Joined: 04 Sep 2006 Posts: 705 Location: Austin, Texas
|
Posted: Wed Sep 06, 2006 5:35 pm Post subject: |
|
|
why you trying to re-invent the wheel?
I'm a scientist-engineer-inventor type; it's what I do. Usually computer stuff for money, but this seemed interesting to do for fun.
the nicro-wire is easy to use. why get all complex with a oven?
Partly because I like trying different things, and partly because I have different uses for the oven than most people here. (And I think that may make me pretty typical of people who could use a vacuum former.)
It's not clear to me that an oven that's good enough for 1/8" HIPS heats quite evenly enough for heating some other plastics, which are less forgiving.
Also, space is a big issue for me. No shop, no garage, no yard. I just do not have room for a setup like your over-and-under, much less Jim's flip-top. (I passed up a beautiful 2 x 3 foot stainless steel box at the scrap yard today, and thought how it'd make a great oven for a machine like yours...) If I build a big vacuum former, it has to be collapsible and lightweight, so that I can store it compactly, or take it over to a friend's house if I'm going to be using it heavily. My wife wants to be able to take it out and put it up easily if she wants to use it for something; putting a big, heavy oven up on stilts is too much. (Ideally, it could fold up and go on a plane with my wife to a museum where she's doing installation work.)
That all makes convection attractive. I can't afford a lot of heavy metal or backer board to even out the irregularities of IR heating.
Right now, I live in an apartment where I might actually be evicted if I insist on doing this stuff on the balcony, and if I screw up just once and make too much smoke inside, an automatic sprinkler system will go off and make a big expensive mess; I'll be charged thousands of dollars to clean it up. (That happened to my neighbor a few months ago.) So I want something that's safe to use in an apartment. (With the windows open, of course.)
A convection oven would be very reassuring in that regard---it'd be great to know that no matter how much I heat a tricky piece of plastic, it will never scorch and set off the sprinklers, if I keep the air temperature below the plastic's scorching temperature. (And that's easy to measure with a thermometer that costs a few bucks.) That would allow me to form trickier plastics, and avoid some consequences that are way worse than having to replace some gunked-up coils.
I wouldn't bother thinking so much about alternative designs if I didn't think my situation was fairly common, in a general way. Most people who could use a vacuum former aren't going to make it their hobby, or do big production runs, and they won't dedicate much space for the machine most of the time. It's just a pretty cool tool. They're also likely averse to big black clouds of smoke, or just ruining expensive plastic with more trial and error than is really necessary.
I also wouldn't bother if I didn't think the eventual design would likely be fairly simple and easy to make, as well as doing a good job. The point would be an easy-enough-to-make design that makes it easier to do cooler things, without wasting space, time or money. That might turn out to be surprisingly easy. The basic structure is a couple of boxes, and I might find off-the-shelf collapsible or nestable boxes that would do the trick with a little adapting.
[/b] |
|
Back to top |
|
 |
Stomper Master
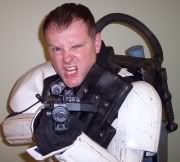
Joined: 01 Oct 2005 Posts: 473 Location: Woodburn, Oregon USA
|
Posted: Wed Sep 06, 2006 9:36 pm Post subject: |
|
|
Hmmm very interesting idea... you could use a draft inducer motor with it's housing from a gas furnace to blow the air. They move a decent amount of CFM, and are designed to be in the hot air stream, and run on 110vac as well. _________________ Tony Krewson
FEAR... is not my god!! |
|
Back to top |
|
 |
drcrash Guru

Joined: 04 Sep 2006 Posts: 705 Location: Austin, Texas
|
Posted: Thu Sep 07, 2006 6:46 am Post subject: draft inducer as blower for convection oven |
|
|
Wow, yes. Those draft inducer things sound great. I didn't know they existed. (I haven't thought much about HVAC systems.) That's the kind of off-the-shelf gadget I was thinking of, without knowing where to look for it it.
So I did some googling... McMaster-Carr & Grainger stock several models, so it's an easy-to-get item if you're willing to pay $60 or more. (If not, it shouldn't be too hard to roll your own.)
Thanks, Tony. Great idea. |
|
Back to top |
|
 |
Stomper Master
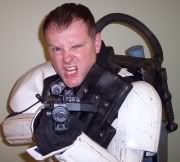
Joined: 01 Oct 2005 Posts: 473 Location: Woodburn, Oregon USA
|
Posted: Thu Sep 07, 2006 8:08 am Post subject: |
|
|
I do commercial heating and A/C, and when you started talking about convection heating and so forth the ol' light bulb lit up over my head , glad I could help! If you decide that is the way you want to go, and can't obtain one for some reason let me know and I can help you out in obtaining one!  _________________ Tony Krewson
FEAR... is not my god!! |
|
Back to top |
|
 |
drcrash Guru

Joined: 04 Sep 2006 Posts: 705 Location: Austin, Texas
|
Posted: Fri Sep 08, 2006 12:12 pm Post subject: crude convection oven prototype |
|
|
So I McGuyvered up a little heat-gun-driven convection oven out of some aluminum foil and spit... actually a couple of large disposable roasting pans sandwiched around a 12 x 18 inch piece of fluorescent ceiling panel styrene. I didn't insulate anything, and just counted on the still air around the roasting pans losing little heat compared to the mad rush of hot air through them.
It took about 4 minutes from a cold start to heat the plastic until it sagged an inch, and another minute until it was sagging 2 1/2, i.e., too much (across a 12-inch span).
That was with the heat gun on high about a third of the time and on low the rest of the time. (Because the plastic smoked when I had it on high.) The whole sheet got soft and sagged, not just a spot. (I wouldn't say it heated the plastic "evenly," though, because I didn't make a good plenum for it---just a crude baffle to disperse the heat gun blast a little.)
This makes me think that a pair of heat guns could heat a 2 x 3 foot sheet of plastic (4x as big) in 10 minutes at most, and maybe in 5 if the air paths are sized right.
Which is not to say that it's a good idea. I was clearly blowing too-hot air into that thing, and heating plastic "too fast." For a good convection oven, you'd want to use more air flow that's less hot, and get fast heating by blowing hot air faster, not blowing really hot air.
I can try that with a heat gun plus a hair dryer, to get a higher volume of less-hot air, but it seems likely that will do more to blow away my hot air than increase the efficiency of convection, so it will heat slowly. I may need recirculation to get good air velocity without having to heat ludicrous amounts of air.
I just realized heat gun might work with a recirculator, though; you don't have to recirculate the air through the heat gun. Just recirculate the air that's already in the oven, continually injecting more "fresh" hot air into the mix with the heat gun, and letting a corresponding amount of old air come out.
If works as well as I think it will, I don't need to build an air-heater box, but I likely will need a draft inducer.
That also makes me think that if you used a draft inducer to circulate the air, you would probably do okay with one heat gun to heat fairly large piece of plastic, and it could be very simple. More than two would be overkill, because the problem isn't heating the air hot enough---it's moving it around fast enough that it transfers that heat to the plastic quickly.
Paul |
|
Back to top |
|
 |
jegner Site Admin

Joined: 30 May 2003 Posts: 2144 Location: Texas, USA
|
Posted: Fri Sep 08, 2006 3:10 pm Post subject: |
|
|
Sounds interesting. I would love to see it done for a 2 foot by 2 foot oven. Dr. Crash, can you post some pics?
Jim |
|
Back to top |
|
 |
drcrash Guru

Joined: 04 Sep 2006 Posts: 705 Location: Austin, Texas
|
Posted: Sat Sep 09, 2006 6:18 pm Post subject: |
|
|
If you decide that is the way you want to go, and can't obtain one for some reason let me know and I can help you out in obtaining one!
I think I'm set. I just scored a variable-speed draft inducer on ebay for $6. (Plus $12 shipping.) But thanks. |
|
Back to top |
|
 |
drcrash Guru

Joined: 04 Sep 2006 Posts: 705 Location: Austin, Texas
|
Posted: Sat Sep 09, 2006 8:55 pm Post subject: |
|
|
Sounds interesting. I would love to see it done for a 2 foot by 2 foot oven. Dr. Crash, can you post some pics?
I took some pictures of the disposable roasting pans and I'll try to get them up and labeled soon.
Meantime, here's a verbal description...
I actually constructed a couple of extra-long roasting pans by taking pairs roasting pans, cutting off one end of each, and overlapping them to make somewhat longer roasting pans. This gave me one roasting pan a couple of inches longer than my plastic-holding frame, and another about three inches longer than that.
I cut a hole in one end of the shorter roasting pan, to stick the heat gun nozzle into.
Then I sandwiched the two roasting pans around the plastic, so that I could blow air through one roasting pan (and across the plastic) and have it go around the far end of the plastic and come back through the other roasting pan. (Which is longer so there'll be a gap at the heat-gun end, too, to let the air escape.)
The two roasting pans (and the plastic in between) give me a U-shaped duct around the plastic, heating it from both sides. (Does that make sense?)
I may try this with a 2 x 2 version. I've scored some 26" (inside) welded aluminum frames of 1 1/2" square aluminum tube, and some flashing, I can make a similar sandwich around the plastic. (Flashing, frame, plastic, frame, flashing.) The frame thickness will provide reasonable air gaps on each side of the plastic. I can blow hot air through one frame, across one side of the plastic, and let it go around the end of the plastic and come back through the other frame.) Maybe I can just clamp that stuff together well enough for a basic test.
That should be enough to tell me whether a heat gun (and maybe a hair dryer) are enough to heat a 2 x 2' piece of plastic. A good convection oven would require a couple of simple enhancements, of course. |
|
Back to top |
|
 |
drcrash Guru

Joined: 04 Sep 2006 Posts: 705 Location: Austin, Texas
|
Posted: Sun Sep 17, 2006 7:30 am Post subject: |
|
|
Quote: | I think I'm set. I just scored a variable-speed draft inducer on ebay for $6. (Plus $12 shipping.) But thanks. |
Maybe I spoke too soon. I'm sitting here with the draft inducer, and I have no idea how to plug it in. The physical mounting and ducting look trivial, but I can't find any technical specs for it, like what temperatures it can actually handle, or the pinout so that I can wire it up. (I expected it to have simple wire leads, like the ones from McMaster, but it has a two-row 12-pin white plastic connector...)
I assumed that the information would be on the web somewhere, but it doesn't seem to be. Oops.
Tony, do HVAC guys like you have access to tech information like I need? (And do you by any chance happen to work with Trane systems? I have a Fasco A190, which is an OEM part/replacement for several Trane blowers; mine has the Trane part # 7000-5833 and "Cust. P/N D341114G01" on it.)
I was surprised to find out that the the centrifugal blower is made of plastic, which makes me wonder if some draft inducers aren't up to the full flue heat, and work in a different way than the ones I have seen temperature specs for. (All of those are good up to around 600 degrees.) Is it going to melt if I run 500-degree oven air through it? Or is it made out of a very high-melting-point plastic? (It should be, for the $300 this one would cost new.) |
|
Back to top |
|
 |
|
|
You cannot post new topics in this forum You cannot reply to topics in this forum You cannot edit your posts in this forum You cannot delete your posts in this forum You cannot vote in polls in this forum
|
Powered by phpBB © 2001, 2005 phpBB Group
|