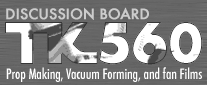 |
www.TK560.com Vacuum Forming, Movie Prop, Sci-fi and GIjOE Forum
|
|


|
View previous topic :: View next topic |
Author |
Message |
mpmurray Newbie
Joined: 24 Nov 2005 Posts: 11
|
Posted: Mon Apr 17, 2006 8:34 pm Post subject: Operation of Check Valve & Supplier of Valve & Guage |
|
|
My current check valve (from Lowe's plumbing section) closes and allows no more vacuum pull for the tank. I'm wondering if the tank vac pressure get so strong that the valve is prevented from opening. Sort of a tug-a-war between pump and tank.
Can I use standard plumbing check valves, or must it be some kind of air check valve?
I suppose I should get a guage too.
Anybody know a supplier of both?
Thanks!
michael |
|
Back to top |
|
 |
crashmann Guru

Joined: 27 Sep 2005 Posts: 501
|
Posted: Tue Apr 18, 2006 1:05 pm Post subject: |
|
|
I was using a garden hose check valve from Home Depot, but it was making way too much noise. Then I installed a ball valve just before the vac pump and changed the operating procedures:
Close the ball valve at the forming table
Open the ball valve at the pump (after the pressure chamber) and turn on the pump
Monitor the gauge and draw down to 25" mercury
Close the ball valve, then turn off the pump
When the plastic is ready, turn on the pump and open the valve
Flip over the plastic, then open the valve at the table
For the gauge, I went to an auto parts store and bought a combo vacuum / pressure gauge. I connected it to the system using a T fitting and reducer connections. I found when you open the valve at the table, the gauge immediately dropped to zero, then after the plastic was drawn down, it would show 4" of vacuum when using the shop vac, or 11" when using the vac pump.
I added a second gauge at the vacuum chamber to accurately monitor the vacuum as I am drawing down the plastic.
McMaster-Carr probably has a better check valve than Home Depot or Lowes. http://www.mcmaster.com Search for check valve. Don't know if you need a specific valve for "air" or "vacuum" applications. However, I found they were a little pricey
For a vacuum gauge, just go to the auto store
Charlie
TI-386 |
|
Back to top |
|
 |
jegner Site Admin

Joined: 30 May 2003 Posts: 2144 Location: Texas, USA
|
Posted: Thu Apr 20, 2006 12:03 pm Post subject: |
|
|
Good info. I really need to carve out some time to finish plumbing my hi-vac.  |
|
Back to top |
|
 |
Mattax Expert
Joined: 09 Mar 2006 Posts: 160 Location: Virginia
|
Posted: Thu Apr 27, 2006 8:19 pm Post subject: |
|
|
Me too! Hopefully, I will have time to sit down next week and finish my oven and plastic frame design and then the necessary fittings and filters. WHEW! So much left to do, yet so close!
I am actually in a holding pattern on finishing my table due to the second shed. It needs to be completed before I can start working on the vac table again. I ran out of room in my first shed once I bought the vac tank and thus the second shed.
Finish wiring, insulate, plywood walls, urethane and finish electrical. _________________ Mattax
TK487
Garrison Tyranus |
|
Back to top |
|
 |
drcrash Guru

Joined: 04 Sep 2006 Posts: 705 Location: Austin, Texas
|
Posted: Wed Oct 11, 2006 10:03 pm Post subject: |
|
|
Quote: | I was using a garden hose check valve from Home Depot, but it was making way too much noise. |
Charlie, when was it making too much noise, and what kind of noise was it making? What kind of check valve were you using? (Maybe a spring & disk bronze valve, or a plastic and rubber flapper PVC valve?)
Was the check valve making noise before opening the valve to the vacuum tank? Or only after?
I'm in the process of plumbing a 2-stage system, and I am not sure about check valves. I have a maybe-too-small ball check valve. (Not to be confused with a ball valve---the ball is free and either gets sucked against one orifice, stopping it up, or tumbles around at the other end of the chamber, not stopping anything up, depending on the direction of airflow.)
I'm wondering if you were using one of the PVC valves with a plastic disk on a rubber flapper/gasket, and it was fluttering when you were just using the shop vac, before opening the vacuum tank valve.
I've been considering using one of those, but maybe the ball check valve would be better. (Not sure. The ball may bounce around, irregularly affecting the airflow, and make a bunch of racket, too.) |
|
Back to top |
|
 |
crashmann Guru

Joined: 27 Sep 2005 Posts: 501
|
Posted: Thu Oct 12, 2006 12:10 am Post subject: |
|
|
I was using a garden hose anti-backflow check valve at the pump exhaust port. It's a bronze body, and I think it's just a rubber gasket inside. As the vac pump was drawing down the pressure, the noise from the valve would get significantly louder, like a classic Volkswagon engine. I suspect the rubber gasket was smacking the inside of the valve and creating the really loud noise.
After removing the check valve and converting to just a ball valve, the pump noise was much more tolerable! Also, I changed the location of the valve to between the tank and the pump.
I'd like to use a real check valve, but there's too many to choose from on McMaster Carr. And I'm afraid of adding noise to the system (it's loud enough as it is!)
Hope that helped
Charlie
TI-386 |
|
Back to top |
|
 |
jegner Site Admin

Joined: 30 May 2003 Posts: 2144 Location: Texas, USA
|
Posted: Thu Oct 12, 2006 7:30 am Post subject: |
|
|
The noise, have you tried putting a styrafoam cooler over the pump and motor, to deaden the sound? |
|
Back to top |
|
 |
drcrash Guru

Joined: 04 Sep 2006 Posts: 705 Location: Austin, Texas
|
Posted: Thu Oct 12, 2006 12:23 pm Post subject: |
|
|
Quote: | The noise, have you tried putting a styrafoam cooler over the pump and motor, to deaden the sound? |
That won't do much. To block sound, you need mass. Except for the highest frequencies, sound goes right through lightweight stuff like styrofoam.
(Styrofoam transmits sound extremely well because it's not just light but very rigid for its weight. People have used it to make speaker cones because, and it works better than tin cans when you do the tin-can-on-a-string mechanical "telephone.")
What you want is a heavy box, which will reflect the sound rather than transmit it, and you want to put a bunch of heavy soft stuff in it to actually absorb the sound.
Maybe an MDF box lined with dense soft stuff.
(Speaker enclosures are often made out of MDF because it's heavy and not entirely rigid, so it transmits sound poorly. They're usually lined with fiberglass stuff that absorbs high frequencies, but is too light to absorb low frequencies.) |
|
Back to top |
|
 |
drcrash Guru

Joined: 04 Sep 2006 Posts: 705 Location: Austin, Texas
|
Posted: Thu Oct 12, 2006 12:32 pm Post subject: |
|
|
Code: | I was using a garden hose anti-backflow check valve at the pump exhaust port. |
Did you mean to say the vacuum port?
(I'm not sure if your picture is "before" or "after" you changed the valve configuration.) |
|
Back to top |
|
 |
jegner Site Admin

Joined: 30 May 2003 Posts: 2144 Location: Texas, USA
|
Posted: Thu Oct 12, 2006 1:25 pm Post subject: |
|
|
I've used styrafoam coolers for 'temporary' boat motor cowlings and they work quite well for deading sound of motors running. |
|
Back to top |
|
 |
drcrash Guru

Joined: 04 Sep 2006 Posts: 705 Location: Austin, Texas
|
Posted: Thu Oct 12, 2006 2:04 pm Post subject: |
|
|
Quote: | I've used styrafoam coolers for 'temporary' boat motor cowlings and they work quite well for deading sound of motors running. |
I'm sure it helps significantly. Almost anything will block some sound, especially high frequencies, which can be the most cutting and annoying part.
But almost anything will work better than a styrofoam cooler, and do a much better job of blocking lower frequencies. A sheet of 1/4" plexiglas, for example, or a box made of anything heavier than styrofoam, with even a thin cork lining.
If you want to lower sound levels a whole bunch of dB, and especially if you want to absorb something besides the high frequencies, you need (a) mass and (b) a soft but dense inner surface. (The thicker the better.)
One thing they sell for industrial noise reduction around things like milling machines is thick vinyl curtains impregnated with tiny lead shot. The mass of the lead keeps the curtain from moving a lot and transmitting the sound to the other side. The soft vinyl absorbs the acoustic energy, rather than just reflecting it. It's not the best sound-reducer available, but it's a pretty good one that's less than an eighth of an inch thick and easy to move around.
I've used a sound pressure level meter on this sort of thing, and mass really is what keeps sound from getting out of the box. A soft, relatively dense lining is what absorbs it while it's bouncing around in there, so that the noise doesn't build up and eventually escape.
It's a common misconception that soft and/or lightweight things are good for soundproofing. Soft things are good for deadening what it sounds like inside the box (or room), but lightweight ones are not as good as dense ones---sound can go right through them, be reflected off a wall, and come back right through them. Massive walls are what keep the sound that isn't immediately absorbed from being conducted outside the box or into the next room.
For example, recording studios---which typically demand sound pressure level drops of many dozens of dB---are typically built with double walls of double-thickness gypsum board, with dense soft stuff on the inside and between the double walls. The sound that isn't absorbed by the first layer of soft stuff has a hard time getting through double-thickness gypsum board, because it can't move something so massive very much. So it bounces around inside the box and gets more chances to be absorbed by the soft stuff.
What does get through may be absorbed by the next layer of soft stuff, but if it isn't, it has a hard time making the next double-thickness layer of gypsum board vibrate and transmit the energy. It will bounce around between the two massive wall layers and get several chances to be absorbed by the soft stuff in between.
If you really want to deaden the sound of a pump a lot, you should do the same kind of thing. Put it in a soft-but-dense-stuff-lined box of something heavy-and-not-too-rigid like MDF or gypsum board, and put that in another soft-but-dense-lined box of something heavy-and-not-too rigid. (With no rigid connections between the inner and outer boxes.)
Unfortunately, once you have one soft-lined box of heavy stuff, you've still got a much bigger problem with the sound coming out of the air intakes and outputs, where you have to have a hole all the way from the inside to the outside.
For that, you want to use baffles. You want to make sure that any path from the inside of the outside of the box has to twist and turn, and be lined with dense soft stuff, so that the air vibrations hit soft dense stuff (backed by heavy stuff) a few times before getting out of the box. The denser the soft stuff is, the better, because almost anything will absorb high frequencies but lightweight stuff isn't good at absorbing lower frequencies, no matter how soft it is. |
|
Back to top |
|
 |
crashmann Guru

Joined: 27 Sep 2005 Posts: 501
|
Posted: Thu Oct 12, 2006 2:50 pm Post subject: |
|
|
The picture is after I made my modifications. The large blurry thing at the bottom right corner is the exhaust filter. I installed the check valve between the exhaust filter and the pump so that when the pump is turned off, the valve would close, and not allow air back into the system.
Good in theory, but not in practice
Without the check valve, the pump makes some noise, but not enough to be heard in the upstairs bedrooms at 2:00am (that's when I do my best work ) I recall a vac table setup axactly like Jim's where the students placed a cardboard box with fiberglass insulation over the pump. The insulation probably did a fine job absorbing the noise, but it probably also held in the heat from running the motor.
When I move to the garage (if it ever gets built) I probably won't be able to do any midnight forming, since my son's new bedroom will be directly overhead
At least I'll have more room to spread out!
Charlie
TI-386 |
|
Back to top |
|
 |
jegner Site Admin

Joined: 30 May 2003 Posts: 2144 Location: Texas, USA
|
Posted: Thu Oct 12, 2006 2:55 pm Post subject: |
|
|
crashmann wrote: | I recall a vac table setup axactly like Jim's where the students placed a cardboard box with fiberglass insulation over the pump.
|
Oh, yea, I remember that one too now that you mention it. I wonder what ever happened to that? |
|
Back to top |
|
 |
drcrash Guru

Joined: 04 Sep 2006 Posts: 705 Location: Austin, Texas
|
Posted: Sun Oct 15, 2006 7:57 am Post subject: |
|
|
Charlie, what size and type of flexible hose is that you're using?
I'm using flexible hoses from the main valve assembly to the 2-stage check valve and to the vacuum tank. Unfortunately, the 1/2" braided PVC tubing I'm using is deforming a bit under sustained vacuum. (1/4" seems to handle it just fine, as I'd expect. I'm not really surprised about the 1/2" deforming; big tubes are much easier to crush than small ones, for the same wall thickness.)
I'm thinking of upgrading to 1/2" high-pressure hose, but while I'm at it I may go to 5/8" or 7/8" "high pressure washer hose."
I discovered that hose barbs have smaller inside diameters than I'd expect. For half-inch ID tube, they're only 3/8 ID. To get 1/2" inside diameter for the hose barb fittings, you need to go to 3/4" ID tube. (Half-inch pipe to 3/4" hose barb fittings do exist at some hardware stores, but apparently not Lowe's or Home Depot.)
I haven't found 3/4" tube that looks like it can handle full vacuum, but the 5/8" high-pressure washer hose at Lowe's seems like it probably would; maybe the 7/8" too.
(I seem to recall that you said you have a full 1" pipe from the tank to the platen, so I guess the hose in the picture isn't a bottleneck. Is your 1" pipe flexible or rigid?) |
|
Back to top |
|
 |
crashmann Guru

Joined: 27 Sep 2005 Posts: 501
|
Posted: Sun Oct 15, 2006 7:53 pm Post subject: |
|
|
I'm using the 5/8" high pressure washer hose. It was able to survive the pinch test between my thumb and forefinger, so I figured it wouldn't crush under vacuum. I wanted to find larger diameter, but it just wasn't available at the hardware stores. Then I found McMaster Carr, and they carry a boatload of vacuum hose in enormous diameters!
The trouble is finding fittings to accomodate the enormous hose. If you go with 1" or larger, then you're committed to ordering everything from McMaster.
Since I only had 5/8" hose, I was able to use the plumbing available at Home Depot. I found some hose barbs that allowed me to connect to the threaded ends of the steel plumbing. However, they did not swivel, and the hose got all twisted up when I was attaching it. So I went with 3/4" quick disconnect units from McMaster. They're rather expensive at $30.00 for a set (6534K97 and 6534K39) but since I prefer to take the vac table outside when the weather cooperates, they were exactly what I needed. There was a lot of wrestling to work the 5/8" hose onto a 3/4" barb, but some Windex lubricated it just enough
The metal parts of my plumbing are 3/4" galvanized steel, including the ball valves. If there's any bottlenecks in the system, it's probably in the ball valve.
I also get a fair amount of leakage between the platen and the plastic. So when I'm forming, I first turn on the vac pump, open the valve at the pump, flip the plastic and open the valve at the platen. By having the pump running, that helps compensate for any leakage, and I'm not limited by the volume in the vacuum tank (although 60 gallons plus 30' of 3/4" hose is a lot of volume!)
Charlie
TI-386 |
|
Back to top |
|
 |
|
|
You cannot post new topics in this forum You cannot reply to topics in this forum You cannot edit your posts in this forum You cannot delete your posts in this forum You cannot vote in polls in this forum
|
Powered by phpBB © 2001, 2005 phpBB Group
|