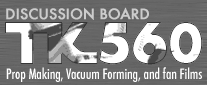 |
www.TK560.com Vacuum Forming, Movie Prop, Sci-fi and GIjOE Forum
|
|


|
View previous topic :: View next topic |
Author |
Message |
cod Master
Joined: 05 Nov 2006 Posts: 322 Location: San Francisco
|
Posted: Fri Nov 10, 2006 12:37 pm Post subject: wiring oven questions |
|
|
I'm wiring up an oven and having trouble finding an extension cord that can handle 20 amps.(romex is stiff and inappropriate?) Also, I might use this at a home occasionally and would like it to be a little more flexible, so I'd like to divide my circuit into two seprate circuits, each carrying around 10 amps. This seems like it might be better distribution for older homes/hillbilly wiring. I'm using the oven calculator to find a coiled length for each of the 2 circuits and coming up with:
2400watts/2 = 1200 watts percircuit
10.45 amps per circuit
coiled length 33"
my rationale is that then a heavy duty extension cord can be used on each circuit, as well as switches, dimmers that are not exorbitantly expensive. Also a dimmer on an outer ring and a dimmer on an inner ring might allow for more control. Is this outlandish? Should I just make one circuit that hits about 20 amps and forget about all this ? Seems like 20 amps in one circuit is borderline to blowing a fuse/staring a fire. .... and I'd like to use dimmer(s) (and its hard to find a cheap one that is over 400 watts)
c.o'd |
|
Back to top |
|
 |
jegner Site Admin

Joined: 30 May 2003 Posts: 2144 Location: Texas, USA
|
Posted: Fri Nov 10, 2006 1:55 pm Post subject: |
|
|
Welcome to the board Chris.
I used 10 ga. Romex wiring for my extension chord, but to be honest, I agree, a more flexible option would be more professional. Talk to an electrician, and ask for the gauge wire needed to carry the load. Then make your own chord. The wire is sold by the foot at the hardware stores. There might even be a guide as to load ratings at the stores.
Finding an off-the-shelf chord is almost impossible. The lone exception are those chords used for RVs.
Jim |
|
Back to top |
|
 |
crashmann Guru

Joined: 27 Sep 2005 Posts: 501
|
Posted: Fri Nov 10, 2006 9:40 pm Post subject: |
|
|
Hi Cod!
(Please excuse me while I giggle at your screen name. Below Darth Vader's belt, he wears a ____ piece )
On my table, I used a 25' 12 gauge extension cord and draw a full 20 amps through it. After running the oven for a while, the outer jacket does feel warm, so there is resistance in the cord and energy is being lost. Most homes do not have a dedicated 20 amp outlet, so you would have more flexibility (and bring your rig to a friend's home) if you designed your oven for two separate 15 amp circuits.
I was hoping to find a chart that would list recommended gauge wire and length versus the load, but Google disappointed me...
So instead, I searched for 20 amp extension cords, and the products that came back all used 12 gauge wiring with a maximum distance of 75' When you get to the 100' 12 gauge extension cords, they are only rated for 15 amps.
Remember, you are adding resistance to the circuit with the extension cord, so the shorter you can make it, the smaller your loss.
If you go with two separate circuits, each with a 25' 12 gauge extension cord, you should not have to worry about tripping 15 amp circuit breakers.
Like you said, the hardest part is finding dimmer switches rated for higher than 400 watts!
Good luck with your quest, and welcome to the platen!
Charlie |
|
Back to top |
|
 |
cod Master
Joined: 05 Nov 2006 Posts: 322 Location: San Francisco
|
Posted: Mon Nov 13, 2006 11:09 pm Post subject: oven circuit questions |
|
|
thanks for the warm welcome everyone.
So,
I'm adapting the oven calculator to give me numbers for 2 circuits, an outer ring overlapping with an inner ring, but 2 discrete circuits. I will split each into around 1000-1200 watts.
I'm not clear on the nichrome characteristics: If I calculate a given COILED length, I'm all set, right ? Or does resistance change based on how far you stretch it ? Not clear on that . I do note that the manufacturer suggests a minimum of 200% stretch.
How many amps can the nichrome handle? Not sure how many segments I should divide the 2 circuits into , but the calcualtor suggests that that is how one can design current limits for each segment. What is a good target ? Iwas getting numbers between 2-5 amps per segment.
my target is to build around 2 1000 watt dimmers, if i can find them less than 40$!
thanks again |
|
Back to top |
|
 |
drcrash Guru

Joined: 04 Sep 2006 Posts: 705 Location: Austin, Texas
|
Posted: Tue Nov 14, 2006 5:06 am Post subject: |
|
|
I'd probably try to stick reasonably close to the watts/inch of the Thurston James design. Not so much because of worry about burning up the coils if you run it hotter, but because it will change the frequencies of IR emitted by the coils.
(The frequency distribution depends on the temperature, with hotter objects emitting higher frequencies.)
I'm not sure how much difference this really makes. Some people say some frequencies of IR are better than others for heating plastic "efficiently." I'm rather skeptical about that, at least for reflective ovens---if the walls are reflective, the radiation will bounce around until it hits plastic, multiple times if necessary, so the plastic will absorb the lion's share of the IR as long as the walls are less absorptive than the plastic.
On the other hand, the Thurston James design clearly works well and can heat large sheets of plastic with a lot less wattage than most pro machines. If you want to play it safe, you might want to stick pretty close to both the nichrome gauge and the watts/inch of the TJ oven.
You might also want to check into whether a dimmer---even if you can find them rated for enough watts---is the right kind of voltage divider for a resistive heater. I've read somebody saying that it's not, and a resistive heater will blow the triac or SCR circuit in a dimmer long before you hit its rated wattage; that person said that what you want is a variac (autotransformer) like an oven heat controller.
That doesn't make a lot of sense to me, either, because I can't see a big difference between an incandescent light and a resistive IR heater. An incandescent light bulb pretty much is a resistive IR heater---it emits about 4x as much IR as it does visible light---so I'd think the same circuits would work for both. But again, if you want to play it safe, you might want to use a tried and true design, like an actual oven heat control. (You might be able to get that cheap, used, from an appliance repair place.)
A lot of pro machines control the temperature by cycling the elements on and off in a 15 or 20 second cycle. When they're on, they're at full current, and temperature is controlled by what fraction of the cycle they're off.
I do that by hand sometimes, flipping the switch on and off to slow heating.
Some other pro machines change the heat setting by switching from running the elements (or banks of elements) in parallel to running them in series. (If you run two identical elements in series, rather than in parallel, you get a quarter the watts.) This turns the elements mostly-off but keeps them pretty hot. That reduces thermal stress on the elements from the high/low cycling, and helps them heat up very quickly at the beginning of the on cycle. (And if IR frequency really matters much, that may make the "hot" cycle hit the "right" frequency range more of the time.)
If anybody knows of a cheap-and-easy timer gadget that could be used to switch elements on and off (or high to low) in a 15-second cycle, I'd be interested in hearing about it. |
|
Back to top |
|
 |
jegner Site Admin

Joined: 30 May 2003 Posts: 2144 Location: Texas, USA
|
Posted: Tue Nov 14, 2006 7:03 am Post subject: |
|
|
drcrash wrote: |
If anybody knows of a cheap-and-easy timer gadget that could be used to switch elements on and off (or high to low) in a 15-second cycle, I'd be interested in hearing about it. |
Hows about one of the thermostats from the indoor electric grills? It cycles on and off depending on temp, and is a 110v device.
Jim |
|
Back to top |
|
 |
drcrash Guru

Joined: 04 Sep 2006 Posts: 705 Location: Austin, Texas
|
Posted: Tue Nov 14, 2006 8:42 am Post subject: |
|
|
Quote: | Hows about one of the thermostats from the indoor electric grills? It cycles on and off depending on temp, and is a 110v device.
|
I tried using the thermostat that came with the little Sunbeam grill, and it didn't seem to work very well. It let the temperature vary by 20 or 30 degrees before switching on or off. (And occasionally 40.) It would switch off for a minute or so at a time, just when the plastic was almost ready. IIRC, that was with the temperature setting all the way up.
It might have worked better if I'd moved it lower in the oven, rather than leaving it attached to the grill element. In the over-and-under, with the grill inverted, there may just be too much accumulating hot air there, and it may not be a good indicator of the temperature at the plastic.
At the moment, I don't really know what the issues are in oven thermostats. (Is it normal for the temperature to vary that much, or is this just a really crummy thermostat? Where should I place the probe?)
I'm willing to watch the thermometer and turn the heat up or down now and then---sometimes I want to do that, anyway, to heat the plastic quickly at first, but slow down to avoid burning it once it gets pretty hot---but sitting and flipping a switch every 20 seconds is really tedious.
I think a plain power control would be fine for my purposes, but a good thermostat would be more convenient; a bad thermostat just gets in the way.
BTW, my understanding is that the heat controls for a surface burner on a stove are called "infinite switches" in appliance repair lingo, even though they're not switches but voltage dividers similar to dimmers. (Anybody who knows, please correct me if I'm wrong.)
Another question I have is whether an stove heat control or oven thermostat for a 230 volt oven would work with 115 volts. (It may be easier to find higher voltage ones cheap, maybe free from junked stoves.) It seems reasonably likely that the main part (a voltage divider of some kind) would work fine at a lower voltage, but I don't really know.
One cheap place to get low-wattage heat controls would be from 2-burner electric "hot plates." (That's not the right name, but people call them that.) You can find those for $20 new, and cheaper at thrift shops. I think the infinite switches are rated at something like 600 to 700 watts, which would be just enough for a four-segment Thurston James oven where each 600-watt segment gets its own infinite switch. |
|
Back to top |
|
 |
Stomper Master
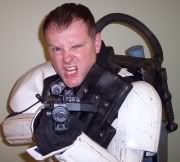
Joined: 01 Oct 2005 Posts: 473 Location: Woodburn, Oregon USA
|
Posted: Tue Nov 14, 2006 4:53 pm Post subject: |
|
|
Over the years my father (runs the electric shop for The Oregonian newspaper) taught me this basic "rule of thumb" for the appropriate wire sizes.
This is for copper wire, go one size up for aluminum wire.
14-AWG = 15 amps
12-AWG = 20 amps
10-AWG = 30 amps
08-AWG = 40 amps
06-AWG = 50 amps
Any larger than that you start getting into needing SE cable, where each of the conductors are about as big around as your pinky to larger than your wrist, depending on the circuit ampacity.
You could get heavy duty rated, rubber jacketed, flexible extension cords that are used for welders at a welding supply store, or an electrical supply house... I THINK Home Depot or Lowe's carries this stuff too... but be warned it's spendy because copper prices are outrageous ATM!! _________________ Tony Krewson
FEAR... is not my god!! |
|
Back to top |
|
 |
cod Master
Joined: 05 Nov 2006 Posts: 322 Location: San Francisco
|
Posted: Tue Nov 14, 2006 5:34 pm Post subject: oven wiring |
|
|
ah, yeah , I figured therr might be a kink in the works, re: a dimmer working on it. It doesnt reeally add up though. Isnt the filament in a light bulb basically the same thing ? It's not as if ther is a bigger surge of power for the dimmer to handle ?
Also, wah are people's power bills like, working with these ovens ? I'm in the most expensive area in the country, and in an industrial space. I want my partner to know waht he's getting into with allowing me to use the shop for this kind of draw.
SO, yes, I aggree with the Thruston James designs being tried and true. A couple of defintie mods though:
a) My over/under design is a strict 24", not expanding out to 28"
b) my goal is to nearly equal the power/inch, just distribute the load to have alittle headroom.
thanks ofr all the info, guys. |
|
Back to top |
|
 |
jegner Site Admin

Joined: 30 May 2003 Posts: 2144 Location: Texas, USA
|
Posted: Tue Nov 14, 2006 5:45 pm Post subject: |
|
|
The corners are the real issue with the ovens, as you have to get them hot at about the same rate the center gets, and thats a real trick. The 28 inch base for a 24 inch top on the oven is one way to do this, and is suggested. That extra circuit on the outer rim really makes it work.
I agree with Dr. Crash, the thermostat found in the Sunbeam grill is problematic, at least in it's stock config. I was thinking more about toaster oven controls.
hmmm |
|
Back to top |
|
 |
Stomper Master
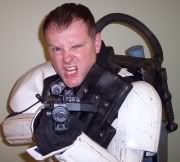
Joined: 01 Oct 2005 Posts: 473 Location: Woodburn, Oregon USA
|
Posted: Tue Nov 14, 2006 5:51 pm Post subject: |
|
|
Methinks I'm going to use a fancy adjustable HVAC control that's used in commercial rooftop units to cut out gas burners at a certain temperature, that is WHEN I get around to building my dang table!
(This may have been stated before) What kind of maintained maximum temperature do you experienced fellas recommend for heating up styrene, and/or ABS?  _________________ Tony Krewson
FEAR... is not my god!! |
|
Back to top |
|
 |
cod Master
Joined: 05 Nov 2006 Posts: 322 Location: San Francisco
|
Posted: Tue Nov 14, 2006 6:13 pm Post subject: |
|
|
My approach to this would be to have one circuit spiral evenly from center to edge, then second circuit spiral from halfway between center and edge, to outer edge. The end result is that there is more nichrome coverage on the outer real estate.
the 28 inch/24 inch design seems moot for over/under ? It would be upside down ?
Quote: | The corners are the real issue with the ovens, as you have to get them hot at about the same rate the center gets, and thats a real trick. The 28 inch base for a 24 inch top on the oven is one way to do this, and is suggested. That extra circuit on the outer rim really makes it work.
I agree with Dr. Crash, the thermostat found in the Sunbeam grill is problematic, at least in it's stock config. I was thinking more about toaster oven controls. |
|
|
Back to top |
|
 |
drcrash Guru

Joined: 04 Sep 2006 Posts: 705 Location: Austin, Texas
|
Posted: Tue Nov 14, 2006 8:33 pm Post subject: |
|
|
I read up on infinite switches, like for stove-top burners, and it turns out they are indeed switches, not voltage dividers like variacs or triacs or SCR's. They actually turn the element on and off to vary the heat.
They aren't thermostats, though, in the sense that they measure the temperature of what they're heating. Instead, they have a bimetal strip inside them, which they run the current through. When it gets hot, it warps and breaks the contact. (It warps because its made of two pieces of metal side by side, and one kind of metal expands more when it's heated.)
That acts to measure the current---the more current going through the bimetal strip, the sooner it warps enough to break contact.
This makes me less optimistic that a 230 V infinite switch would work with a 115 V oven... although maybe what matters is the amps, not the volts per se, so I'm not really sure. |
|
Back to top |
|
 |
drcrash Guru

Joined: 04 Sep 2006 Posts: 705 Location: Austin, Texas
|
Posted: Tue Nov 14, 2006 8:48 pm Post subject: |
|
|
Quote: | My approach to this would be to have one circuit spiral evenly from center to edge, then second circuit spiral from halfway between center and edge, to outer edge. The end result is that there is more nichrome coverage on the outer real estate. |
I would think that you'd want increasing watt density toward the very edge, and the very corners, not just more in the outer half. The outer half of the outer half probably needs more heat than the inner half of the outer half.
I've never seen any good data about this, though---exactly what kind of heat distribution you need, and what you need it for.
(It'd be great if somebody took a thermal imager to one of these machines, and showed just what kind of temperature distribution you get from different IR distributions. Or they could use a touchless IR thermometer and a lot of patience.)
One reason for extra heat at the very edge of the plastic is that the clamping frames conduct heat away. Big pro machines often have heating elements in the clamping frames to keep them at about the right temperature.
I think the bigger reason is that convective cooling affects the edges and corners a lot more than the middle. My understanding is that for flip-flop ovens with no lid on, it affects the edges and corners a whole lot more, because you'll get an updraft over the middle of the plastic, pulling fresh air in at the edges. It's not as clear to me what happens with over-and-unders.
Quote: | the 28 inch/24 inch design seems moot for over/under ? It would be upside down ? |
I wouldn't say it's moot, but I'd guess you'd be better off with straight shiny sides. The straight shiny sides do much the same thing as the flared out design. The flared-out design puts actual heating elements past the edge of the plastic, so that the edge of the plastic is heated from both sides (toward the center and away from the center), like the middle of the plastic. The shiny straight sides get the same effect---and I suspect, do it better---by using reflections to make "virtual" heating elements that extend way past the edge of the plastic. |
|
Back to top |
|
 |
jegner Site Admin

Joined: 30 May 2003 Posts: 2144 Location: Texas, USA
|
Posted: Tue Nov 14, 2006 10:18 pm Post subject: |
|
|
I agree, if I were to make a 24 inch holding frame size over/under oven, I would make it larger than the 24 inc frame, just so I had adequate heat applied to that problematic outer edge. Straight walls for sure, and to make it deeper than the flip-flop oven, just so the plastic can go up into the oven just a tad. |
|
Back to top |
|
 |
|
|
You cannot post new topics in this forum You cannot reply to topics in this forum You cannot edit your posts in this forum You cannot delete your posts in this forum You cannot vote in polls in this forum
|
Powered by phpBB © 2001, 2005 phpBB Group
|