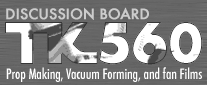 |
www.TK560.com Vacuum Forming, Movie Prop, Sci-fi and GIjOE Forum
|
|


|
View previous topic :: View next topic |
Author |
Message |
cod Master
Joined: 05 Nov 2006 Posts: 322 Location: San Francisco
|
Posted: Sat Mar 24, 2007 8:11 pm Post subject: ebay 'big iron', also I got a tank today |
|
|
I got a water heater,50 gals. Unwrapping now.
Here's some stuff on ebay that is of interest to me:
http://tinyurl.com/2jwzdg
that is essentially the design Ive been striving for, minus the over-under heating. My girlfriend was exactly right. I need a lower heating element, or at least maximum reflection back to the plastic.
I'm interested in how far you can take reflection for underside heating in an over/under. How about a big, aluminum wok cover underneath ?, like a giant parabolic dish! It would probably burn a hole right thru the middle, catch on fire.
I've been experimenting with weights/chains, ultimate portability(lots of this ebay stuff is just too 'industrial' in scale for me, complete with asbestosy-looking wiring and residues.
another!:
http://tinyurl.com/2lhlsb
warehouse-sized room not included. some intersting design ideas in these photos. _________________ <.o'> |
|
Back to top |
|
 |
jegner Site Admin

Joined: 30 May 2003 Posts: 2144 Location: Texas, USA
|
Posted: Sun Mar 25, 2007 6:19 pm Post subject: |
|
|
WOW, those are pretty cool machines! I wish I had an old airplane hangar to store it in! LOL.
4x4 foot forming area, now thats what I'm talking about!
Jim |
|
Back to top |
|
 |
jzawacki Novice
Joined: 12 Jan 2007 Posts: 70 Location: Illinois
|
Posted: Sun Mar 25, 2007 9:46 pm Post subject: |
|
|
Why would you need a 4' x 4' area? That just seem so huge. $2 - 3k doesn't seem that bad if you really need an industrial type machine.. Good to know if I end up wearing out my over/under that i'm working on. |
|
Back to top |
|
 |
drcrash Guru

Joined: 04 Sep 2006 Posts: 705 Location: Austin, Texas
|
Posted: Mon Apr 02, 2007 5:26 pm Post subject: Re: ebay 'big iron', also I got a tank today |
|
|
cod wrote: | My girlfriend was exactly right. I need a lower heating element, or at least maximum reflection back to the plastic.
|
What are you trying to accomplish? (I may have missed something.) Do you have reflective side walls?
My impression is that single-sided heating usually works fine for plastics up to about 1/8" to 1/4". Beyond that (depending on various variables) you want double-sided heating.
I've recently been using my 2-burner hotplate bottom-heater oven (made of roasting pans sitting on the hot plate) for "double-sided" heating by the simple expedient of flipping the plastic over every minute (at first) or 30 seconds. (This has the disadvantage of disturbing the air a lot, which probably gives me colder corners than when I just let thin plastic sit over it.)
I've vacuum formed 1/4" Sintra-type stuff that way, and 8mm EVA foam, and it seems to work fine. (I haven't stressed the corners yet, though---the stuff I'm making doesn't extend into the corners.)
I'm intending to modify my little electric grill over-and-under to let me use it as a kind of rotisserie oven---making the oven deeper, with longer reflective side walls, and having handles that stick out through slots in the walls, so that I can turn the plastic over now and then, without taking the plastic out or opening it up. I suspect that'll be about as good as actual double-sided heating, and easier to build. _________________ Paul (a.k.a. Dr. Crash)
Tired of buying cheap plastic crap? Now you can make your own! www.VacuumFormerPlans.com |
|
Back to top |
|
 |
cod Master
Joined: 05 Nov 2006 Posts: 322 Location: San Francisco
|
Posted: Mon Apr 02, 2007 6:53 pm Post subject: Re: ebay 'big iron', also I got a tank today |
|
|
drcrash wrote: | cod wrote: | My girlfriend was exactly right. I need a lower heating element, or at least maximum reflection back to the plastic.
|
What are you trying to accomplish? (I may have missed something.) Do you have reflective side walls?
My impression is that single-sided heating usually works fine for plastics up to about 1/8" to 1/4". Beyond that (depending on various variables) you want double-sided heating.
. |
I'm trying for an 1/8" 2x2 sheet of petg with about 6 inch draw. I'm not actually going to think about lower heating until I get some good aluminum lined walls and try that first. I had reflectiive side walls that were essentially aluminum covered bubble wrap, but they can't take too much heat. Now I'm going to try aluminum foil glued to wood or steel (cheaper than aluminum). I just replaced the platen with an aluminum sheet. That should add a tiny bit of reflection.
I've done about 8 test pulls and I was never able to get a good seal because the plastic wouldn't complete the full draw. I'm not sure if it cooled too fast, or it just never got hot enough. I've also added a 50 gallon hi-vac system, so that should be a huge difference.
I think some better walls will help, not just for reflection, but trapping heat also. And some heavier counter-weight for my pulley system. The industrial machines I've studied lately have the air piston as leverage, forcing the plastic into the draw. My approach is to hoist the frame up with added counter-balanced weights and pulleys, and then drop . _________________ <.o'> |
|
Back to top |
|
 |
drcrash Guru

Joined: 04 Sep 2006 Posts: 705 Location: Austin, Texas
|
Posted: Mon Apr 02, 2007 8:07 pm Post subject: Re: ebay 'big iron', also I got a tank today |
|
|
cod wrote: |
I'm trying for an 1/8" 2x2 sheet of petg with about 6 inch draw. I'm not actually going to think about lower heating until I get some good aluminum lined walls and try that first. I had reflectiive side walls that were essentially aluminum covered bubble wrap, but they can't take too much heat. Now I'm going to try aluminum foil glued to wood or steel (cheaper than aluminum). I just replaced the platen with an aluminum sheet. That should add a tiny bit of reflection.
|
I strongly recommend aluminum flashing for the walls. It's cheap and stays pretty flat. You don't need to glue it to anything---and if you do, you should have some kind of spacer. If you glue the aluminum (foil or whatever) to something that doesn't like heat, it will conduct whatever heat it absorbs to whatever you glue it to---and the glue. An airspace between the aluminum and whatever's supporting it is a good idea, and bolts or screws are a better idea for attaching it than glue. (But for vertical walls, flashing probably doesn't need support... if you bend it into a box, and support it at the bottom or suspend it from the top, it will be fine.) Flashing is thick enough to stay flat over several unsupported inches, or even a fairly big box if you bend or roll the edges to make it more rigid, so it's WAY better than foil. (And it only costs tens of cents per square foot in the roofing section of the home improvement store. Tin snips do a fine job cutting it.)
Quote: | I've done about 8 test pulls and I was never able to get a good seal because the plastic wouldn't complete the full draw. |
Do you mean that you couldn't stretch the plastic over the buck, and get the frame to meet the gasket? (Or the plastic to meet the edge of the platen---not sure what kind of edge sealing you're doing...?)
Quote: | I'm not sure if it cooled too fast, or it just never got hot enough. |
If you're using 1/8" plastic, and not taking very long to pull it down over the buck, and the buck is not very tall/steep sided, I'd guess you didn't get it hot enough. 1/8" isn't too much for single-sided heating, PETG is one of the easiest plastics to form once hot, and 1/8" should be no problem to stretch over a normal buck, all other things being equal. You will need to apply some modest force to stretch it, but it should stretch fine when you do---and should suck in well under vacuum, too. There's nothing easier to form than PETG, and 1/8" is very doable.
Quote: | I think some better walls will help, not just for reflection, but trapping heat also. |
Do you mean keeping hot air contained, as well as keeping IR reflecting around inside until it hits the plastic? If so, I agree---deep sidewalls do both.
I haven't done thick PETG, but I have done some 1/8" clear acrylic, which pretty clearly lets a lot of IR right through---if you turn the oven on, and put your hand under the plastic (in my over and under) you can feel the IR coming through the plastic and hitting your hand. I don't know what fraction of the IR passes right through the plastic, but it's clearly some significant percentage.
If you put some flat aluminum under it, you shoudl be able to reflect the IR back up and to/through the plastic again, and get some degree of double-sided heating effect. (I use a big aluminum cookie sheet for that, on my little electric grill over and under.)
(I suspect you're clued into this... but I'm spelling it out for anybody who isn't.)
I can't say how effective that will be for you---how much of the IR goes through the plastic the first time depends on the type of plastic and the temperature of the heating elements. However much gets through the first time, most of it will be reflected back up by a flat aluminum reflector.
(A "bad" heating-element temperature for heating plastic may actually be good, in this kind of setup---instead of all being absorbed in the first millimeter of plastic, it may penetrate deeper into the plastic, on average, or go right through, be reflected off your bottom reflector, and then be absorbed near the far side, going the other way---or reflect back and forth any number of times before being absorbed at random depths. That may heat the plastic more evenly, like a microwave oven heating stuff with water and fat in it.)
Quote: | And some heavier counter-weight for my pulley system. The industrial machines I've studied lately have the air piston as leverage, forcing the plastic into the draw. My approach is to hoist the frame up with added counter-balanced weights and pulleys, and then drop . |
I'm not clear on what you're saying there. Do the "added counter-balanced weights" make it neutral, or increase the downward force when you pull it down? Can you pull down hard on the plastic---say, as hard as if you had one hand on each side of the frame, and leaned into it? I suspect that amount of force would be enough for properly heated 1/8" PETG, but I'm not sure if your rig delivers it. Something on the order of a few tens of pounds should be plenty for a 2 x 2 foot piece of 1/8" PETG.
The important thing is that you should be able to apply a few tens of pounds of force pulling the plastic down, and have it fairly evenly distributed, with the plasic coming pretty much straight down at least when it approaches the platen. Various pulley and/or lever systems should be able to do that, but I'm not sure if yours does. _________________ Paul (a.k.a. Dr. Crash)
Tired of buying cheap plastic crap? Now you can make your own! www.VacuumFormerPlans.com |
|
Back to top |
|
 |
cod Master
Joined: 05 Nov 2006 Posts: 322 Location: San Francisco
|
Posted: Mon Apr 02, 2007 9:30 pm Post subject: |
|
|
I cant handle the url coding above to reply, so bear with me.
Quote: | Do you mean that you couldn't stretch the plastic over the buck, and get the frame to meet the gasket? (Or the plastic to meet the edge of the platen---not sure what kind of edge sealing you're doing...?)
|
yep. couldnt stretch it over the buck. one time I stretched it too far. my edge sealing at this juncture is just a completely flat aluminum table. one hole in middle. I bought some rubber tubing to experiment with gaskets, but I may skip that. i would like to make a gasket out of silicone; either tube, strip, or mold.
----"If you're using 1/8" plastic, and not taking very long to pull it down over the buck, and the buck is not very tall/steep sided,"
It is a steep mold. I'd like to go as far as possible with mold depth - up to 12" . This is probably where pneumatics would come in, and good buck/mold design.
Instead of air pressure, I'm working with hoisting the frame up with weights attached underneath, so that it comes down with some force.
My pulley system is in re-build mode right now. The one pro machine I saw recently on ebay (the one that started this thread) is my goal
http://tinyurl.com/2jwzdg _________________ <.o'> |
|
Back to top |
|
 |
drcrash Guru

Joined: 04 Sep 2006 Posts: 705 Location: Austin, Texas
|
Posted: Mon Apr 02, 2007 10:20 pm Post subject: |
|
|
Quote: | Quote: | "If you're using 1/8" plastic, and not taking very long to pull it down over the buck, and the buck is not very tall/steep sided," |
It is a steep mold. I'd like to go as far as possible with mold depth - up to 12" . This is probably where pneumatics would come in, and good buck/mold design.
Instead of air pressure, I'm working with hoisting the frame up with weights attached underneath, so that it comes down with some force.
|
Could you be more specific? Depending on the shape of the buck, 12" shouldn't be a problem, or might be a big problem for forming in general, but either way I don't think that it should be particularly a problem for stretching 1/8" PETG down to the platen, with the right levers or pulleys.
Have you looked at Doug Walsh's lever system for the Proto Form machine? That's simple and I think it should work fine---two levers, two pivots, and a vertical guide on each side. It might be better to go that route than to come up with an original pulley system. (Though that's an interesting design problem.) It's hard to imagine anything simpler that does the trick.
My understanding is that Walsh's levers are fine for a machine up to about 2 x 4 feet... what size are you building?
Quote: | My pulley system is in re-build mode right now. The one pro machine I saw recently on ebay (the one that started this thread) is my goal |
Hmmm... anything in particular about that machine that you like? (If they spent $25,000 on building it as they say, they spent about an order of magnitude more than they should have. There's no way it should cost nearly that much.) _________________ Paul (a.k.a. Dr. Crash)
Tired of buying cheap plastic crap? Now you can make your own! www.VacuumFormerPlans.com |
|
Back to top |
|
 |
jegner Site Admin

Joined: 30 May 2003 Posts: 2144 Location: Texas, USA
|
Posted: Tue Apr 03, 2007 6:21 am Post subject: |
|
|
Cod, is your machine an over-under? Just curious.
Jim |
|
Back to top |
|
 |
cod Master
Joined: 05 Nov 2006 Posts: 322 Location: San Francisco
|
Posted: Tue Apr 03, 2007 2:41 pm Post subject: |
|
|
My machine is an over-under, yes. I have the Doug Walsh book somewhere, but I can't remember what I gleaned from it, or what his design was like. If it's not an over/under style it's not useful to me. I seem to remember the clamping system the Dr.. describes(some sort of expanding /compressing 'x' design ..... , but I'll have to dig up that book.
I found the Doug Walsh design for frame raising the platen. It looks effective, but I don't think it would be any easier to build than my pulley/weight approach. Another factor is portability, where I think the pulley system would be lighter (assuming the counterweights are diisposable) and maybe designable to disassemble for low profile storage. I guess I'll find out whenn I get there. maybe I just like pulleys and aircraft wire
Its apples and oranges as far as I can see.
My girlfirend says the same thing though : 'Why re-invent the wheel everytime you try something'
but since Walsh's plans aren't free ..... _________________ <.o'>
Last edited by cod on Tue Apr 03, 2007 2:53 pm; edited 1 time in total |
|
Back to top |
|
 |
drcrash Guru

Joined: 04 Sep 2006 Posts: 705 Location: Austin, Texas
|
Posted: Tue Apr 03, 2007 2:45 pm Post subject: |
|
|
cod wrote: | My machine is an over-under, yes. I have the Doug Walsh book somewhere, but I can't remeber what I gleaned from it, or what his design was like. If it's not an over/under style it's not useful to me. I seem to remember the clamping system the Dr.. describes(some sort of expanding /compressing 'x' design ..... , but I'll have to dig up that book.
My girlfirend says the same thing: 'Why re-invent the wheel everytime you try something'  |
Doug Walsh's over-under design isn't in his book... he sells plans for it. (For a 2x2, 2x3, or 2x4 machine.) The lever design is simple, though, and fairly obvious from pictures of his Proto Form machine.
There are several threads discussing it here. You might search for "drop-down frame," "over and under," "throw," and maybe "lift bar." _________________ Paul (a.k.a. Dr. Crash)
Tired of buying cheap plastic crap? Now you can make your own! www.VacuumFormerPlans.com |
|
Back to top |
|
 |
cod Master
Joined: 05 Nov 2006 Posts: 322 Location: San Francisco
|
Posted: Tue Apr 03, 2007 3:02 pm Post subject: |
|
|
what kind of travel distance does this give? my oven can be mounted anywhere along the slotted legs I'm using , but I may have to keep it close to where it is now, which is prolly 3 ft or so. The Walsh mechanism looks like it would be limited to slightly less than the length of its components.
So, if my platen is 2x2, then the 'legs' of the Walsh thing would be around 2ft... pulling it up would yield a reach limiterd by the length of that leg ?
I dunno, maybe its a non-issue.
It does look like you could get a lot of leverage out of the Walsh thing.
The two guide tubes should be smooth (chrome?) metal ? And the guide tubes would guide the frame with some sort of lubricated steel or nylon contact ? hmm
just sussing out the parts here. _________________ <.o'> |
|
Back to top |
|
 |
drcrash Guru

Joined: 04 Sep 2006 Posts: 705 Location: Austin, Texas
|
Posted: Tue Apr 03, 2007 3:50 pm Post subject: |
|
|
cod wrote: | what kind of travel distance does this give?
|
Check out this thread, where I give some basic principles and example geometries:
http://www.tk560.com/phpBB2/viewtopic.php?t=356&highlight=leverage+throw
Unfortunately, I never got around to figuring out how to calculate the leverage issues.
I may just build a little sliders-and-levers system for my little over-and-under, which would let me bring the plastic down with one hand and operate valves with the other... I could also use it as a scale model for empirically investigating the leverage issues.
I think the trick to the vertical sliders is in that thread, too. The trick is to have two guides for each vertical sliding bar, displaced vertically enough that the bar can't get far from vertical, so that the "bearings" can't bind. (If you double the distance between the top and bottom guides, you can double the allowable slop in the slider, too.) The shorter the spacing between the guides, the finer the tolerance you need to prevent binding. _________________ Paul (a.k.a. Dr. Crash)
Tired of buying cheap plastic crap? Now you can make your own! www.VacuumFormerPlans.com |
|
Back to top |
|
 |
cod Master
Joined: 05 Nov 2006 Posts: 322 Location: San Francisco
|
Posted: Tue Apr 03, 2007 5:39 pm Post subject: |
|
|
yeah! heh, it's all there from last year!. And the sad part is I had read it , and it made sense to me.
http://i90.photobucket.com/albums/k249/skywords/vacuum/Mvc-337f.jpg
that is a nice design. I'm sold.
Eight pulleys/bearings is contraption-ish.
The production machines don't mess, and have guided pistons, along rails,tight tolerances in trajectory.
But the above photo features a wee bit of welding. I've avoided welding, for the most part with expensive slotted-L steel. I can add more and more, and more, like an Erector Set. Lucky me.
But still, doc. I think you've nailed it. thanks for pointing back to the 'minutes'.
I read on ... _________________ <.o'> |
|
Back to top |
|
 |
cod Master
Joined: 05 Nov 2006 Posts: 322 Location: San Francisco
|
Posted: Tue Apr 03, 2007 6:05 pm Post subject: width of frame |
|
|
But yeah, now I see from the jpgs that the width of the telescoping 'x-handle' assembly is measured by, at least, the length of the draw(plus a bit for leveraged torque-ing).
Mebbe the trick is a 4 (instead of 8 ) contact/bearing assembly, with a lot of counter-weight(counter-weight adds stability?). You could use some sort of cheap tanks/botlles to hold sand (and the sand could double for fire dousing).  _________________ <.o'> |
|
Back to top |
|
 |
|
|
You cannot post new topics in this forum You cannot reply to topics in this forum You cannot edit your posts in this forum You cannot delete your posts in this forum You cannot vote in polls in this forum
|
Powered by phpBB © 2001, 2005 phpBB Group
|