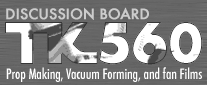 |
www.TK560.com Vacuum Forming, Movie Prop, Sci-fi and GIjOE Forum
|
|


|
View previous topic :: View next topic |
Author |
Message |
jzawacki Novice
Joined: 12 Jan 2007 Posts: 70 Location: Illinois
|
Posted: Tue May 15, 2007 10:23 am Post subject: Multiple frames on one platen? |
|
|
Based off of what DrCrash is saying in this thread, How do you construct different size frames to work on a single size platen? And what is the best material to use for covering the platen holes?
I currently have a 21.5 x 21.5 (or so) size platen designed for my 24 x 24 (or so) size frames to go around. But, when I put together a 9 x 9.5 frame to play with for sale signs, one of the things I learned was that the frames I made were to thick and although the plastic did suck down, it looked horrible.
So, covering the holes in the platen wasn't a problem, but if your frames don't go around the platen, how do you make frames thin enough so that they don't effect the ability of the plastic to be pulled down?
I'm hoping for two types of answers. The "professional" way, and then the "cheap" and dirty way. I liked the feeling of actually doing something real for a change, as apposed to building a vacuum former that just doesn't seem to ever get finished. But I would also like to be able to not waste tons of plastic in the future to do small test pulls. |
|
Back to top |
|
 |
drcrash Guru

Joined: 04 Sep 2006 Posts: 705 Location: Austin, Texas
|
Posted: Tue May 15, 2007 11:02 am Post subject: Re: Multiple frames on one platen? |
|
|
jzawacki wrote: | Based off of what DrCrash is saying in this thread, How do you construct different size frames to work on a single size platen? |
Did you read the section on frames in my draft "Chapter 2"?
http://www.tk560.com/phpBB2/viewtopic.php?t=466
There's a bazillion ways to make frames.
One thing to keep in mind is that the bottom frame does not have to be very rigid, so it can be pretty thin. It only has to be rigid enough to spread the clamping force out halfway to the next clamp. (A little flex is probably a good thing, to make sure that the bottom frame conforms to the top one.)
Most of my frames are made of aluminum windowscreen framing with metal corners, because they're easy to make and cheap, and you can mix and match side lengths to make new sizes on the fly. (For example, I can take the 9-inch sides from my 9 x 12s and the 20-inch sides from my 12 x 20's, and make 9 x 20 inch frames for molding model plane wings.) They're about 1/4" thick.
For big frames, you probably want something stiffer on top, but the bottom frame can be pretty flimsy---as long as you have a binder clip clamp every 4 to 6 inches, you're okay.
If you're using binder clips, you want to make sure that the bottom part of the clip is flat against the bottom of the bottom frame, and the rolled edge of the clamp comes down inside the gasket, rather than on the gasket. (Simple vertical guide rails for lowering the plastic make that easy.) Or you can use C-channnel for the bottom frame, open side outward, and put the bottom of the binder clip inside the C, leaving the bottom of the frame completely flat.
Quote: | And what is the best material to use for covering the platen holes? |
Thin cheap plastic (around 1/32") works fine, in my experience so far. (Like the stuff cheap preprinted GARAGE SALE and FOR RENT signs are made out of.) Hot plastic generally doesn't stick to cold plastic---the surface of the hot plastic immediately chills on contact with the cold plastic, and doesn't stick. (People rely on that for smoothing bucks by vacuum forming a "slipper" layer of plastic over it and leaving it there.)
I might find out otherwise when I go back to forming thick plastics with especially high melting points, with an over-and-under that irradiates the platen more... but in that case I can cover the area inside the gasket with a piece of aluminum windowscreen. (Which I generally do anyway, for other reasons; I'll just have to use a piece that fits more closely, not just under the buck.)
You could use aluminum flashing, which is cheap, but the cut edges of aluminum flashing are dangerously sharp, so I haven't bothered with that... I'd rather use have a piece of screening over a piece of plastic.
Wait a second... I suppose you could just cut away ALL the plastic inside the gasket, and that would solve the problem... you'd probably want to do that for a many-hole platen anyway, to expose as many holes as possible. (Hey, why didn't I think of that before? Doh!)
Quote: | I currently have a 21.5 x 21.5 (or so) size platen designed for my 24 x 24 (or so) size frames to go around. But, when I put together a 9 x 9.5 frame to play with for sale signs, one of the things I learned was that the frames I made were to thick and although the plastic did suck down, it looked horrible.
So, covering the holes in the platen wasn't a problem, but if your frames don't go around the platen, how do you make frames thin enough so that they don't effect the ability of the plastic to be pulled down?
|
What do you mean? Did it not suck down all the way to the platen all around? I generally put my bucks on risers for other reasons, so even if the plastic doesn't quite suck down to the platen where the buck is nearest the gasket, it sucks down far enough not to matter. Thin bottom frames help with that. (Basically, you need a riser as tall as your gasket thickness plus your bottom frame thickness, and you should be good.) _________________ Paul (a.k.a. Dr. Crash)
Tired of buying cheap plastic crap? Now you can make your own! www.VacuumFormerPlans.com |
|
Back to top |
|
 |
crashmann Guru

Joined: 27 Sep 2005 Posts: 501
|
Posted: Tue May 15, 2007 11:21 am Post subject: |
|
|
Hi Doc,
We seem to be following each other around the board today
Could you post some pictures of your flexible sized frames along with your corner guides?
You posted a couple of great ideas - using thin C channel for the bottom frame so that the binder clip sits inside, rather than interfering with sealing to the bottom of the platen. I also like the idea of using a full sheet of plastic to seal the outside holes of the platen. You just cut a window in the middle to match the inside size of your frames. Then you could seal the edges with tape to prevent air from seeping in.
I'm considering making multiple frames from plywood (just cutting a window for the plastic), then using the middle for a single hole platen. The platen would help elevate the mold above the clamping frame, and encourage better forming. Since it's a single hole platen, it could be supported on saw horses, and have a shop vac hose connected underneath.
You've got my wheels turning now!
Charlie
TI-386 |
|
Back to top |
|
 |
drcrash Guru

Joined: 04 Sep 2006 Posts: 705 Location: Austin, Texas
|
Posted: Tue May 15, 2007 12:05 pm Post subject: |
|
|
crashmann wrote: | Hi Doc,
We seem to be following each other around the board today
|
TAG! YOU'RE IT!
Quote: | Could you post some pictures of your flexible sized frames along with your corner guides? |
Hmmm... I guess I need to take some pictures of those things.
Here's a couple of picture of frames, with the handles on
and taken off
but they don't show much beyond that.
(It's easy to take the bent-wire handles off---you just squeeze the handle to narrow it, and pull it away.)
If the handles aren't in the way of your guides, or keeping your plastic from fitting in your oven, you don't have to take the top ones off.
If you use a C-channel bottom frame, with the clip bottom inside the C, you don't have to take the bottom ones off, either. That can really speed up clamping and unclamping the plastic. Taking the handles off and putting them back on is easy, but gets a bit tedious doing 2 handles per clamp.
The main reason I made a couple of C-channel bottom frames was for forming thick plastic---the large binder clips weren't big enough to easily clamp around 2 layers of windowscreen frame and 1/4" or 3/8" plastic. (I think I'll look for extra-large binder clips, because I like the mix-and-match aspect and the cheapness of the windowscreen frames.)
The corner braces for the frames are similar to these:
They slide snugly into the frame side pieces. You need to cut the pieces at 45 degrees so that they meet with the corner brace fully enclosed.
This picture shows what happens when you (a) don't put the clips on with the rolled parts inward far enough, and (b) don't have guides to help bring the frame down aligned with the gasket.
(You also get a side view of the frames with 1/8" EVA craft foam clamped between them.)
Note the dents where the rolled part got mashed into the foam. (With high vacuum, they can cut all the way through the gasket.)
I make much better gaskets these days, and treat them better. _________________ Paul (a.k.a. Dr. Crash)
Tired of buying cheap plastic crap? Now you can make your own! www.VacuumFormerPlans.com |
|
Back to top |
|
 |
cod Master
Joined: 05 Nov 2006 Posts: 322 Location: San Francisco
|
Posted: Tue May 15, 2007 3:45 pm Post subject: Re: Multiple frames on one platen? |
|
|
jzawacki wrote: | Based off of what DrCrash is saying in this thread, How do you construct different size frames to work on a single size platen? And what is the best material to use for covering the platen holes?
|
this is not quite what you are looking for, but it might spark other ideas: this adjustable, 'professional' frame system is made from readily available powerstrut(unistrut?). I think it's quite clever, using heavy duty 'off-the-shelf' hardware.
http://www.tk560.com/phpBB2/viewtopic.php?t=558 _________________ <.o'> |
|
Back to top |
|
 |
jzawacki Novice
Joined: 12 Jan 2007 Posts: 70 Location: Illinois
|
Posted: Tue May 15, 2007 6:37 pm Post subject: |
|
|
Quote: | Did you read the section on frames in my draft "Chapter 2"? |
Yup, read the 101 ways to make frames.. But I don't remember reading what you just said about the screen frames and the mix and match approach.. I really like that idea.
Also, I didn't think to put the buck (classic wrench in this case) on a standoff (even though I knew I should), which would have fixed the problem I had.. not that over heating the plastic helped any.
And I have no idea why I didn't think to use plastic to cover the platen holes.. I was using cardboard with a pile of "for sale" signs sitting next to the platen.. Duh.. It seems like every time I see pics posted I feel like I am over engineering this thing.. Hopefully it will pay off in the long run. :/ |
|
Back to top |
|
 |
drcrash Guru

Joined: 04 Sep 2006 Posts: 705 Location: Austin, Texas
|
Posted: Tue May 15, 2007 7:41 pm Post subject: |
|
|
jzawacki wrote: | Quote: | Did you read the section on frames in my draft "Chapter 2"? |
Yup, read the 101 ways to make frames.. But I don't remember reading what you just said about the screen frames and the mix and match approach.. I really like that idea. |
I saved the best for last, and you probably glazed over by around 100.
There's even a trick so that you don't even need 4 of each side size (for opposing sides of top & bottom frames)... you just need 2 of each size, as long as you have longer sizes lying around. (Or just scraps of something else; it doesn't have to be window screen frame stuff.) You just make the bottom frame out of the "right" sizes, and then clamp some other-size strips over the tops to hold the plastic down, with extra length bits hanging out at the corners.
That's a little more hassle than just clamping two frames together around the plastic, but it works fine if you're just doing a few things of a given size. In effect, you get mix-and-match sizes for the bottom frame, and an adjustable frame for the top. _________________ Paul (a.k.a. Dr. Crash)
Tired of buying cheap plastic crap? Now you can make your own! www.VacuumFormerPlans.com |
|
Back to top |
|
 |
|
|
You cannot post new topics in this forum You cannot reply to topics in this forum You cannot edit your posts in this forum You cannot delete your posts in this forum You cannot vote in polls in this forum
|
Powered by phpBB © 2001, 2005 phpBB Group
|