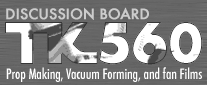 |
www.TK560.com Vacuum Forming, Movie Prop, Sci-fi and GIjOE Forum
|
|


|
View previous topic :: View next topic |
Author |
Message |
jegner Site Admin

Joined: 30 May 2003 Posts: 2144 Location: Texas, USA
|
Posted: Wed Sep 12, 2007 12:58 pm Post subject: Resin for vac molds |
|
|
I get asked a lot, what is a good resin for making vac-form molds. Well, here is the one I'd choose:
http://www.smoothonsecure.com/store/product_info.php?cPath=291_1_10&products_id=187&osCsid=4175cc85314e2a2f88159b40e4dee5b2
Called SmoothCast 385 its a 5:1 ratio urethane resin that is mineral filled. Has some good specs for vacuum forming, mostly compression strenght and heat tollerance.
My suggestion if you want to duplicate your master pattern in an effort to get more pulls per sheet of plastic, you can try making copies out of UltraCal30, HydroStone, or Rockite, but over time these product will shrink or crack. A resin based material might be a better option for a production mold. Plain old resin will work but is more expensive than this stuff, and the SmoothCast385 is made specifically for vacuum forming mold patterns.
At $52 for a 12 pound [1 gallon] kit, these might be a good option for some folks doing small runs, and don't want to mess up their hard-to-make-easy-to-break masters.
Jim |
|
Back to top |
|
 |
drcrash Guru

Joined: 04 Sep 2006 Posts: 705 Location: Austin, Texas
|
Posted: Wed Sep 12, 2007 4:37 pm Post subject: BC 8002 Kwik Kast II |
|
|
Plaster and gypsum cement shouldn't shrink, I don't think. They actually swell a tiny bit when they're setting, but once they're set and dry, I tink they're pretty dimensionally stable.
They will chip eventually, though. One thing I've been meaning to look into is additives that make gypsum cements less brittle. There are plasticky things you can add (some of them are some melamine stuff) to give them properties intermediate between gypsum cement and plastic. Sculptors often use them, and I'm wondering if they'd work for vacuum forming molds.
As far as resins go, here's the one that Doug Walsh recommends called BC8002 Kwik Kast II from BCC.
http://www.meyerplastics.com/mold_making_materials/polyurethanes_sht.htm
He says it's an easy 1:1 mix, works great, and costs a lot less than most of the competing ones. _________________ Paul (a.k.a. Dr. Crash)
Tired of buying cheap plastic crap? Now you can make your own! www.VacuumFormerPlans.com |
|
Back to top |
|
 |
drcrash Guru

Joined: 04 Sep 2006 Posts: 705 Location: Austin, Texas
|
Posted: Wed Sep 12, 2007 5:00 pm Post subject: TC1630 Ultracast |
|
|
This page has a link to a .pdf about BJB's TC1630 Ultracast.
http://www.liquidplasticsolutions.com/bjbfillunfill.htm
Here's the .pdf
www.liquidplasticsolutions.com/pdf/tc1630.pdf
It's another 1:1 mix filled urethane often used for vacuum forming molds.
The neat thing about it for me is that you can cast it in alginate molds. (It even says so in the .pdf.) Alginate molds are a lot cheaper than silicone molds.
(Thanks to Gobler for pointing this one out.) _________________ Paul (a.k.a. Dr. Crash)
Tired of buying cheap plastic crap? Now you can make your own! www.VacuumFormerPlans.com
Last edited by drcrash on Fri Sep 14, 2007 7:06 am; edited 1 time in total |
|
Back to top |
|
 |
jegner Site Admin

Joined: 30 May 2003 Posts: 2144 Location: Texas, USA
|
Posted: Wed Sep 12, 2007 5:02 pm Post subject: |
|
|
Where can you buy the BCC resins? That BC8002 looks pretty good, but I don't see a cost. Did I miss it?
As for Gypsum or P.O.P. if mixed 'heavy' it won't shrink much, but over time it will as the H2O evaporates. Rockite actually expands slightly as it sets. Somethign like .01% IIRC.
My issues with POP and Gypsums are they are too brittle, but fine for short runs. |
|
Back to top |
|
 |
drcrash Guru

Joined: 04 Sep 2006 Posts: 705 Location: Austin, Texas
|
Posted: Wed Sep 12, 2007 5:56 pm Post subject: |
|
|
jegner wrote: | Where can you buy the BCC resins? That BC8002 looks pretty good, but I don't see a cost. Did I miss it?
I haven't found a price online. You may have to call BCC.
Here's there home page... it's got their order line & tech assistance numbers at the bottom:
http://www.bccproducts.com/
|
_________________ Paul (a.k.a. Dr. Crash)
Tired of buying cheap plastic crap? Now you can make your own! www.VacuumFormerPlans.com |
|
Back to top |
|
 |
Jr Branham Novice
Joined: 09 Jun 2007 Posts: 28 Location: Georgia
|
Posted: Wed Sep 12, 2007 8:11 pm Post subject: Bcc Stuff |
|
|
Hey gang,
I have used the Bcc resins. The gray one is a bear to mix. I tried the blue one (8650, I think) and it was much more user friendly. The grey stuff will settle real bad in the can. Both pour real well. My molds are very heavy.
Jr. |
|
Back to top |
|
 |
kayaker43 Expert
Joined: 13 Jun 2007 Posts: 175
|
Posted: Wed Sep 12, 2007 8:47 pm Post subject: |
|
|
The BCC 8002 gray resin settles out because I think the filler is aluminum. Its worth getting a mixer for your drill because the aluminum is a good thing for our uses. Once mixed, its a dream to work with and pours easily with no degassing needed.
Its been a while, but the last batch I bought was $52.00 for a two gallon kit. Most everything else is twice that? _________________ Doug Walsh
www.build-stuff.com
Hobby-Vac and Proto-Form machine plans
Also other plans books and videos for people who like to build things |
|
Back to top |
|
 |
drcrash Guru

Joined: 04 Sep 2006 Posts: 705 Location: Austin, Texas
|
Posted: Wed Sep 12, 2007 8:56 pm Post subject: Re: Bcc Stuff |
|
|
Jr Branham wrote: | Hey gang,
I have used the Bcc resins. The gray one is a bear to mix. I tried the blue one (8650, I think) and it was much more user friendly. The grey stuff will settle real bad in the can. Both pour real well. My molds are very heavy.
Jr. |
Did you use a drill to mix, or were you doing it by hand?
Is the blue more expensive? _________________ Paul (a.k.a. Dr. Crash)
Tired of buying cheap plastic crap? Now you can make your own! www.VacuumFormerPlans.com |
|
Back to top |
|
 |
kayaker43 Expert
Joined: 13 Jun 2007 Posts: 175
|
Posted: Wed Sep 12, 2007 9:06 pm Post subject: |
|
|
If you buy from a distributor it could have been sitting for a year? Ask them to put it on the shaker first.,.. or get a jiffy mixer for the drill.
The colors are the same price I think, but I'm pretty sure they use talc and pigment instead of aluminum powder. They should all work, but the aluminum filler might make it more stable? My molds hardly shunk and never warped. Can't beat black/white 50/50 for easy mixing. _________________ Doug Walsh
www.build-stuff.com
Hobby-Vac and Proto-Form machine plans
Also other plans books and videos for people who like to build things |
|
Back to top |
|
 |
drcrash Guru

Joined: 04 Sep 2006 Posts: 705 Location: Austin, Texas
|
Posted: Wed Sep 12, 2007 9:25 pm Post subject: casting thin shells to save expensive resin |
|
|
Here's a video from Freeman Manufacturing and Supply on making parts by casting a slightly undersized plug to fill up most of the space (out of something cheap) and then pouring expensive stronger stuff between the plug and the mold:
http://www.freemansupply.com/video/surfacecasting/surfacecasting.htm
They call it "surface casting" but I don't know if that's a standard term.
If you have a rubber mold, that seems like a great way to make a vacuum forming mold. You'd probably only need 1/8" or so of expensive filled resin, and the cheap plug in the middle could be made out of something much less expensive, like 6lb expanding urethane foam and styrofoam rubble, or even concrete.
(Concrete is a bitch to drill, and heavy but pretty literally dirt cheap... a few dollars for 90 lbs. If you cast your vent holes in, and know you won't have to drill it, it's worth considering.)
One non-obvious advantage of this technique is that you don't get much shrinkage or expansion. You cast the middle part first, and it takes up almost the entire volume. After it sets/dries/whatever and gets to its final size, you cast the thin shell around it. That will automatically fill in for any shrinkage of the middle part, and you only get as much shrinkage after that as the thickness of the shell times the shrinkage factor.
Freeman has some cool videos... here's the link to their video library:
http://www.freemansupply.com/video.htm
BITY Mold Supply in Dallas also has some cool molding and casting videos on YouTube. Here's their channel:
http://youtube.com/user/brickintheyard
Freeman has a channel there too, and so does our very own Jim. Here's my channel, which has all those channels as subscriptions:
http://www.youtube.com/profile?user=vacuumformer _________________ Paul (a.k.a. Dr. Crash)
Tired of buying cheap plastic crap? Now you can make your own! www.VacuumFormerPlans.com |
|
Back to top |
|
 |
Jr Branham Novice
Joined: 09 Jun 2007 Posts: 28 Location: Georgia
|
Posted: Thu Sep 13, 2007 5:53 pm Post subject: BCC |
|
|
I purchased mine from a fellow named Nelson Burke, his company is called "the engineer guy" he is located in Atlanta, Ga.
The first batch I did mix by hand...mistake!!!, the next batches I used a jiffy mixer. I did not mean to say it was difficult to use, it was just hard to mix, I think it had settled. Once mixed, both were easy to pour. |
|
Back to top |
|
 |
tubachris85x Master
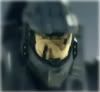
Joined: 15 Jan 2007 Posts: 351 Location: Ft. Lauderdale, Florida
|
Posted: Thu Sep 13, 2007 8:24 pm Post subject: |
|
|
Just saved all those freemman vids on my hardrive! _________________
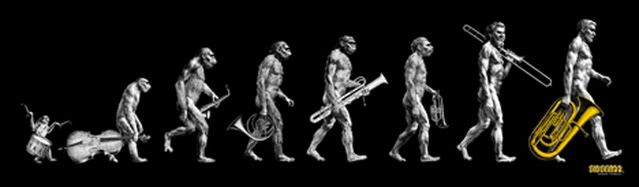 |
|
Back to top |
|
 |
knightshade Expert
Joined: 19 Jun 2005 Posts: 123 Location: Rochester NY
|
Posted: Sat Sep 15, 2007 4:01 pm Post subject: |
|
|
For a while now, I have been using fiberglass resin for my molds.
By the specs, it isn't as strong as what is suggested here - but it is quite a bit cheaper (~$35 a gallon) and easy to pick up locally. I have yet to have a mold break or chip while forming.
The down side with fiberglass resin is that you need a good (ventilated) place to work with it.) |
|
Back to top |
|
 |
drcrash Guru

Joined: 04 Sep 2006 Posts: 705 Location: Austin, Texas
|
Posted: Sat Sep 22, 2007 8:50 am Post subject: polyester & epoxy laminating resin gotchas |
|
|
Knightshade, how are you using the polyester fiberglass resin to make mold?
I'm guessing you're not pouring it solid. (?)
Laminating resins (for fiberglassing) are generally high-exotherm, meaning they give generate a lot of heat when they "kick". Solid pours may get REALLY REALLY hot, and I've heard they can even explode when they get too hot (the free styrene monomer boils, or something). Casting resins are generally low-exotherm so that they don't do that.
Another gotcha for some applications is that regular polyester fiberglassing resin is usually air-inhibited, meaning that it won't set up properly if you coat something with it---it stays tacky. That's a good thing for what it's designed for---laminating---because it means one layer won't cure too much before the next layer is applied, if you do it in a reasonable period of time, and they'll bond better. (Maybe it also extends the shelf life of an open can.)
(I have a couple of platens I sealed on the bottom with polyuester fiberglassing resin, and one set up fine but the other is permanently tacky. Or maybe I'm misremembering, and I did the one that's fine with epoxy. (?) )
TJ's book talks about demolding fiberglass when it's green, but I'm wondering if that leaves you with something that stays tacky/gummy on the surface. (Maybe you can paint it anyway, and then the surface will cure? But if there's a bad interaction with the uncured resin and the paint, you might get orange peel or something?)
I'm thinking of making some molds with cheap polyester, in female molds, doing the normal gel coat (impression coat) followed by a few layers of fiberglass cloth or mat layup. Then I'll fill that fiberglass shell pretty solid with something cheap, but I'm not sure what.
I've seen people talk about doing the impression coat with the same (laminating) resin, or a 50/50 mix of resin and Bondo (which is polyester resin plus microballoon filler). I don't know if Bondo is air-inhibited.
Another gotcha I've encountered with polyester: if you apply it over epoxy, it may partially dissolve the epoxy and leave a gummy mess. I think it may be fine over fully cured epoxy, but most room-temperature epoxies never actually cure fully. (You need to post-cure them at an elevated temperature to drive the cure reaction almost to completion, and then give them another week to sort themselves out. Hyeesh.)
I had one platen edge I'd sealed with epoxy glue, and put polyester over it. Oops... I ended up scraping and sanding it all off, and just putting epoxy finishing resin on it. The bottom line there is that if you're making a platen or a mold with epoxy (maybe just glue on parts of it), be very careful about putting polyester over it.
The gummy surface problem may be easy enough to fix, for molds---maybe you can just sand the gummy layer off. (?) A finely-sanded surface is A Good Thing for molds anyhow. (And for other things, that you want to paint.) _________________ Paul (a.k.a. Dr. Crash)
Tired of buying cheap plastic crap? Now you can make your own! www.VacuumFormerPlans.com |
|
Back to top |
|
 |
jegner Site Admin

Joined: 30 May 2003 Posts: 2144 Location: Texas, USA
|
Posted: Sat Sep 22, 2007 9:42 am Post subject: |
|
|
A well made fiberflass mold will be strong enough for even a 29.9 in/hg vac forming needs. You of course needs to make the molds 'husky' like they way boats and car body panels are made but thats about 4-6 layers of FG and resin. Nice thing, FG molds are light weight and easy to repair!
Jim |
|
Back to top |
|
 |
|
|
You cannot post new topics in this forum You cannot reply to topics in this forum You cannot edit your posts in this forum You cannot delete your posts in this forum You cannot vote in polls in this forum
|
Powered by phpBB © 2001, 2005 phpBB Group
|