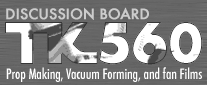 |
www.TK560.com Vacuum Forming, Movie Prop, Sci-fi and GIjOE Forum
|
|


|
View previous topic :: View next topic |
Author |
Message |
samuelha773 Newbie
Joined: 06 Apr 2009 Posts: 5 Location: Troy, NY
|
Posted: Mon Apr 06, 2009 12:32 pm Post subject: New 2x4' vacuum former that I built |
|
|
I've been working on a vacuum forming machine to form 2x4 foot sheets.
So far I've done a few test pulls using 0.030" PETG. Haven't had great success, need to improve heating, particularly in the corners.
I'm considering rebuilding the machine to be a top-down design instead of 180 degree flip flop style.
Will post pics ASAP. _________________ -Sam |
|
Back to top |
|
 |
samuelha773 Newbie
Joined: 06 Apr 2009 Posts: 5 Location: Troy, NY
|
Posted: Mon Apr 06, 2009 12:35 pm Post subject: Pictures of new 2x4' vacuum former |
|
|
What do you think? How can I improve this machine to get better, tighter pulls? _________________ -Sam |
|
Back to top |
|
 |
jdougn Guru
Joined: 18 Mar 2009 Posts: 714 Location: Louisville KY area
|
Posted: Tue Apr 07, 2009 6:43 am Post subject: |
|
|
Other guys will have better answers but I know that some specs on the system will help.
What are the specs on the machine?
What size are the tanks?
What CFM of vacuum through the pump?
How much vacuum does the Pump pull in inHG?
What thickness and type of plastic are you trying to pull?
How much sag in the plastic before flipping?
For some reason the pict links weren't working but I cut-n-paste. Looks like a nicely built machine.
DougN _________________ DougN - Just in case you're wondering, I got my "rating" legitimately... by posting aimless drivel, useless advice, and pointless questions. |
|
Back to top |
|
 |
samuelha773 Newbie
Joined: 06 Apr 2009 Posts: 5 Location: Troy, NY
|
Posted: Tue Apr 07, 2009 7:22 am Post subject: |
|
|
21.5x45.5" platen with 1/16" holes spaced every 1"
30 gallon tank with a Robinair 15600. Able to get to 28 in of Hg.
tank to platen is 3/4" steel pipe... not sure of the CFM but it empties real fast. I also have a check valve and fitting to attach the shop vac for additional pulling.
So far I've been working with 0.030" PETG. I get a 6" sag before pulling. However, it's very soft in the middle, and not really soft at all on the edges and corners. I think the steel frame is acting as a heat sink perhaps?
I am considering rebuilding this as a top down machine. That way I can get the plastic much closer to the heating elements. Also, the steel frame is fairly heavy so flipping isn't as fast as I'd like.
What do you think? How can I improve this machine and get some nice tight pulls?
Thanks in advance for your advice! You guys rock! _________________ -Sam |
|
Back to top |
|
 |
jegner Site Admin

Joined: 30 May 2003 Posts: 2144 Location: Texas, USA
|
Posted: Tue Apr 07, 2009 11:11 am Post subject: |
|
|
PETG is slow to heat up, and slow to cool down, and if your machine is leaking air, you will loose the tight pulls. double check for air leaks. Take a flat sheet of cold plastic, lay it on the platen. Turn your vacuum on. Can you slide your plastic around on the platen?
Also, temp control is paramount. And PETG is hard for new formers to work with. Try using some HIPS as test material.
Jim
BTW, nice looking machine! What are you forming? |
|
Back to top |
|
 |
ANH trooper Master
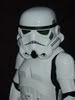
Joined: 20 Oct 2005 Posts: 305 Location: UK
|
Posted: Tue Apr 07, 2009 12:07 pm Post subject: |
|
|
There are two main factors for successful pulls, heat and vacuum. You need both or you are not going to get anywhere with your machine.
One problem that I can see is that your oven does not have tapered walls, so the heating elements are not larger than your sheet of plastic, which it needs to be. If there is any way of making the oven floor larger and adding an extra outer coil, this should help a lot.
Another problem is the distance between your holding frames and heating elements. I have never formed PETG but from what I have read, it needs a lot of sag and may need more than your machine allows. An over head heater would bet better for this kind of plastic (unless you can lower the oven and make the walls taller).
If your tank is reading 28 in/hg and it is holding the vacuum, you shouldn't have any problems really. Your pump should be running the whole time through the forming process and not just for evacuating the tank. I turn on my pump just before I am ready to lower the plastic and keep it running until I am happy with the pull. If you got an air tight seal, the vacuum should hold even when the valve to the tank is closed and it should be hard to lift off the frame.
Nice looking rig too mate. I hope you manage to sort out the problems soon! |
|
Back to top |
|
 |
crashmann Guru

Joined: 27 Sep 2005 Posts: 501
|
Posted: Tue Apr 07, 2009 12:47 pm Post subject: |
|
|
Hi Sam,
Nice rig you've got there! I see you used a shield to help slow down the heating in the middle of the sheet versus the edges, but it's still not enough. The metal frame will act as a heat sink, so when I'm warming up my oven, I flip the frame onto the oven and heat it up as well.
Your nichrome coils are evenly spaced on the oven. Many folks will reduce the spacing for the outside coils, or add an extra row on the outside to create more heat at the edges of the plastic.
The shape of your mold has some very steep sides. Even with styrene, you would have a difficult time getting those shapes to work. Plus, once the plastic is pulled, you'll have a very difficult time extracting the molds. If possible, try to add some taper to the sides which will encourage the plastic to flow over the mold and also aid with release after being pulled. It looks like you've got a nice shop there, so you might want to make a reverse or "negative" mold. That would prevent the webbing you see in the corners.
I agree with Jim that PETg is very temperature sensitive, so as you are flipping the sheet over, it is losing lots of heat. If you can engineer an over under design, that would be a huge improvement. Plus, as ANH Trooper pointed out, when the plastic is heated, the center sags away from the heat source allowing the edges to absorb more heat.
Good luck!
Charlie |
|
Back to top |
|
 |
samuelha773 Newbie
Joined: 06 Apr 2009 Posts: 5 Location: Troy, NY
|
Posted: Tue Apr 07, 2009 1:01 pm Post subject: |
|
|
I'm using this machine to make some cheap prototype molds for an engineering project at my company. Those molds in the picture have a 5 degree taper on them.
I've decided to rebuild the machine as an over/under design. That should get the plastic to about 2" from the nichrome to increase heating. Do you think I will still need to add an additional outer loop of heating element?
I will re-test the flat plastic vacuum test later today, but I recall it being very hard to move a flat sheet. I used contact cement to attach the aluminum to the MDF platen, and then drilled all the holes. Then the MDF top and bottom were wood glued together. Could this construction method be leading to leaks?
I've got 1 4x8' sheet of styrene, I'll do my next test pull with that, but we've got lots of PETG, which is ultimately what we'll probably use.
Thanks for the advice! I'll post new pics in a few days. _________________ -Sam |
|
Back to top |
|
 |
spektr Master
Joined: 07 Jan 2008 Posts: 425
|
Posted: Wed Apr 08, 2009 7:54 am Post subject: Ahhh Yes, the tuning of a new machine..... |
|
|
Ok lets start with the simple stuff...
1) seal the MDF, it normally leaks quite badly, in fact you can probably suck air thru it with your mouth.. Try it and then realize how important proper sealing is.... Tiny leaks add up fact.. Use shellac, 2 or 3 coats.. It sinks in and does yoeman service in this application. I like shellac because it drys fast, can be recoated immediately and cleans with alcohol.........
2) you need to space the tool off the platen by .040 or so because
you cant pull a hard corner unless the vacuum pulls from under the edge of the tool.
Now some technique stuff.........
3) I suspect that your sheet is too hot. I see this a lot. You have too much prestretch and the material is pinned to the platen by the outside vac holes....... This prevents the plastic from sliding to the mold like it needs to and promotes excessive part thinning. It also pulls the heat off the plastic before you can get all the air removed preventing the part from forming.
4) I see no lube.... I use Tire Wet to get the plastic slipping over the mold surfaces.
A Tool Design thought......
5) This should be a cavity mold. Convert it by adding a rail the height of the mold to the outside of the platen. Use a 1x2 wood furring strip. Carpet tape it to the platen and seal the corners with tape. This will hold the plastic level above the mold and stop the excessive chilling that is hurting you.
A process change....
6) ADD SECONDARY OPS if you need them.. If your tool is so poor that you can't pull it in 1 shot, do it twice. Add a port for a shop vac to the plenum. shut off the high vac and pull again with the shop vac. Jump all over it with a heat gun to "fix" the places it didnt work.
Scott. |
|
Back to top |
|
 |
|
|
You cannot post new topics in this forum You cannot reply to topics in this forum You cannot edit your posts in this forum You cannot delete your posts in this forum You cannot vote in polls in this forum
|
Powered by phpBB © 2001, 2005 phpBB Group
|