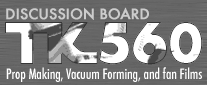 |
www.TK560.com Vacuum Forming, Movie Prop, Sci-fi and GIjOE Forum
|
|


|
View previous topic :: View next topic |
Author |
Message |
CrazyFool Expert

Joined: 07 May 2008 Posts: 203
|
Posted: Sun May 25, 2008 6:23 pm Post subject: |
|
|
Just a quick note. I really appreciate everyone's kind words and I will try to answer all of your questions soon. Busy making forms right now (covered with sawdust!) and hope to try the first pulls tonight...
CF |
|
Back to top |
|
 |
CrazyFool Expert

Joined: 07 May 2008 Posts: 203
|
Posted: Tue May 27, 2008 1:36 am Post subject: |
|
|
jegner
Thanks man! Your site rocks (and so far I've only explored the vacuforming stuff). The guys here a super. Absolutely.
ahillworks
Thanks! The nichrome wire was easy to stretch per jegner's instructions. Attaching it to the ceramic posts was tedious but not terrible. Wiring it up was pretty simple, although I would recommend asking a friend to check your work if you haven't wired too many things.
Vader
I'm not sure if I will be dabbling in the sign business now but I won't rule it out either. This project was to make new signs for a string of automotive businesses that my boss owns (that are completely non-sign related). 'The 7 Day Machine'. I like that. Just so long as it's not the 7 day wonder that blew up on day 8. lol When the new signs finally go up I will try to get some photos without revealing exactly what the business or its name is (to protect my boss's privacy).
Paratech1
You're welcome and thanks! I was trying to plan everything but ran out of time and had to just start nailing boards together. I'm surprised it doesn't look more frightful than it does.
Cheese
Thanks man! I wanted to save space too, especially with a larger machine. Cost estimate... I will be going over those numbers in a couple of weeks. I was in such a hurry that I made multiple trips to Lowe's and just threw whatever I thought I might need into the cart. Lowe's is cool because you can take stuff back. I will probably return about 25% of the things I bought. A very, very rough estimate..? You know I hate to even try and say. It's mostly just wood and screws. The most expensive things were the ceramic insulators (which you don't absolutely need). The shop vacs were about $65 each. I'll try to whip up a cost break down in two weeks. I'd like to know myself.
TK 109
It's not a machine until it can pull something. I hear that. The anticipation (and some dread) was starting to get to me. Finally did my first pulls a few hours ago - photos below. I still need a lot more practice. Today was troubleshooting 101. I'd like a 2nd 'high vacuum' source but I really don't have time right now. My boss wants his signs ASAP and I think what I'm beginning to pull now might be acceptable. My right oven is not heating the plastic as well as the left oven. Not sure why yet. Overall the heat is pretty good though. I could use a helper to help hold down the large 4' x 2' frames while we both work in the details around the forms with our fingers. I only have a few seconds with 1/8" plastic to get a seal and massage the plastic around the forms.
CF |
|
Back to top |
|
 |
crashmann Guru

Joined: 27 Sep 2005 Posts: 501
|
Posted: Tue May 27, 2008 11:34 am Post subject: |
|
|
Why am I reminded of Sesame Street?!?
Today's posting is brought to you by the letter "O"
Great success with your first pulls!
You may want to move the handles on the plastic clamping frames. I noticed you've got them on the bottom frame, and as long as your clamps are tight, they should work. But it would be even better to have your downforce on the upper frame.
Regarding the right oven running a little cooler - Did you check the resistance of the nichrome coils with an ohm meter to make sure each segment is the same as the left oven? To do this, you'll need to disconnect the wiring on the back, since that ties all of the coils together to make one big parallel circuit.
If the temperature difference is significant (impacting performance), then you may want to stretch the nichrome a little on each segment (maybe an inch), then fire it up again. Continue stretching until the temperature evens out.
Charlie |
|
Back to top |
|
 |
jegner Site Admin

Joined: 30 May 2003 Posts: 2144 Location: Texas, USA
|
Posted: Tue May 27, 2008 11:40 am Post subject: |
|
|
What sort of plastic are you using? Thickness is .0125? [1/8th inch]? Just running a shop vac as your vacuum source, your pulls are amazingly tight for that thick of plastic. In order to get tighter pulls, your going to need a stronger vacuum source OR thinner plastic.
Some folks suggests, for a shop vac powered machine, .040 as the upper limit, but I get good results with up to .093. Your parts just need to be raised up above the forming platen sitting on 'risers', but your needs may be different, you may not be able to do that. Depends on how you need to cut those letter forms out.
Looks great!
Jim |
|
Back to top |
|
 |
cod Master
Joined: 05 Nov 2006 Posts: 322 Location: San Francisco
|
Posted: Tue May 27, 2008 5:11 pm Post subject: |
|
|
Wow, good work. very impressive. Inspiring.
I think you might've gotten your pulley idea from me ?
http://cjod.net/cpg/thumbnails.php?album=2
I'd like to be a worry wart and say a few things about that pulley setup of yours- it looks like its mounted on the inside of the oven- I would seriously consider what might happen if that cable flies loose and touches some live current. If there's a way you can ground it you might be safer- the wood handle certainly helps .....but I am concerned.
Also , are you saying that your wires up top had fused together ? That should not be happening - it means the wire is over-capacity..... are you using standard house wiring up there ? I would use oven wire with a glass shell, of the proper amperage .......It's great to cut corners and all, but this is serious business. You don't wanna burn down your bosses' shop- or worse!
Colonel 2 Cents _________________ <.o'> |
|
Back to top |
|
 |
CrazyFool Expert

Joined: 07 May 2008 Posts: 203
|
Posted: Wed May 28, 2008 12:45 am Post subject: |
|
|
crashmann
I'd like to buy a vowel please. Actually, I have the vowel. Now I'm trying to get a decent 't' and 'G'. Those handles? Oh yeah. I put those on in the very beginning, before I added the pulley system (when I found out I would be doing everything alone). I haven't been using the handles, but I like your idea about putting them on top. I'll have to delve into your ohm meter recommendation when I can pause long enough to do some fine tuning. Thanks for the info!
jegner
I'm stuck using some stuff called 'sign white' (in order to match the plastic in the portions of the existing signs that will remain - we are changing some letters but not all of them). It's the typical semi-transparent white that most business signs use. There are fluorescent lights behind the letters that illuminate the letters at night. Unfortunately, sign white only seems to come in 1/8" and 1/4". I'm beginning to think (after some unacceptable pulls today) that the main reason I got a decent 'o' is because I had reheated the same sheet of plastic about 4 times while practicing and basically thinned out the plastic, allowing for an easier pull. You are correct that I cannot raise the letters up on risers because I need a flange around the letters (see photo of cut out 'o'). The existing signs are pretty basic. They are sheet metal boxes painted opaque white with light bulbs inside. Along the length of the metal boxes are letter shapes that have been cut out of the sheet metal. Poking through each shape is a plastic letter. At night, only the plastic letters light up. It's simple but very effective. The flat flanges around the letters are used to affix the letters to the inside of the metal boxes with double sided tape and caulk. When you say that it is very difficult to pull 1/8" plastic with vacuum power... do you mean it is not possible with vacuum power alone... or that it is not possible with vacuum power even if I add a secondary 'high vacuum source'. I'm beginning to stress out just a little. My boss expected the first sign to be done last week. I wonder if maybe rigging a platen that rises to the plastic might work better than what I have now. So the platen is forced up into the heated plastic while the plastic is still being directly heated. Then the vacuum kicks in. Then you lower the platen and plastic down together. I'm not sure if my problem is lack of vacuum, or that the thick 1/8" plastic cools before it can be fully formed... or both. (Sorry about writing a book here.) Thanks for any advice!
Edit: After hours of pouring over this site I'm starting to get the sinking feeling that, unless I have a 50 gallon tank and a high CFM vacuum pump I'm not going to get acceptable results pulling 1/8" plastic. Sigh...
cod
You are correct sir. My simple pulley system was inspired by your more complex (and far superior) system. I have been meaning to give everyone I've gleamed ideas from proper credit. I meant to put the pulleys on the outside of the oven but in my haste to build the thing I got the width measurements wrong somewhere. I'll have to correct that when I get the chance. The wires I'm using are heavy 10 gauge Romex. After placing the insulation under the wires (trapping the heat below the insulation and below the wires) the wires are all cool to the touch. I don't think I will have any more wiring issues now. I appreciate your concern and I share your concern too. Thanks. I frequently check the warmness levels of the wires, switch boxes, outlets, and breakers and keep a fire extinguisher nearby. I even go so far as to unplug the machine and turn off the breakers when I am not using it. Paranoid maybe, but I sleep better!
CF |
|
Back to top |
|
 |
ANH trooper Master
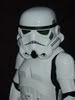
Joined: 20 Oct 2005 Posts: 305 Location: UK
|
Posted: Wed May 28, 2008 9:44 am Post subject: |
|
|
Good job on getting this far so soon CrazyFool!
I have an idea that might help get better pulls. If you plan on pulling three letters each time, could you add another hole in the middle of your platen and hook up either another shop vac or plumb all three holes to both vacs?
I think thickness of plastic doesn't make much difference to pulling plastic. There seems to be this consensus that thicker is harder to pull when I have found this to be untrue. What you need to do is get the plastic to the correct forming temperature and it will pull the same (obviously the thicker guage will have softer lines but should still pull as tight). I'd suggest more sag, like 8"-10" maybe more? Some of the vids on youtube seem to have a lot of sag, though I don't know what plastic they are using, would be worth experimenting with more sag.
A high vac will pull those things super tight, but I had super tight pulls with a shop vac using .100 and .125 HIPS. The trick was to let it sag as much as possible without over heating the plastic which causes orange peel. On my 24" x 24" I was letting the plastic sag a good 4" and the pulls would be as good as any high vac system.
I have never used the plastic you are using, but would suggest trying more sag and then adding the extra vac or hole to aid in air evacuation. You might need to retool your moulds and get rid of the mesh, but would be worth the effort if you get consistantly good pulls  |
|
Back to top |
|
 |
TK 109 Guru
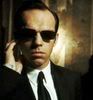
Joined: 11 May 2007 Posts: 712 Location: Galena, Ohio
|
Posted: Wed May 28, 2008 1:09 pm Post subject: |
|
|
very nice pull, especially for that thick of plastic. is it like an ABS-type-thing?
looks very nice.  _________________ -Alex
-------------------------------------------------------
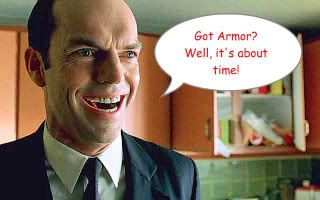 |
|
Back to top |
|
 |
CrazyFool Expert

Joined: 07 May 2008 Posts: 203
|
Posted: Wed May 28, 2008 6:49 pm Post subject: |
|
|
ANH trooper
Thanks man. It's mysteriously beginning to feel like 'work'! I will seriously consider adding a 3rd hole as you recommend. My design was based loosely on a YouTube video I saw ( http://www.youtube.com/watch?v=skNfOIbFWmk ). They seem to be pulling very large and thick stuff with just two shop vacs. I'm not sure how they are getting such good pulls, but their platen is a peg board design so maybe there is some merit to adding more holes.... hmm. Thanks for the encouragement and for sharing your experiences with just shop vacs. That gives me some hope. I'm not sure why I added the mesh. I saw it on this forum somewhere. I had a little vacuforming machine that I never got to work right and I remember one time there was no screen above the platen hole and the first thing it did was suck the plastic right down the whole and that was the end. Pull over. I've been starting to think about adding a dimmer switch to the shop vacs to make the vacuum gradually increase while also adding a rising platen that lifts to meet the still heating plastic (kind of like some of the really expensive vacuforming machines I've seen online). Hmm...
TK 109
Thanks. I'm beginning to regret the '7 Day Machine' moniker because I obviously have some modifications to do before it meets my needs. But I guess if I were pulling thinner stuff it might have worked as is (or is that 'as was'?). The plastic is an acrylic commonly referred to as 'Sign White Acrylic'. I'm nose sure of the exact specs (see photo below).
CF
Last edited by CrazyFool on Thu May 29, 2008 3:09 am; edited 1 time in total |
|
Back to top |
|
 |
CrazyFool Expert

Joined: 07 May 2008 Posts: 203
|
Posted: Thu May 29, 2008 1:50 am Post subject: |
|
|
I ALMOST CANNOT BELIEVE IT!!!
By building a VERY quick and dirty raisable platen out of cheap and embarrassingly bowed plywood and covered by nothing more than K-Y Jelly... I managed to pull thick 1/8" acrylic over 1 1/2" deep forms and end up with beautiful results the very first time!!
I was literally thinking about calling my boss yesterday and telling him I just wasn't going to be able to pull this sign making stuff off. Not unless I spent an additional $500 or $1000 on a high performance vacuum pump, a large, steel tank and days spent setting up a new high vac system. But before throwing in the towel I decided to try one last idea... I wanted to try raising the platen up to the frames while the plastic sheet being held in the frames was still under direct heat from the ovens. I thought that maybe the intense heat would help shape the plastic over the forms. This turned out to be correct beyond my wildest dreams!
How I modified things
1) Frames and plastic (a) still raised by existing pulley handle (a). Nothing changed there.
2) Made a super cheap platen (b) with a bar to raise it up (b)
3) Threw some 1 1/4" shop vac hoses (c) onto the bottom of the new platen and hot glued them into 1 1/2" PVC pipes running up through the new platen. Also hot glued the bottom of the hoses to PVC pipes in the top of the old platen (e). So the two shop vacs (c) pull through the old platen up through the new platen. Don't ask me why I did it exactly this way. I was in a hurry!! lol
4) Puked out some L-cheap'o wood stands (d) to support the new platen while in its down position so that the new hoses would have room.
How I did the pull
1) Raised frames up to ovens with pulley handle. Let the plastic heat for around 20 minutes until there was about 4 1/2" of droop in the plastic.
2) Raised new platen up to frames with new pulley handle. This was such a joke! You should have seen it. The new platen is such a piece of bent up plywood junk that it didn't even come close to sealing with the frames. Not even close. In the fully raised position (with heating plastic beginning to stretch over the forms) there were gaps of like 2 and 3 inches between the frames and platen. To 'fix' this I simply clamped the platen to the frames in the corners with c-clamps.
3) Left platen in up position (with heating plastic slowly shaping over forms) for about two minutes, maybe less. Did NOT turn on any vacuum during this time.
4) With platen still in up position and clamped to frames and ovens still on pumping out heat to the plastic... I turned on both shop vacs and let them run for around 3 or 4 minutes.
5) Turned off the ovens. Left shop vacs running for another 3 or 4 minutes while platen and frames where still in up position.
6) With shop vacs still running, I lowered the platen and frames together (still clamped together).
7) Left shop vacs running for a couple of minutes while I examined the remarkably sharp pulls. Then turned shop vacs off.
They say that 'necessity is the mother of invention' and this is a perfect example. I was really under the gun and grasping at straws looking for anything that might work, like... today. I guess even a CrazyFool can get lucky! I saw a video online somewhere of a very expensive and massive vacuforming machine that raised its platen up or lowered its heater and plastic down (I forget which, but same thing basically) and I thought, "Hmm. Why not try that?" So I copied somebody really. Which means the good idea was actually theirs! Oh well. d'oh! lol
CF
P.S. A very special thanks to ANH trooper for encouraging me to keep trying to pull thick plastic with just shop vacs. That was a shot in the arm I needed at the right time. Hey trooper... how did you learn so much being stranded on an island? This in no way takes away from other high vac guys who have been extremely helpful and a true source of inspiration. You know who you are and I hope you know that I appreciate your help (e.g. crashmann). |
|
Back to top |
|
 |
crashmann Guru

Joined: 27 Sep 2005 Posts: 501
|
Posted: Thu May 29, 2008 8:24 am Post subject: |
|
|
Wow, that is a fantastic pull!
I think most setups have the oven high away from the platen is so you don't burn your eyebrows off when pulling the plastic over your molds. By raising the platen up to the oven (like Dr. Frankenstein), you reduce the opportunity for the plastic to cool as the clamping frame is being lowered. Also, since the plastic was draping onto the molds and taking the shape while being heated, that certainly helped too!
When I build my huge over under setup, I am going to incorporate some of your ideas into the design. Either a raising platen or a lowering oven.
Thank you very much for sharing your experience with the board. Everyone can learn and benefit from your struggles and problem solving.
Great work!
Charlie |
|
Back to top |
|
 |
ANH trooper Master
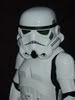
Joined: 20 Oct 2005 Posts: 305 Location: UK
|
Posted: Thu May 29, 2008 10:50 am Post subject: |
|
|
Congratulations mate, I'm really pleased for you
You have proved that if you stick with it, you can pull it off.
I like the idea of raising the platen. This means the plastic never really cools down which is a big factor in vacuum forming. Getting the plastic to the correct temperature is the key to successful pulls, so it doesn't matter what guage you are using, as long as it's hot it will pull.
Like I said earlier, shop vacs can pull very well for most plastics and used to pull HIPS super tight for me. ABS is a different ball game which needs a hi-vac but it looks as though the acrylic based plastic you are using is pulling just fine!
Well done CF  |
|
Back to top |
|
 |
TK 109 Guru
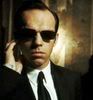
Joined: 11 May 2007 Posts: 712 Location: Galena, Ohio
|
Posted: Thu May 29, 2008 1:38 pm Post subject: |
|
|
WOW! with just a shop vac (or two, right?)??
that's tight. really nice pull, there. i would only be able to get that tight of detialing on the G if i overheated my plastic JUST right...
that's nice!  _________________ -Alex
-------------------------------------------------------
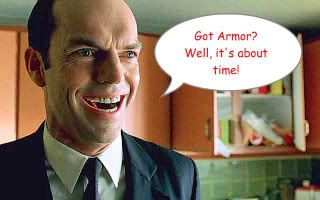 |
|
Back to top |
|
 |
ahillworks Master

Joined: 18 Nov 2007 Posts: 308 Location: Orlando FL
|
Posted: Thu May 29, 2008 5:56 pm Post subject: |
|
|
Very Very inspiring I can not wait for my rebate check from the government. I will be finishing the oven once i get it. Then its back to finishing my former. I would be so grateful to get results like theses. Very good job! Its post and people such as your self that make others want to be as successful. |
|
Back to top |
|
 |
CrazyFool Expert

Joined: 07 May 2008 Posts: 203
|
Posted: Fri May 30, 2008 7:19 am Post subject: |
|
|
crashmann
Thanks man. It was exciting. Apart from breaking the plastic molds trying to get my wood forms out (because I used K-Y Jelly instead of Baby Powder as a release agent) I didn't experience any negative effects other than some pitting here and there and a few spots where I felt the plastic should have been thicker. At first I thought the pitting was from K-Y Jelly boiling off and popping, but now I think the pitting (and thin areas) was probably due to overheating the plastic. I'll have to experiment some more but things are looking good. Can't wait to see your huge over under!!! That would be awesome.
ANH trooper
Thanks! It seems like a lot has happened in a short time and I can't help but wonder about all the things that might be accomplished if I start pushing as hard on other projects after this project is done.
TK 109
You are correct. Two shop vacs, each pulling a 2'x2' square area of platen. Basically just a 2'x2' machine doubled so I assume the same results could be had with a 2'x2' machine and one shop vac. Still working on monitoring the heating. So far I've only paid attention to 'droop' but I think it's time to get some kind of temperature gauge so that I can start making notes and tracking results for accuracy.
ahillworks
Thank you! I'm blushing (under my helmet). I hope your machine is a lot of fun for you. I'm looking forward to using my machine for some fun stuff after this sign business is done.
CF |
|
Back to top |
|
 |
|
|
You cannot post new topics in this forum You cannot reply to topics in this forum You cannot edit your posts in this forum You cannot delete your posts in this forum You cannot vote in polls in this forum
|
Powered by phpBB © 2001, 2005 phpBB Group
|