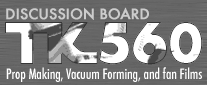 |
www.TK560.com Vacuum Forming, Movie Prop, Sci-fi and GIjOE Forum
|
|


|
View previous topic :: View next topic |
Author |
Message |
CrazyFool Expert

Joined: 07 May 2008 Posts: 203
|
Posted: Wed Jun 04, 2008 6:09 am Post subject: |
|
|
Here is the latest incarnation of 'the freak'. The raisable plywood form I made was really a proof of concept thing. It did work but the plywood was so warped that, when raised and clamped to the frames, it was pulling downward on the frames and causing a lot of stress on the pulley system. I may not be explaining that exactly right but let's just say, once I saw that a raisable platen would work the plywood platen had to be replaced. So I built a 3rd platen. The new platen is made of perfectly flat MDF board and covered with resin, producing a nice seal with the aluminum tube frames. However, the new MDF platen created problems of its own. The dang thing is HEAVY. I knew this might happen and tried to make it lighter by avoiding gluing 3 sheets of 3/4" MDF board together (a board for the top, a board beneath that, and a board for the 'table top' surface that the frames rest on). That would have been extremely heavy. Instead, I put one 21"x45" piece of 3/4" MDF board on the top but the sides and the surface that the frames rest on is only made of small pieces of MDF glued and screwed together. But... even with this lighter MDF platen design the thing was still too heavy for my existing pully system, so I reinforced both the pulley system and the vacuforming machine's frame. Not noted in the photos below are two extra 2"x4" boards in the rear of the machine (added vertically) and some metal straps that I screwed around the legs near the wheels.
This upgraded design, along with being careful not to heat my plastic too long, and reheating the plastic after the pull to aid in removing the forms... produced the first fully successful plastic molds that I consider 'production pieces' which will go up on one of my boss's automotive store fronts. The only thing I have left to do at this point is tweak my timing for tighter pulls and make a couple more forms.
Just a note for newbies who might think my ever-evolving machine is too much work and trouble and feel a bit discouraged... the machine did work as is (or 'as was') for most plastics within 7 days from start of construction to finish. The reason I have been modifying the machine is because I was forced by the project I'm working on to use a very thick 1/8" plastic that most people probably don't use very often, especially not people with shop vacuum powered machines and I didn't know anything about plastics starting out. Not trying to make excuses for myself by continuing to work on a machine that I said was built in 7 days. I just don't want anyone to be discouraged by all the work that went into my machine. You really can make a machine in one week!! The beefed up version of my machine could have been built in one week... but I did not know the machine would need more power (by way of a raisable platen in lue of a high vacuum pump and tank system) until later.
CF
P.S. I am toying with the idea (if I can squeeze in the time) of making a super light raisable platen out of flat, pink foam covered with epoxy resin and then coated with high temperature motor paint. It may need to be supported by fiberglass cloth as well. I've never tried that stuff but have always wanted to. Oh yeah... I also widened the opening on the letter 'G's wood form for an easier pull. |
|
Back to top |
|
 |
acrylikhan Newbie

Joined: 27 Jan 2008 Posts: 19 Location: Phyrexia, Illinois
|
Posted: Wed Jun 04, 2008 10:42 pm Post subject: |
|
|
That is a truly remarkable machine you've built!
My bucket is off to you!  _________________ Acrylikhan's Biker Scout Project: Go Fast, Go Splat! |
|
Back to top |
|
 |
TK 109 Guru
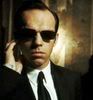
Joined: 11 May 2007 Posts: 712 Location: Galena, Ohio
|
Posted: Thu Jun 05, 2008 2:29 pm Post subject: |
|
|
yes, that's REALLY amazing! how much for your services?  _________________ -Alex
-------------------------------------------------------
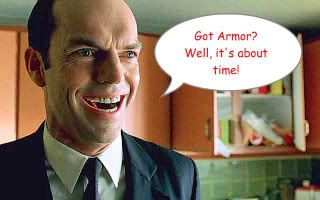 |
|
Back to top |
|
 |
CrazyFool Expert

Joined: 07 May 2008 Posts: 203
|
Posted: Fri Jun 06, 2008 5:42 am Post subject: |
|
|
acrylikhan
Thanks man!
TK 109
lol Thanks. Boy, it would be nice to pull stuff for money. After this project I'm not sure what's going to happen. Originally the owner of the business that needed modified signs was going to pay me $1,000 per sign and there were to be either 10 or 14 signs. But very early on the owner began to doubt my ability to actually produce the plastic molds and paired back the project to about 1/3 its original size. So I'm not exactly sure what I'll end up making. I still have to recoup my costs and my brother (who is married with three kids) lost his full time job and I asked him to work with me the next two or three weeks. He will help me to pull between 60 and 84 molds (around 17" x 17" x 1 1/2" each but some as large as 20" x 28" x 1 1/2"), cutting them out and carefully putting on the vinyl stickers - which are not cheap. In the end I may not make much of a profit from this deal, but it could open some doors so I'm OK with that. One thing I sure would like to do is finish the first sign so all that comes next is pumping out more plastic molds and sticking on the vinyl stickers. The construction phase (ended) and troubleshooting phase (almost over) have sapped me. I'm entering the fine tuning phase now but I'll be happy to exit that and move completely into the production phase. I won't actually be putting the plastic molds up on the building fronts. Someone else who owns a lift will be doing that.
CF |
|
Back to top |
|
 |
CrazyFool Expert

Joined: 07 May 2008 Posts: 203
|
Posted: Tue Jun 10, 2008 1:43 am Post subject: |
|
|
IT WORKS!!! PRODUCING PRODUCTION MOLDS!!!
What a learning process I tell ya but I have officially exited the troubleshooting phase and fine tuning phase (although does fine tuning ever really end?) and entered the production phase! Photos below are of my latest, largest and most complex pull just completed about 90 minutes ago. I'm not sure I could ask for better results using a home built shop vacuum powered machine pulling thick 1/8" plastic. There were no bubbling issues. No pitting issues. And the forms popped right out of the molds with almost no force and no reheating required. The way I managed that was to make the forms out of wood, coat the wood two or three times with epoxy resin (sanding the resin smooth after it hardened), and then smear a bunch of high temperature motor grease on the forms. That worked beautifully. I had tried the grease before and it didn't work. The forms kept sticking inside the plastic molds. But I guessed (without testing first - yikes) that the grease was being absorbed into the uncoated wood so I coated all of my wood forms with epoxy resin in hopes that the grease would not penetrate the wood, and keep doing its job of being all greasy n stuff. Thanks again you guys for all of your suggestions!!! They helped (and help) tremendously.
Not sure I could ask for a better pull with a shop vacuum machine...
Why I needed a big 2'x4' machine. The logo is alarmingly wide...
Demolding success within 1 minute...
Demolding secret: Forms covered with epoxy resin and high temperature grease...
A few notes about the procedure at this point:
1. Raise frames with plastic to completely cold ovens*
2. Turn on oven and let plastic heat for 18 minutes
3. Raise greased up platen and forms to frames and clamp to frames. (Takes me about 1 minute total.)
4. Let frames, plastic, platen, and forms heat under oven until minute 22.
5. Turn on shop vacuums and let run until 24 minute mark.
6. Lower everything down together. Leave vacuums running while massaging any corners, if needed.
7. Turn off vacuums about minute 25.
8. Frames unclamped, opened, and forms removed by minute 29.
*Starting procedure with completely cold ovens (at this point) in order to track results exactly. I guess it may not matter if the ovens are cold or hot to begin with, but if the ovens are hot when I am trying to insert the plastic into the frames and put the forms on the platen the plastic and forms can catch a lot of heat and get pretty hot before I am set to do the pull. And sometimes it takes me longer than other times to insert the plastic and get the forms ready. So I see that as an area of unpredictability that I wanted to eliminate.
Any and all comments, tips, and criticisms welcome!!
CF |
|
Back to top |
|
 |
jegner Site Admin

Joined: 30 May 2003 Posts: 2144 Location: Texas, USA
|
Posted: Tue Jun 10, 2008 6:50 am Post subject: |
|
|
Try talcum powder instead of grease to release your molds. I'm not sure of the way to grease will react to the plastic over time. But the talcum or baby powder works wonders! Put some in an old sock, then you just dab the mold and rub lightly.
Also, the heat cycle on my machine from cold takes about 10 minutes to get to a desired temp for pulling plastic, and the longer the oven is on, the hotter it will get. This has the net effect of the last few molds made are faster to heat, than the first few.
Your pulls look great. Can't wait to see the finished product!
YMMV
Jim |
|
Back to top |
|
 |
CrazyFool Expert

Joined: 07 May 2008 Posts: 203
|
Posted: Tue Jun 10, 2008 7:42 am Post subject: |
|
|
jegner
Thanks man. Last thing I need is my plastic molds to dissolve! For now I read that I can clean auto grease off of acrylic plastic with warm water and white dish soap. (But I'm not sure if that's typical auto grease or any type of auto grease.) I guess you don't want to use colored dish soap or it might tint your plastic, especially the semi-transparent plastic I'm using for the business signs. But I will take your advice and try Baby Powder again now the my wood forms are covered with epoxy resin. For some reason Baby Powder didn't work for me the last time I tried it, so I assumed it must have been absorbed somehow by the (then) uncoated wood forms.
CF |
|
Back to top |
|
 |
CrazyFool Expert

Joined: 07 May 2008 Posts: 203
|
Posted: Wed Jun 11, 2008 2:49 am Post subject: |
|
|
Still cranking out molds. It's amazing how easy (and FUN ) it is to make molds once you've moved beyond the troubleshooting phase. You're no longer worried about whether or not your mold will turn out... but how cool you can get it to look this time! It's also amazing what a difference plus or minus just 1 or 2 minutes under the ovens can make. That's the main reason why I'm starting pulls with completely cold ovens. So far I've found it difficult to measure droop/sag in the heated plastic sheet with any degree of accuracy. I can't quite tell if the plastic is at its optimum level of readiness simply by eyeballing how much it's drooping. One thing about 2'x4' sheets of 1/8" acrylic is that they are about $35.00 a piece, so I'm trying not to produce any unusable molds. If I start with cold ovens I can't get as many pulls in one day (because I have to wait for the ovens to cool down) but I think that I do achieve a better degree of accuracy by measuring the time as opposed to the droop. I've been wondering about installing a couple of laser pointers that crisscross under the drooping plastic sheet. With some kind of droop measuring device like laser pointers, after a while I might be able to accurately gauge how far the plastic is drooping by the ideal pulling time. Then maybe I can move away from tracking by time and just go by the droop (sag)... and as jegner wisely suggested, get many more pulls in one day by using already hot ovens.
CF |
|
Back to top |
|
 |
CrazyFool Expert

Joined: 07 May 2008 Posts: 203
|
Posted: Fri Jun 13, 2008 1:48 am Post subject: |
|
|
Very close to completing the first business sign.
It's hard to believe that these plastic molds (the same molds I was breaking and melting just a week ago!) are about to go up on a real business store front. And not only one store. These signs may go up on as many as 7 stores, with two signs at most stores... for a total of around 12 signs. They will be seen every day (night and day) by millions of people. It seems surreal. I've never done anything like this before. I simply mentioned to someone that I 'might' know how to make business signs with a process I'd read about called 'vacuform molding' and... suddenly... I was in the sign making business. The sign in these photos will be 3 feet tall and nearly 8 feet long!
I could not have done this without you guys.
CF |
|
Back to top |
|
 |
TK 109 Guru
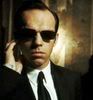
Joined: 11 May 2007 Posts: 712 Location: Galena, Ohio
|
Posted: Fri Jun 13, 2008 8:32 pm Post subject: |
|
|
dude, this is too cool. you've made a machine that can (and probably will) make you HUGE sums of money. i guess all of us could be making a bunch of bucks on this vacuum-forming stuff, eh?
i wish i could be as comfortable as you are about forming that suff. usually, i make some many mods to my stuff that i only seem to form a certain varaition of the same molds only once. and after every mod, forming becomes POTENTIALLY a little more difficult and so on... maybe it's just me...
anywho, what is this company name? i've been curious since the start of this thread. i simply can't wait how this turns out.
looking forward to your future projects, will be AWESOME to see.
p.s. make a vid. PLEAE make a vid! that would be awesome!!
keep forming, bro!  _________________ -Alex
-------------------------------------------------------
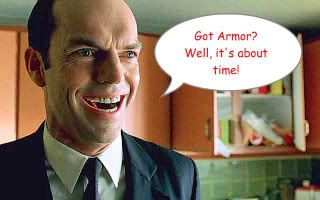 |
|
Back to top |
|
 |
TK 109 Guru
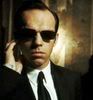
Joined: 11 May 2007 Posts: 712 Location: Galena, Ohio
|
Posted: Fri Jun 13, 2008 8:36 pm Post subject: |
|
|
about the droop:
tap with your fingers. when it's as bouncy as a wet paper towel in the oven, it's ready. the more it droops, and the "bouncier" it is, the TIGHTER the pull will be.
just my 2 cents.  _________________ -Alex
-------------------------------------------------------
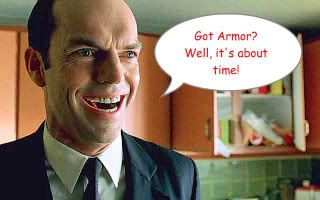 |
|
Back to top |
|
 |
CrazyFool Expert

Joined: 07 May 2008 Posts: 203
|
Posted: Sun Jun 15, 2008 8:04 am Post subject: |
|
|
*** !!!YEAH!!! *** WhooooHOooo...!!!
TK 109
Thanks man! It is weird to do a creative project and actually make money. I've done a few things in the past where I made a little bit of money but nothing like this.
It's probably best for me not to talk about the name of the company. I would not get into trouble but it could annoy my boss a little bit. Later, I will try to show as much as I can of the store front and the new signs when they go up so anyone who's interested can get a better idea of what I've been babbling about all this time.
Boy, the sign really comes to life when you apply the stickers. I just have one thing to say about vinyl stickers... it is some serious work to apply large vinyl stickers right without ruining them. Vinyl stickers for outdoor applications will stick to anything, and once they stick that's it! You get one shot. Thank God some chick who used to rent an apartment at the building I manage on the side complained so many times about her neighbors in the building next door. I never thought I would be glad that someone complained so much! But it led to me installing mirrored window tint in her living room - which was a total nightmare to do by myself because her windows were like 7 feet wide. Anyway, I would have destroyed all of the vinyl stickers for this sign project if it had not been for her endless complaints about guys next door hanging out on their balcony smoking cigarettes and looking into her living room. Because of that, I learned how to apply mirrored window tint using what's called 'The Wet Method'. (You know, it's getting to the point that whenever something annoying or bad happens I start looking for how it's going to pay off in the end!) Even the sign company who printed the stickers you see in the photo below did not know about the wet method. They use the dry method, which is awful. Here's a wet method YouTube video I like... http://www.youtube.com/watch?v=K1Vh4hObhVI
Vinyl stickers applied!!! Next step... Going up on a store front for millions of people to see!!
CF
P.S. What kind of video were you interested in seeing? Believe it or not with all the junk I've accumulated over the years the one thing I don't have is a video camera. My still camera can do grainy 30 second videos. I might try that when I get the chance.
P.S.S. I did not draw the logo. A few people have asked me about that. I did have to manipulate him digitally, and I did draw the letters so they would match existing letters in a portion of the old sign that will remain (I am replacing the old company logo and one word in their old signs).
P.S.S.S. I do try not to exaggerate. The sign really will be seen millions of times. I'd say at least 10,000 cars a day drive by the store this sign will go up on. (And there are 7 stores in this sign project.) It's possible that if they stay in business long enough not only will the signs be seen millions of times... they will be seen by millions of different people. Just FYI. The power you have at your fingertips with this vacuforming stuff is no joke. I want to thank jegner again for putting up this super web site... and the mods like crashmann, who make visiting the site so enjoyable. I'd also like to thank the academy, and my pet turtle 'Snake'.
Last edited by CrazyFool on Sun Jun 15, 2008 1:52 pm; edited 3 times in total |
|
Back to top |
|
 |
ahillworks Master

Joined: 18 Nov 2007 Posts: 308 Location: Orlando FL
|
Posted: Sun Jun 15, 2008 12:46 pm Post subject: |
|
|
Wow that is awesome man. I can not wait to get the nichrome wire on tuesday so I can do awesome things such as this project! Keep up the good work and can not wait to see what it looks like in store front. |
|
Back to top |
|
 |
crashmann Guru

Joined: 27 Sep 2005 Posts: 501
|
Posted: Mon Jun 16, 2008 12:10 am Post subject: |
|
|
And I thought the logo was a kangaroo!
Again, very impressive work you CrazyFool! In just over a month you have gone from a small comment to your boss, to producing finished product.
Thank you for documenting all of your work along the way - the successes and even more importantly, the developmental challenges (we don't want to call them "failures" ) Everyone on the board benefits from your progress on this project.
Three cheers for CrazyFool!!!
Charlie |
|
Back to top |
|
 |
TK 109 Guru
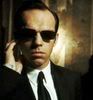
Joined: 11 May 2007 Posts: 712 Location: Galena, Ohio
|
Posted: Mon Jun 16, 2008 1:19 pm Post subject: |
|
|
hip, hip, HOORAY!
a vid of you forming, crazy fool, would be very cool!
hip, hip, HOORAY!
hip, hip, HOORAY! _________________ -Alex
-------------------------------------------------------
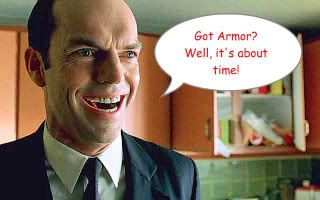 |
|
Back to top |
|
 |
|
|
You cannot post new topics in this forum You cannot reply to topics in this forum You cannot edit your posts in this forum You cannot delete your posts in this forum You cannot vote in polls in this forum
|
Powered by phpBB © 2001, 2005 phpBB Group
|